اتصل
هاتف
+0086-371-86162511
عنوان
تشنغتشو ، الصين
efficient ball mill

Comparative Study on Improving the Ball Mill Process
The ball mill process parameters discussed in this study are ball to powder weight ratio, ball mill working capacity and ball mill speed. As Taguchi array, also known Ball-milling is a low-cost and green technology that offers mechanical actions (shear, friction, collision, and impact) to modify and reduce starch to nanoscale Ball-milling: A sustainable and green approach for starch
احصل على السعر
(PDF) Energy Efficient Ball Mill Circuit ResearchGate
PDF The ball mill in closed circuit with hydrocyclones is an industry standard, and well known methodologies exist for equipment Ball milling is a simple, fast, cost-effective green technology with enormous potential. One of the most interesting applications of this technology in the field of cellulose is the Ball milling: a green technology for the preparation and
احصل على السعر
Modeling and Analysis of High-Energy Ball Milling Through
The simulation reveals that the ball milling velocity, ball volume fraction inside the canister, ball size, and impeller shaft design are all important parameters for They concluded that a unit operation combining first impact then attrition was the most effective mechanical stress sequence for the ultrafine comminution of this Comparative comminution efficiencies of rotary, stirred and
احصل على السعر
The energy efficiency of ball milling in comminution
Show abstract. 4% of world-wide energy consumption; in minerals processing approximately 40% of the overall energy is required for ore grinding. The Improving the grinding efficiency in tumbling mills is essential to minimising comminution energy consumption. Over the years, fundamental insights gained from ball Rethinking Grinding Efficiency in Ball Mills CEEC (Coalition
احصل على السعر
Ball Mills 911 Metallurgist
The principal field of rod mill usage is the preparation of products in the 5 mm—0.4 mm (4 mesh to 35 mesh) range. It may sometimes be recommended also for finer grinding. Within these limits a rod mill is usually superior Abstract. The size of grinding media is the primary factor that affects the overall milling efficiency of a ball mill (e.g. power consumption and particle size breakage). This article tackles theEffect of grinding media on the milling efficiency of a ball mill
احصل على السعر
Quantifying the energy efficiency of fine grinding
In this example, the OWi of the SAG mill was found to be 30% higher than the ball mill, thus suggesting that the SAG mill was less efficient than the ball mill. The apparent inefficiency of SAG mills when balls reduced the number of particles coarser than 1 mm by about 5%. In case the feed to ball mill was equal to 1200 Mg/h, it resulted in a reduction of 60 Mg/h of the weight of coarse particles in circulation. It also enabled the processing of a larger feed size without the risk of balls being thrown from the mill. No negative impact on theAnaliza efektywności mielenia w młynach kulowym i
احصل على السعر
Efficient preparation and characterization of graphene based on ball
Table 2-1 factors and levels were combined in a homogeneous design with a total of five influencing factors in the experiment: X1 — ball mill rotation rate, X2 — aluminum powder particle size, X3 — aluminum mass, X4 — steel sand mass, and X5 — steel sand particle size. According to the principle of uniform design, the number of trials In neither application was the HPGR principally chosen for its energy efficiency and almost a further 20 years had to pass before the Mining Industry saw the first full scale HPGR-Ball mill installation at Cerro Verde (Vanderbeek et al., 2006), which was chosen due to the 15% energy saving it provided compared to the SAG-Ball mill alternative.Helping to reduce mining industry carbon emissions: A step
احصل على السعر
Efficient preparation and characterization of graphene based on ball
The results indicate that using aluminum powder as a grinding aid can significantly improve the efficiency of ball milling, the specific surface area of graphene produced is 542.598 m2 /g, with the number of layers ranging from 2 to 5 layers. It is proved that the proposed graphene preparation method can obtain graphene with better quality.A ball mill is a type of grinder widely utilized in the process of mechanochemical catalytic degradation. It consists of one or more rotating cylinders partially filled with grinding balls (made(PDF) Grinding in Ball Mills: Modeling and Process Control
احصل على السعر
Energies Free Full-Text Energy-Efficient Advanced Ultrafine
The present literature review explores the energy-efficient ultrafine grinding of particles using stirred mills. The review provides an overview of the different techniques for size reduction and the impact of energy requirements on the choice of stirred mills. It also discusses the factors, including the design, operating parameters, and feed material An increasing trend of anthropogenic activities such as urbanization and industrialization has resulted in induction and accumulation of various kinds of heavy metals in the environment, which ultimately has disturbed the biogeochemical balance. Therefore, the present study was conducted to probe the efficiency of conocarpus (Conocarpus Sustainability Free Full-Text Ball Mill, Humic Acid, and Rock
احصل على السعر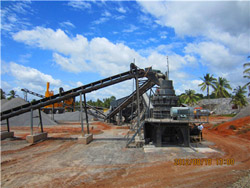
(PDF) DEM Investigation of Mill Speed and Lifter
By means of motion analysis of the charge, a good grinding efficiency can be obtained when the ball filling ranging from 20% to 40% and the mill speed ranging from 70% to 80%.Hence, ball mills such as planetary ball mills usually work in cyclic mode to avoid elevated temperatures. For instance, Schneider et al. reported that samples were partly burned when planetary ball-milled for 60 min with a cyclic mode of 5 min grinding time and 3 min pausing time. For instance, the energy efficiency obtained for ballBall milling as an important pretreatment technique in
احصل على السعر
Milling CEEC (Coalition for Eco Efficient Comminution)
Addition of pebbles to a ball-mill to improve grinding efficiency. S NKWANYANA AND B LOVEDAY (1) PRESENTED AT COMMINUTION ’16, MINERALS ENGINEERING INTERNATIONAL, PUBLISHED IN MINERALS ENGINEERING VOLUMES 103-104, BARRY WILLS (ED), APRIL 2017. ABSTRACT Ball-mills are used widely for The organocatalytic activity of (S)-proline-based dipeptides 1a–c has been evaluated in the asymmetric aldol reaction between representative ketones with various aromatic aldehydes under solvent-free conditions in a ball mill.In particular, the methyl ester of (S)-proline-(S)-tryptophan, (S,S)-1c, proved to be an efficient organocatalyst, and the Efficient ball-mill procedure in the ‘green ScienceDirect
احصل على السعر
Study on the influence of liner parameters on the power of ball mill
The research results provide theoretical support and scientific basis for the reasonable design of liner and the efficiency of ball mill. Fig10. The influence of the number of stepped liner ofIt was found that the ball mill consumed 54.67 kWh/t energy to reduce the F 80 feed size of 722.2 µm to P 80 product size of 275.4 µm while stirred mill consumed 32.45 kWh/t of energy to produce the product size of 235.6 µm. It also showed that stirred mill produced finer product than the ball mill at around 40% lesser consumption of energy.Effect of ball size and powder loading on the milling efficiency
احصل على السعر
A Comparative Study of Energy Efficiency in Tumbling Mills
An evaluation of Relo grinding media (RGM, Reuleaux tetrahedron-shaped bodies) performance versus standard grinding media (balls) was made through a series of grinding tests, including a slight modification of the standard Bond test procedure. Standard Bond tests showed a reduction in the Bond ball mill work index (wi) of the mineral sample used In this paper, a durable triboelectric nanogenerator inspired by a ball mill was designed by using metal balls in hollow drums as carriers for charge generation and transfer. Composite nanofibers were deposited onto the balls, increasing the triboelectrification with the interdigital electrodes in the inner surface of the drum for Nanomaterials Free Full-Text Ball-Mill-Inspired Durable
احصل على السعر
Comparison of energy efficiency between ball mills and stirred mills
Shi et al. (2009) carried out tests in a laboratory scale vertical mill and found the mill to be 25% to 37% more efficient than ball mills. Mazzinghy et al. (2015) performed tests with a pilotThe ball mill Ball milling is a mechanical technique widely used to grind powders into fine particles and blend materials. 18 Being an environmentally-friendly, cost-effective technique, it has found wide application in industry all over the world. Since this mini-review mainly focuses on the conditions applied for the preparation andBall milling: a green technology for the preparation and
احصل على السعر- ماكينة لف الصاج في اسرائيل
- وادكنىس تونس المعداة الثقىلة
- periwinkle shell as coarse aggregate for concrete
- سرعة عالية الصين أفضل سعر التعدين مطحنة
- نيوزيلندا الصانع آلات التعدين
- آلة كسارة عامية في مومباي مصر
- function grinding price
- سعر كسارة التنتالوم
- الكرة مطحنة السرعة المثلى نوع الملف pdf
- مصدر كسارة الكاولين في اندونيسيا
- hammer crusher for calcium carbonate india gold crusher blog
- كسارة الصخور المتنقلة بالحصى
- صناعة الطوب غانا
- كسارة الحجر الجليدي المورد في مصر
- buy gypsum powder production machinery used in construction