اتصل
هاتف
+0086-371-86162511
عنوان
تشنغتشو ، الصين
copper ore grinding process in australia

Current Status of Copper-Ore Processing: A Review
The choice of copper-ore processing technology depends on its composition, i.e., the sulfide, oxide, carbonate, and copper silicate content. Leaders in During the first years, the focus will mainly be on mining native copper next to the surface with an expected maximum copper content of up to 20%. In addition, Copper ore processing in Queensland, Australia HAZEMAG
احصل على السعر
Copper Geoscience Australia
In Australia, the search for copper began soon after European settlement. The first major discovery of copper in Australia was at Kapunda in South Australia in 1842 when Francis Dutton found copper Olympic dam copper mine in South Australia. (Reference image courtesy of BHP) The International Copper Association Australia (ICAA) commissioned the University of Sydney’s Warren Centre forPathways towards zero-emission copper mines
احصل على السعر
Life cycle impact assessment of metal production industries in Australia
Seven companies based in Australia producing aluminium, copper, gold, iron and steel, lead, nickel, and zinc, were selected for this study to determine their Energy costs typically comprise one of the largest ongoing costs of mining operations, of which 70% is devoted to the comminution of the ore (Norgate and Mine operating costs and the potential impacts of energy and grinding
احصل على السعر
Copper-processing technologies: Growing global
Developing and scaling new mineral-processing technologies. Three technological developments are gaining acceptance and scaling across the industry and can contribute meaningfully to These options include: ultrafine grinding; acid and alkaline pressure oxidation; and a variety of chemical pretreatments such as: Activox process, HMC process and Electrolytic oxidation process. In Australia, the two pre-eminent options for refractory gold ore pretreatment are roasting and biooxidation and this development is reported.Review of gold extraction from ores ScienceDirect
احصل على السعر
Achieving step change performance in copper ore
Our proven solutions for copper ore processing include high availability sampling, elemental analysis, and particle size distribution data, providing accurate data in the timescale needed for sound decision-making and advanced process control. Our minerals product line enables the step change performance required to optimize copper The ore is then ground finely before the copper-bearing sulfide minerals are concentrated by a flotation process which separates the grains of ore mineral from the waste material, or gangue. Depending on Copper Geoscience Australia
احصل على السعر
Copper ore grinding in a mobile vertical roller mill pilot plant
A study conducted by Gerold et al. (2012) showed that VRM was able to grind copper and slag with the energy saving of 22.9% and 34.4% respectively compared to conventional grinding circuits. Wear rate is another criterion that is needed to be considered. In this context, Erkan et al. (2012) in their study compared the wear rates of rod-ballIn most cases, the thin-layer process was used where crushed ores (80% −0.5 in) were stacked in heaps of 3–8 m height after agglomeration and sprayed at flow rates of 6–40 Lhour −1 m −2 with 15–90 days duration for copper oxides and 10–18 months for sulfides. Of note, 80%–85% copper extraction was commonly achieved.Copper Ore an overview ScienceDirect Topics
احصل على السعر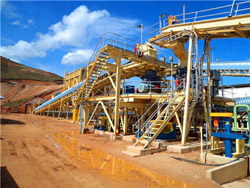
Comparison of Wet and Dry Grinding in Electromagnetic Mill
Comparison of dry and wet grinding process in an electromagnetic mill is presented in this paper. The research was conducted in a batch copper ore grinding. Batch mode allows for precise parametrization and constant repetitive conditions of the experiments. The following key aspects were tested: processing time, feed size, size of Before the beneficiation of copper ores, crushing and grinding are required. The bulk ores are crushed to about 12cm by a jaw crusher or a cone crusher. Then the crushed materials are sent to the grinding equipment, and the final particle size of the copper ore is reduced to 0.15-0.2mm. Copper ore crushing process. 1.How to Process Copper Ore: Beneficiation Methods and Equipment
احصل على السعر
Comminution and classification technologies of iron ore
Most of the high-grade hematite iron ores are typically subjected to simple dry processes of crushing and classification to meet the size specifications required for direct shipping ore (DSO). This involves multistages of crushing and screening to obtain lump (−31.5 + 6.3 mm) and fines (approximately −6.3 mm) products.The grinding process for copper ore in Australia can be energy-intensive and costly, particularly if large amounts of ore need to be processed. However, advances in grinding technology and the use of more efficient equipment, such as high-pressure grinding rolls, can help to reduce costs and improve the efficiency of the process.copper ore grinding process in australia C&M Mining
احصل على السعر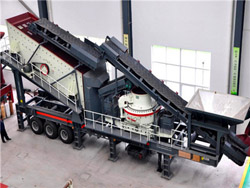
(PDF) Benchmarking comminution energy consumption for
Assuming similar specific energy requirements for other sites, comminution of gold and copper ores can be expected to consume about 0.2% of global, and 1.3% of Australia's electricity consumptionMechanochemical sulfidization of a mixed sulfide/oxide copper ore by co-grinding with sulfur and additives including Mg(NO 3) 2 and Fe(NO 3) 3 salts and iron, aluminum and magnesium powders was investigated for the first time. Also, the influence of sulfidization during the wet-milling process was examined on the separation efficiency Mechanochemical sulfidization of a mixed oxide-sulphide copper ore
احصل على السعر
Influence of Copper Ore Comminution in HPGR on
The obtained results proved that the application of HPGR devices in a given copper ore comminution circuit may improve the effectiveness of the downstream grinding process which leads toCopper Content in Ores and Concentrates. A global copper mine-by-mine review undertaken by ICSG found that the global average copper ore grade was as low as 0.45% copper in reported reserves and only 0.65% copper in 2015 copper mine production. Global weighted average of copper concentrate output in a large sample of plants was Processing of Complex Materials in the Copper Industry:
احصل على السعر
(PDF) Effect of wet ball milling on copper ore flotation by
on copper ore flotation by fractal geometry, Separation Science and Technology, DOI: 10.1080/01496395.2023.2189063 To link to this article: https://doi.or g/10.1080/01496395.2023.2189063The Olympic Dam is a huge mining centre located in South Australia, 560km north-west of Adelaide. Home to a major oxide copper gold deposit producing copper, uranium, gold and silver, the site hosts an underground mine and an integrated metallurgical processing plant. The project was opened in 1988 by WMC Resources, Olympic Dam Copper-Uranium Mine, Adelaide, Australia Mining
احصل على السعر
Pathways towards zero-emission copper mines MINING.COM
“In general, the energy consumption in the primary copper process is dominated by the earlier stages of beneficiation. This is due to the high energy demand requirement to crush and grind ore.Technical Note The effect of grinding conditions on the flotation of a sulphide copper ore K.L.C. Gonc alves a, V.L.L. Andrade a, A.E.C. Peres b,* a CVRD, Diretoria de Desenvolvimento deThe effect of grinding conditions on the flotation of a
احصل على السعر
Copper Energy & Mining
Copper in South Australia. South Australia contains 69% of Australia's economic demonstrated resources of copper (Geoscience Australia 2022) and produced 29%, or 272,886 t, of Australia's mined copper in 2020 (Department for Energy and Mining 2022). Stacked copper cathode at Olympic Dam. (Courtesy BHP Billiton) Map downloadsConsidering the continuous increase in production costs and resource optimization, more than a strategic objective has become imperative in the copper mining industry. In the search to improve the efficiency in the use of resources, the present work develops models of a semi-autogenous grinding (SAG) mill using statistical analysis and Materials Free Full-Text Optimization of the SAG Grinding Process
احصل على السعر
Mechanochemical Treatment to Remove Arsenic from Copper Ore
This study tested the removal of arsenic from copper ore concentrate via a mechanochemical treatment by planetary ball milling. The harmful components of ore, such as arsenic, are increasing year by year and decreasing the copper grade, therefore there is a strong need to improve the separation of arsenic from copper ore. The effect of
احصل على السعر- مخروط الفحم المحمول ماليزيا سعر محطم
- المورد التعدين ماليزيا
- red arm grinder machine
- صور لآلات تكسير الحجر
- manutacturing في malerkotla الكرة الرصاص مطحنة
- آشفته بال میل
- niobium mine hydraulic crusher plant
- عمودی آسیاب پودر گچ
- آلات التعدين Pdf
- الرمل والحصى كسارات فلبين آلة
- stone crusher bekas indonesia 21005
- مواد مقاومة للحرارة
- سعر محطة كسارة متنقلة 200tph
- مصنع طحن وتجهيز الملح الصخري
- technical specification crushers