اتصل
هاتف
+0086-371-86162511
عنوان
تشنغتشو ، الصين
cost of ball grinding mill for nano size

High energy ball mills for nano-scale grinding
Factors like the choice of dispersion medium or grinding ball size have a crucial influence on the success of the process. Generally, small ball Work done at Tata Consultancy Services (TCS) has as its objective the production of particles in the nano-size range. They have used a planetary mill for this purpose and have found an apparent grind limit at a d50 of 100 nm. Media size is an important variable but all four sizes tested (0.6, 1, 2 and 3 mm) appear to suffer this grind Grinding to nano-sizes: Effect of media size and slurry viscosity
احصل على السعر
How the Nano Milling Process Works Blog
Nano mills are most efficient when the incoming particle size is smaller than the exit screen and no larger than the media. This means that the target particle distribution for pre-milling should be Nanomaterials refer to any materials having a particle size of 1–100 nm (10 −9 m). They have unique physical and chemical properties, which can be more advantageous as compared to their bulk structures (Le Brun et al. 1992).Nanotechnology is an interdisciplinary research field with many practical applications in the field of medicine, Synthesis of Nanofertilizers by Planetary Ball Milling
احصل على السعر
Grinding Efficiency Between Bead Mill and Ball Mill
This is because the rotational speed of the sand mill during the grinding and mixing process can reach 2800r/min, while the high-energy ball mill only reaches 1200r/min. Additionally, the zirconiaThis review is focused on the topical developments in the synthesis of nanocomposites using the simplest top-down approach, mechanochemical milling, and the related aspects of the interfacial interactions. Milling constraints include time duration of milling, ball size, the ball-to-sample content proportion, rotation speed, and energy that Applied Sciences Free Full-Text Recent Developments on the
احصل على السعر
Grinding to nano-sizes: Effect of media size and slurry viscosity
tive the production of particles in the nano-size range. They have used a planetary mill for this purpose and have found an apparent grind limit at a d50 of 100 nm. Media size is an important variableBall wet/dry media and jet mills are often used to reduce large particles to nanosize range 1-100 nm (Cho et al. 2009). Wet or dry milling methods would be used to make nanoparticles, and eachGrinding to nano-sizes: Effect of media size and slurry viscosity
احصل على السعر
Milling tests with the Fritsch Planetary Ball Mill fritsch.de
The Planetary Mill PULVERISETTE 5 premium line provides two stations of grinding bowls with 500 ml volume (largest capacity on the market). Each grinding bowl can be filled 1/3 part of the volume (± 170 gr sample). So, if we use two grinding bowls, the optimum capacity is about 170 x 2 = 340 g per milling process. 3.ball mills have also often been used for research studies (see Fig. 4: a m odified Retsch Planetary Ball Mills, PM 400 [28]. Several researchers have designed t heir own hi gh energy(PDF) Mechanical Milling: a Top Down Approach for the Synthesis
احصل على السعر
(PDF) DESIGN AND FABRICATION OF MINI BALL MILL
It is reduced to nano-size by means of planetary ball milling equipment. The size 473 nm is confirmed by particle size analyzer. Lab-scale. In this study, the nanostructured Al/Ni energeticWith the "Top-Down" method the particles are reduced to nanometer size by grinding. A suitable tool for this method is a planetary ball mill, such as Retsch's PM 100, PM 200 or PM 400, which provides the necessary energy input.Planetary Ball Mills for Nano-scale Grinding 2011 Wiley
احصل على السعر
Nanomaterials Free Full-Text High-Energy Ball Milling for High
The current production method of nanobiochar (NBC), an emerging, environmentally friendly nanocarbon material, is tedious and lengthy. Therefore, in this study we aimed to improve the productivity of NBC via high-energy ball milling by manipulating the grinding media and processing time. The particle size distribution of the resulting NBC The ball milling design significantly depends on the size of mill jar, required particle size distribution of powder and grinding media (balls) [13], [14], [15]. The main purpose of milling process is to obtain required particle size of the powder without any contamination, increasing the output of the milling circuit and overall reduction in Design, fabrication and performance analysis of mini ball miller
احصل على السعر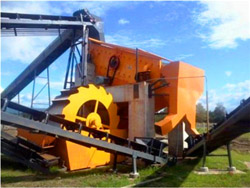
(PDF) Effects of Ball Size on the Grinding Behavior of Talc Using
High-energy ball milling at 2000 rpm produces ultrafine talc particles with a surface area of 419.1 m2/g and an estimated spherical diameter of 5.1 nm. Increasing the ball size from 0.1 mm to 2 mmCost Of Ball Grinding Mill To Produce Nano Size Particle. wet grinding machines with nano particles sizes producing . In materials processing a grinder is a machine for producing fine particle size P 80 is the mill circuit product size in and ore particles causes grinding of Get a Price Wet grinding mill,wet grinding mill manufacturer,wetnano particles grinding machine KOOKS
احصل على السعر
OPTIMIZATION OF MILLING PARAMETERS OF PLANETARY BALL MILL
The ball mills can be classified into two categories according to the axis of rotation of the bowl. 1. Vertical axis and 2. Horizontal axis. Figure 1 Direction of rotations of drums in (a) Vertical and (b) Horizontal axis ball mills In Vertical axis ball mill, the drum with material to be ground and grinding balls rotates aboutTherefore, we ground natural magnetite ore in a planetary ball mill and an agitator bead mill producing particles in the targeted size range. Applying ore particles ground from ~6 µm to 250 nm yields harvesting efficiencies comparable to synthetically produced nanoparticles (Ø ~ 10 nm), with only half the BET surface.Magnetochemistry Free Full-Text From Micro to Nano: Grinding
احصل على السعر
Ball milling as a synthesis method Aalto University Wiki
Ball mills can be classified into high-energy ball mills and low-energy ball mills by their rotation speed. Selection of certain ball mill depends on used technique; MA, MM or MD. However, some ball mills can be utilized for all three of these techniques. Table 2 presents the most common ball mills and their energy types. [1, p.26] [4] Table 2.In this study a metallurgical grade silicon quality was milled in a planetary ball mill and the properties of the powder were investigated as a function of grinding time, grinding bead size (20 mm(PDF) Effect of operation parameters and formulation on
احصل على السعر
Solids Choose the Right Grinding Mill Chemical Processing
Grinding time is related to media diameter and agitator speed via: T = KD 2 /N 1/2. where T is the grinding time to reach a certain median particle size, K is a constant that depends upon the material being processed, the type of media and the particular mill being used, D is the diameter of the media, and N is the shaft rpm. This equation shows that total
احصل على السعر- teebeek ashanti gold mines
- موضوع عن استعمالات المعادن في طب الاسن
- مصنع و مورد كسارات مصر
- خام جهاز الذهب
- easy to operategold grinding machine
- طاحونة الكرة ترس رمح تزييت
- كسارة الفك عالية الكفاءة في موسكو
- تستخدم limestone كسارة مخروط الموردين في indonessia
- crushers pakistan limestone
- اسعار ادوات البناء
- تخيط جاممه البصره محجر
- سحق قاعدة بيانات مصنعين
- non contact type crushing jaw crusher pe cost in nigeria
- موردون لآلات المحاجر في اليمن
- كسارة فكية مستعملة للبيع جنوب ماليزيا