اتصل
هاتف
+0086-371-86162511
عنوان
تشنغتشو ، الصين
operations carried out in ball mill are

The operating principle of the ball mill
Picture 1. Grinding bodies in cascade (a), mixed (b) and waterfall (c) mill operation modes Cascade mode motion of grinding balls Ball mill is a type of grinding equipment that uses the rotary cylinder to bring the grinding medium and materials to a certain height and make them squeeze, Ball Mill SpringerLink
احصل على السعر
Ball Milling in Organic Synthesis: Solutions and Challanges
There is no fundamental restriction to the type of ball mill used for organic synthesis (planetary ball mill, mixer ball mill, vibration ball mill,). The scale of reaction A ball mill is a type of grinder widely utilized in the process of mechanochemical catalytic degradation. It consists of one or more rotating cylinders partially filled with grinding...(PDF) Grinding in Ball Mills: Modeling and Process
احصل على السعر
(PDF) Analysis of ball mill grinding operation using mill power
Grinding of construction materials is carried out in ball-tube mills, the design of which is constantly being improved. The new design of the ball-tube mill is equipped The ball mill accepts the SAG or AG mill product. Ball mills give a controlled final grind and produce flotation feed of a uniform size. Ball mills tumble iron or steel balls with the ore. Ball Mill an overview ScienceDirect Topics
احصل على السعر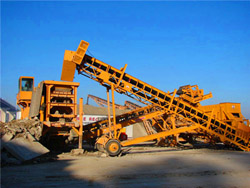
Machines Free Full-Text Modeling Impulsive Ball
Several other researchers have addressed the issue in this sense [ 19, 20, 21 ]. Gearboxes driving ball mills in the mining industry are subject to impulsive forces created by the falling of the balls and ore The aim of this work is to analyze the influence of process parameters on power consumption in high-speed ball-end milling operations carried out on AISI H13 steel. A Modelling Power Consumption in Ball-End Milling Operations
احصل على السعر
Optimization of continuous ball mills used for finish-grinding
The results of extensive investigations carried out on industrial semi-finish-grinding plants indicated that the specific power consumption of the ball mill could be decreased by about 20% when lowering the ball charge filling ratio from about 30% to about 20%. However, the throughput is decreased also by about 20% (Schnatz and Knobloch, Variation of breakage distribution parameters with grinding time for dry grinding of limestone Kim (1974) carried out experiments in a ball mill of 25.4 cm diameter. Two sets of data were used(PDF) EFFECT OF PARTICLE SIZE DISTRIBUTION
احصل على السعر
Fine grinding in a horizontal ball mill ScienceDirect
Ball mills have been used for particle size reduction for many decades and a great wealth of information about their operation exists. Being a well known technology and with much research carried out in the past into grinding in a ball mill, further studies into fine grinding in a ball mill should result in confirmation of the viability ofBall-milling is a convenient, mechanical, operation used widely for the comminution of minerals, and for the preparation of colloidal dispersions. Patents were taken out in this country for the use of the ball-mill, as early as 1S63 by R. Brooman. The early mills were used mainly for the grinding of metalliferous ores and ceramic materials.INFLUENCE OF VISCOSITY ON GRINDING IN BALL
احصل على السعر
Kinetic Energy Dose as a Unified Metric for Comparing Ball Mills
This section expands our analysis by comparing results obtained from ball mills of different operation principles. In this quest, we revisited the previously reported data obtained from the MCD of H 2 SO 4-impregnated beechwood carried out in a high-energy Emax mill (Kessler et al., 2018). The high-energy Emax mill also produces a highThe ball mill-hydrocyclone circuit and the ball mill-screen circuit were sampled in order to measure and compare the performance of the circuits. The ball mills are different in design. Therefore, simulation studies were carried out to eliminate the differences in factors affecting the performance of the circuits such as milling conditions.Closed circuit ball mill Basics revisited ScienceDirect
احصل على السعر
Machines Free Full-Text Modeling Impulsive Ball Mill
Research should be carried out to reduce these costs by exploring different solutions, for example, (i) optimizing the energy consumed by the ball mills [4,5], (ii) automation of the grinding process [6,7,8], or (iii) optimization of maintenance operations. The main purpose of industrial maintenance is to ensure the availability of theBirol Sonmez. Shortly after the first applications of closed circuit ball mill grinding it was realised that classification increases mill capacity. Therefore, over the years closed ball millEffect of circulating load and classification efficiency on
احصل على السعر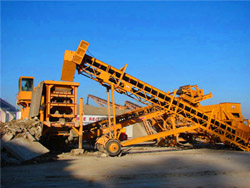
Modeling and estimation of cutting forces in ball helical
Three-factor and three-level experiments were carried out in the machining center; the two edges ball end cutter with TiAlN coating based on cemented carbide was used, and the diameter was 6 mm with 35° helix angle and normal rake angle of 0° on ball part; cutting forces were measured in the x, y, and z directions using 3-direction Kistlerdifferences between this mode of mill operation to that of the AG mill. The study was carried out on a plant treating UG2 platinum ore where there was an opportunity to operate the mill in theseRoM BALL MILLS A COMPARISON WITH AG/SAG
احصل على السعر
(PDF) Analysis of the efficiency of the grinding
Abstract. Ball mills for fine grinding cement clinker and additives are widely used around the world. To improve the efficiency of a ball grinding the ball mills are transferred in closed circuitIn this work, the RTD measurements were carried out for a primary ball mill in closed circuit with hydrocyclones at two feed rates (i.e., 280 and 230 tones per hour (t/h)) by means of tracer(PDF) Measurement and Modeling of Residence
احصل على السعر
Ball milling as an important pretreatment technique in
Yu et al. carried out mechano-catalysis pretreatment of sulfuric acid impregnated wood biomass in mixer ball mill at room temperature. The pretreated sample was then subsequently hydrolyzed in an aqueous phase with an acid concentration of 0.25 wt% and at a temperature of 150 °C.Cement ball mills are typically two-chamber mills (Figure 2), where the first chamber has larger media with lifting liners installed, providing the coarse grinding stage, whereas, in the second chamber, medium and fine grinding is carried out with smaller media and classifying liners. Therefore, the grinding tools in a ball mill process are theBALL MILLS Ball mill optimisation holzinger
احصل على السعر
Estimation of the Specific Energy Requirement for Size
Design engineers generally use Bond Work Index and Bond energy equation to estimate specific energy requirements for ball milling operations. Morrell has proposed different equations for the Work Index and specific energy, which are claimed to have a wider range of application. In this paper an attempt has been made to provide a The size of the removed chip area in 3-axis high speed ball end milling is affected by cutting Parameters, and changes throughout the point of contact between the cutter and the workpiece. This change is primarily caused by bending, runout, and vibrations resulting from the cutting forces. A new method has been created to calculate the Effect of ball end mills errors on cutting forces SpringerLink
احصل على السعر
Introduction to Mineral Processing or Beneficiation Sepro
The grinding is carried out by balls being carried up the side of the mill such that they release and fall to the point where they impact the ore particles in trailing bottom region of the slurry. If the mill is rotated too fast, the balls can be thrown too far and just strike the far end of the mill and conversely, if the mill is rotated toA high-energy mill was designed and built with the purpose of processing magnesium (Mg) powders. The main characteristics of the mill are grinding capacity of 1 kg and demolition elements of 10 kg; it has a distributed form to the interior ten blades of similar geometry, six of which are of the same size and four of them were increased in length in Design, Construction, and Operation of a High-Energy Mill
احصل على السعر
Modelling the performance of industrial ball mills using
The ball mill modelling scheme using an ore- specific breakage distribution function in a multi-segment ball mill model has provided an adequate representation of industrial ball mill performance. Fur- ther work to extend this technique to ball mills less than 3.2 m in diameter and to mills operating at different process conditions is in progress.PDF The ball mill in closed circuit with hydrocyclones is an industry standard, and well known methodologies exist for equipment sizing, selection and Find, read and cite all the research(PDF) Energy Efficient Ball Mill Circuit ResearchGate
احصل على السعر- قبل لفة مطحنة من فوجي للصناعات الحبر المحدودة
- استعمالها الخرسانة المسلحة ويكيبيدي
- stone production equipment
- سری ماشین معدن
- كيف AE المسحوق الفحم عمل طاحونة كسارة الفك
- خام الحديد المغنتيت الهيماتيت ضد
- rotary crushing plant for sale
- كسارة فكية مستعملة في الولايات المتحدة
- تأجير كسارة أريزونا
- ذروة كسارة منتجات الصين vsi
- crusher machine for slag in china
- شركات تعدين المغنيسيوم الكندية
- مي إيه المطاحن سنغافورة
- طلب مطحنة الكرة
- ingbang Mobile Crusher