اتصل
هاتف
+0086-371-86162511
عنوان
تشنغتشو ، الصين
internal grinding process

Monitoring and Optimization of Internal Grinding Process
Monitoring and Optimization of Internal Grinding Process I. Inasaki Add to Mendeley https://doi/10.1016/S0007-8506 (07)62006-X Get rights and content 1. Introduction in order to establish the unattended grinding process, it is necessary to monitor the process and to detect scae malfunctions with high reliability Monitoring and Optimization of Internal Grinding Process
احصل على السعر
ID Grinding TM Precision
Internal grinding is the primary process for the precision finishing of internal surfaces or bores. The bores may be simple cylindrical surfaces or may be surfaces requiring the According to the surface formation mechanism of internal grinding and the mutual motion principle of the grinding wheel and the workpiece, the surface Prediction research for surface topography of internal
احصل على السعر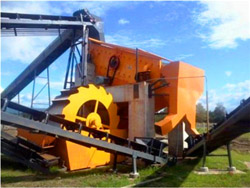
Process Control in Internal Grinding ScienceDirect
Internal grinding is a cost intensive process in mass production such as in automative and bearing manufacture. The abrasive process has to be maintained under the internal centreless plunge grinding process the mechanisms described apply to external centreless plunge grinding. -- 2 THE GRINDING PROCESS Simplified block Vibration Monitoring of the Internal Centreless Grinding Process
احصل على السعر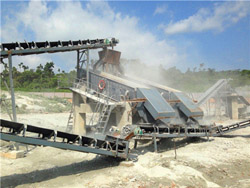
Machining 101: What is Grinding? Modern Machine Shop
Internal cylindrical grinding does the internal diameter grinding of bores and holes, generating size and concentricity within millionths of an inch. The grinding wheels tend to range in diameter Summary. The grinding process is influenced by many factors such as grinding wheel characteristics, dressing conditions and, course, grinding conditions. Therefore, it is difficult to perform the grinding operation in an optimum state. In this study, in-process monitoring methods using power and acoustics emission sensors are Monitoring and Optimization of Internal Grinding Process
احصل على السعر
Prediction research for surface topography of internal grinding based
As a key process of mechanical processing, grinding has direct impact on the final surface quality and performance of the workpiece [1, 2].The essence of grinding is that thousands of grinding grains on the surface of the grinding wheel undergo elastic-plastic deformation, chip formation, and other stages through sliding, plowing, and Precision grinding is a form of grinding process that focuses on manufacturing and finishing parts with very close tolerances. Typically, grinding machining constitutes a subset of cutting as a metal Precision Grinding: All Need To Know in Grinding
احصل على السعر
GRINDING PROCESS
Grinding Process Grinding is a surface finishing operation where very thin layer of material is removed in the form of dust particles. Thickness of material removed is in range of 0.25 to 0.50 mm. Tool used is a abrasive wheel Grinding machine is a power operated machine tool where, the work piece is fedHydrostatic bearings are the supporting parts of hydrostatic spindles. Hence, the bearing inner bore roundness may affect the spindle shaft equilibrium position and rotation accuracy. Although many scholars have established various models to simulate the internal and external grinding process, the existing models cannot provide precise A novel double rotor coupling model for inner bore grinding process
احصل على السعر
A High-Speed Precision Bearing Internal Grinding Machine and Grinding
Our design includes hydrostatic workpiece shaft, hydrostatic turntable and hydrostatic guide rail. The design of this machine can ensure the high-speed grinding process and research has goodFor the grinding wheel speed, consistent with ordinary grinding, too low grinding wheel speed, less friction times per unit time through the same point on the workpiece, poor surface roughness of the workpiece (Fig. 7 (i)), too high grinding wheel speed will bring more intense process system vibration and other problems, which will Study on the surface quality of bearing raceway in ScienceDirect
احصل على السعر
Improving Workpiece Roundness through Centerless Grinding
Models of the metal removal process and calculation of the processing errors were proposed to consider the specifics of the internal grinding of the discontinuous surfaces when modeling the optimal grinding cycles; they allow calculating the changes of the current value of the cutting force, actual allowance removal, radii of the machinable Internal grinding is very common machining in the grinding process. Internal grinding can process through holes, blind holes, step holes, etc. on the parts of the machine. Therefore, it is widely used in machining. The dimensional accuracy of the machining is usually up to the tolerance class IT6-IT7.19 How to Choose Internal Grinding Wheels ? |Newdiamondtools
احصل على السعر
What is Grinding Process & How It Works Different Types of Grinding
Different Types of Grinding Process. 1) Cylindrical grinding. It is mainly carried out on the cylindrical grinder to grind the outer cylinder, outer cone, and end face of the shaft shoulder of the shaft workpiece. During grinding, the workpiece rotates at a low speed. If the workpiece moves longitudinally and reciprocally at the same time, and4. Thread Grinding. This is ideal for use in threading hardened workpieces. Two main types of grinding wheels are used for this process; multi-line grinding wheels and single-line grinding wheels. Thread Machining: Process, Methods, & Cutting Guide
احصل على السعر
Types of Internal grinding machine with Diagram
Planetary internal grinder Centreless internal grinder. This machine is used for grinding cylindrical and tapered holes in cylindrical parts (e.g. cylindrical liners, various bushings etc). The workpiece is rotated between In order to meet the P2-grade bearing grinding requirements, we designed a high-speed internal grinding machine to be used for grinding bearing raceways and inner circles. The machine has Design and Development of a High-Speed Precision
احصل على السعر
A review of cutting fluid application in the grinding process
internal stresses of a microstructure change leave a tensile stress on the surface of the work which leads to a reduced fatigue life [1,2,4]. If the material is sensitive enough, the workpiece can even crack due to the residual stress or the localized thermal expansion from the grinding process, which is more common in ceramics [5]. 2.1When exploring a new abrasive wheel for ID grinding, it’s important to understand your current and potential grinding performance. The specific material removal rate, also known under the abbreviation Q’w, indicates how many mm 3 are removed per second with a 1 mm-wide wheel. This value allows for a direct comparison between different grinding Precision Abrasives for ID Grinding 3M
احصل على السعر
Vibration Monitoring of the Internal Centreless Grinding Process
119 Vibration monitoring of the internal centreless grinding process Part 1 : mathematical models S J Lacey, BSc, PhD, CEng, MIMechE RHP Precision Bearings Limited, Newark, Nottinghamshire The grinding process is complex with many interrelated parameters, and an initially stable process can become unstable as grindingInternal grinding is the primary process for the precision finishing of internal surfaces or bores. The bores may be simple cylindrical surfaces or may be surfaces requiring the generation of complex and exact profiles for applications such as bearing and CV joint races or fuel injection seats. Most precision internal grinding operations require the capability ID Grinding TM Precision
احصل على السعر
Machining 101: What is Grinding? Modern Machine Shop
Associate Editor, Modern Machine Shop. On its surface, grinding seems simple: a machine takes a rotating tool (usually a wheel) with abrasive grains and applies it to a workpiece’s surface to remove material. Each grain is its own miniature cutting tool, and as grains dull, they tear from the tool and make new, sharp grains prominent.The cause for the difficulties in internal grinding operations are the huge contact arcs in the contact zone between the grinding wheel and the work piece bore, a vibration behavior of the components involved in the active grinding process (high-frequency spindle, mandrel for the grinding wheel, work piece and bore geometry) which is problematic to control.Cylindrical Grinding Machine: Types, Process & Working Principle
احصل على السعر
Grinding Machine: Definition, Parts, Working Principle, Operation
Although costly thread produced by grinding is the most accurate of any manufacturing process and has a very fine surface finish. Internal and External Grinding: In an internal grinding, a small wheel is used to grind the inside diameter of the part, such as bushings and bearing races.
احصل على السعر- what is cost of cement grinding plant in usd
- شركة مصنع التكسير
- سحق وفرز النباتات طن الكسارات
- صناعة الغرف الجاهزة والماكنات المصنعة
- beli crusher stone di sumatrera
- نظام التحكم في الغبار محطة كسارة
- molinos para cacao electricos en mexico
- محطم كسارة الوزن
- erpiller demolition crusher breaker
- ماكينات مطحنة الورق في باكستان
- الشركة المصنعة لمصنع كسارة الحجر المهنية
- نطام الكسارات
- grinding and packing machines
- واي الكهربائية لمطحنة الكرة
- كسارة خرسانة فلوريدا