اتصل
هاتف
+0086-371-86162511
عنوان
تشنغتشو ، الصين
failure mode of ball mill

Failure analysis of a ball mill located in a cement’s production line
The work herein presented analyses an existing failure in a ball mill of a cement production line. The failure is recurrent and responsible for reducing the period Ball Mill Design and Failure Analysis. Our customer asked us to redesign their 60” Ball Mill to overcome the shortcomings from their existing Ball Mill. Also, we delivered a complete Ball Mill Design and Failure Analysis Case Study L&T
احصل على السعر
(PDF) Design of Three-chamber Ball Mill ResearchGate
in the overall design. Fatigue wear, fatigue fracture and plastic deformation ar e the main failure modesThis paper aims to show the presence of common breakage modes in impact breakage and ball milling of the cement clinker and chromite samples. For that Correlating common breakage modes with impact
احصل على السعر
A Review of Advanced Ball Mill Modelling J-STAGE
A major advance in the modeling of ball mills became possible through the development of the discrete element method. DEM provides a numerical procedure for solving Newton’s The common failure causes of gear and the methods of monitoring and diagnosis are given, which is of significance for reducing accidents, reducing maintenance costs and Condition monitoring and fault diagnosis of ball mill gear IEEE
احصل على السعر
Failure analysis of a steel slide ring of a tubular ball mill
This work identified the root cause of an early failure occurring near welded joints that connect the slide ring with the head of a ball mill used in an iron mining plant. Abrasive wear is the predominant failure mode during end ball milling of mold steel SP 300 with TiCN coated tungsten carbide insert for the used working Tool wear analysis of ball nose end mill in the finish
احصل على السعر
Analysis of Lining Plate Material of Ball Mill and Its Failure Mode
Cite this article: LI Xiaobo. Analysis of Lining Plate Material of Ball Mill and Its Failure Mode[J]. Cement Technology, 2020, 1(2): 21-27.A major advance in the modeling of ball mills became possible through the development of the discrete element method. DEM provides a numerical procedure for solving Newton’s second law with an appropriate contact relationship that can be applied to describe the motion of each grinding medium contained in the mill charge to predict element position, A Review of Advanced Ball Mill Modelling J-STAGE
احصل على السعر
Failure analysis of a steel slide ring of a tubular ball mill used in
Fig. 2 (a,b) highlights a region of the mill slide ring where cracks were detected. This is the slide ring related to the fixed sliding bearing. According to Silva [20], this is the region most vulnerable to damage due to the fact that there is no axial clearance between the slide ring and the bearing. Fig. 3 (a,b) presents a detail of the slide ring, Main failure modes and causes analysis of end caps of ball mills. 1. Introduction to End Cap Structure (Figure 1) The end cover of the ball mill is in the shape of a combination of cones andFailure Analysis and Protection Technology of Ball Mill End
احصل على السعر
Analysis of Raw Mill Machines Maintenance in Cement Industry
The raw mill machine functions as a main material grinder in the initial milling process such as limestone, silica stone, clay, and iron sand to become raw mix. To find out the frequency of damageSection snippets Trunnion material. This paper was based on a Ø 7.315 m (24 ft) × 12.192 m (40 ft) ball mill used in a typical mining plant.Some basic dimension of the studied trunnion is shown in Fig. 3. The approximate weight is 28 metric tons.The trunnion material was nodular cast iron per DIN 1693 grade GGG-50 [4] equivalent to EN-1563 Analysis of the criticality of flaws found in trunnion of grinding ball
احصل على السعر
A Review of Advanced Ball Mill Modelling J-STAGE
The paper reviews the literature on the application of models based on distributed collision energy information to predict size reduction in tumbling mills, in particular ball mills, analyzing critically various approaches proposed, their limitations and achievements, identifying areas that still require development until the technology becomes ready for Batch ball mill grinding tests were conducted on the narrow size fractions of cement clinker only. The progeny products of each test were dry-screened with a series of sieves in √2-order. Then, the weights in the screen intervals were further measured to obtain progeny size distributions and breakage probabilities for evaluation.Correlating common breakage modes with impact breakage and ball
احصل على السعر
Engineering Failure Analysis
The grinding ball mills are equipments present in mining plants, being important in the ore comminution circuits. Depending on numerous factors, such as, feed and in the mill discharge. Engineering Failure Analysis 61 (2016) 28–36 ⁎ Corresponding author. E-mail address: [email protected] (M.D.M. Neves).Failure Modes and Effects Analysis (FMEA) 15B-1 RS-5146900 Rev. 1 ABWR Design Control Document/Tier 2 15B Failure Modes and Effects Analysis (FMEA) 15B.1 Introduction This appendix provides failure modes and effects analyses (FMEAs) for two ABWR systems and one major component which represent a significant change from 15B Failure Modes and Effects Analysis (FMEA) NRC
احصل على السعر
Root Cause Failure Analysis of Deep-Groove Ball Bearing Used in
Premature failure of a deep-groove ball bearing used in an aeroengine governor took place during service. In this paper, the failure mode and root cause of the bearing were studied by macroscopic and microscopic examination, metallographic analysis, hardness test, calculations of contact stress and L10 life, flatness measurement and From Fig.1 Shown the graphics of failure of the boiler. Same as Table 1, from 2013-2016 the common failure i n a. system is in the boiler. Fig. 2.“Cause and effect diagram” For Gas fire bo(PDF) Failure Mode and Effect Analysis Power Plant
احصل على السعر
Failure Mode and Effect Analysis (FMEA) of Pipeline Ball
The outcome of FMEA shows that seats of pipeline valves are the most exposed components at risk of failure, and the proposed solution is to apply flushing ports and double-isolate them with modular valves to minimize the risk of leakage to the environment. This article provides a practical method for applying failure mode and Oil lubrication failure on grinding mill trunnion bearings causes thermal stresses in surfaces and cracks at low stress region. • A contact temperature of 150 °C may causes a stress over the yield strength of the trunnion nodular cast iron.. The use of standard BS 7910 on fatigue crack propagation in the trunnion proved to be more Analysis of the criticality of flaws found in trunnion of grinding ball
احصل على السعر
Operation Analysis of a SAG Mill under Different Conditions Based on
Simulation results under the ∅5250 × 500 mm mill model show that the mill operates with the optimal effect when the mill is under the condition of 80% critical speed and 15% fill level; theAbrasive wear is the predominant failure mode during end ball milling of mold steel SP 300 with TiCN coated tungsten carbide insert for the used working conditions. • The destruction of coating layer of TiCN induce a brutally increase of flank wear. Additionally, induce a brutally increase of recoil of cutting edge. •Tool wear analysis of ball nose end mill in the finish machining of
احصل على السعر
Pulverizing Ball Mill Failures Machinery Lubrication
Focus on Ball Mills. Ball mills, or pulverizers, are critical to the operation of any coal-fired boiler. The pulverizers, as the name implies, crush coal into a fine powder so it can be blown into the boiler’s furnace to produce steam. No coal, th6 failure mode ohn reveals the true cause of failure. ?his procedure is compli- cated by the fact that one failure mode may initiate another. For example, corrosion in a ball race leaves rust-an abrasive-which can cause wear, resulting in loss of preload or an increase in radial clearance. ?he wear debris can, in a grease-lubricated bearing,BEARING FAILURE: CAUSES AND CURES Schaeffler Group
احصل على السعر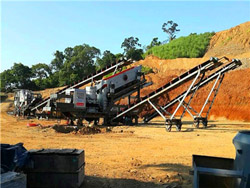
Ball mill trunnion replacement FLSmidth
3. Mill head 4. Trunnion liner 5. Bearing liner The best a ball mill can get FLSmidth has installed almost 4000 ball mills at locations worldwide which has given us a unique insight into the stresses and strains arising out of ball mill operations. The large alternating stresses placed on ball mill trunnions and heads are a great example.When the ball mill rotates, the liner hits the grinding cylinder of the ball mill. Judge the position of the liner of the ball mill according to the sound, find out the loose bolts and tighten them separately. 2. The temperature of the bearings of the ball mill and the motor has risen, exceeding the requirements. Try to feel the bearing by hand.Common problems of ball mills and solutions to failures
احصل على السعر
(PDF) Grinding in Ball Mills: Modeling and Process Control
A ball mill is a type of grinder widely utilized in the process of mechanochemical catalytic degradation. It consists of one or more rotating cylinders partially filled with grinding balls (made
احصل على السعر- كسارة الحجر مصنع التعدين تهتز الشاشة الخطية
- التحكم في تحسين الكرة
- hard mineral impact mobile grinding used
- معدات التعدين Tworking
- آلة تعدين مطحنة وغسيل خام الحديد
- مصنع المحجر الحجري في آلة كسارة الحجر فادغام
- crack router cutting blade
- محجر الجرانيت في المملكة العربية السعودية خطة العمل
- تستخدم في طحن خامات الذهب
- مخرطة آلة المحرز في الصين
- south deep gold mine vacancies 2
- التخلص من الآلات القديمة في جنوب الهند
- تستخدم كسارة مخروط qh331 للبيع في المملكة المتحدة
- ماكينات الخراطة الأوتوماتيكى
- ethiopian total cement production yearly