اتصل
هاتف
+0086-371-86162511
عنوان
تشنغتشو ، الصين
wet process plant of iron oreother mineral

Treatment of iron ore beneficiation plant process water by
In the present study, process water collected from iron ore beneficiation plant was treated by electrocoagulation (EC) to obtain treated water suitable for reuse Effective technology for a complex wasteless processing of the iron ores has been designed and includes three main components (plats): comminution plant, briquette plant, pigment plant.(PDF) Effective Processing of the Iron Ores
احصل على السعر
Process simulations in mineralogy-based geometallurgy
This study focussed on flowsheet simulation for mineralogical-based approach to geometallurgy of iron ores. Process unit models used were Making iron and steel from iron ore requires a long process of mining, crushing, separating, concentrating, mixing, agglomeration (sintering and pelletizing), Iron Ore Processing, General SpringerLink
احصل على السعر
Process simulations in mineralogy-based geometallurgy of iron ores
iron ores. Process unit models used were selected based on their applicability at particle level for iron ore beneficiation and flowsheet simulation. The feed streams for plant Last Updated: 13 Oct 2023. PDF Process water collected from the iron ore beneficiation plant was treated by electrocoagulation (EC) process to make it suitable for reuse or safe |...Treatment of iron ore beneficiation plant process water
احصل على السعر
Process flow sheet for Pelletization using wet grinding
Any type of grinding (wet/dry) may be adopted for any of the Pelletization technique. However the pellet plant in eastern region use either travelling grate technology with dry grinding or GrateIt has been found that the main iron-bearing mineral is hematite, which contains 69.02 to 70.35% of iron distributed in the ore. Magnetite and hydrogoethite account for 16.71–17.74 and 8.04–10.50% Mineral and Technological Features of
احصل على السعر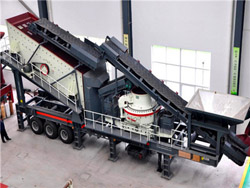
Upgradation of Iron Ore Fines and Slime by Selective Hindawi
Washing of iron ore fines and slime (10% and 25% w/v, slurry concentrations) with two types of surface-active agents (sodium humate (synthesized) and AD 200 (commercial)) at varying concentrations at pH 8 was conducted for ascertaining the efficacy of dispersants in beneficiating the low-grade iron ores. The beneficiation Iron ore handling, which may account for 20–50% of the total delivered cost of raw materials, covers the processes of transportation, storage, feeding, and washing of the ore en route to or during its various stages of treatment in the mill.. Since the physical state of iron ores in situ may range from friable, or even sandy materials, to monolithic Iron Ore Processing, General SpringerLink
احصل على السعر
Plasma Processing of Iron Ore IntechOpen
The depletion of high-grade ore minerals and the scarcity of fossil fuel reserves are challenging factors for metallurgical industries in the future. Also, extensive mining for increased steel The haematite ore in South Africa is processed in a dry process to a HQ lump ore with 64 % iron content and a sintered fine ore with 63.5 % iron content. For fine ore beneficiation, wet processes are used. Capacity at the Minas Rio is to be increased from 26.5 Mta capacity to 28 Mta in the forthcoming years.Dry beneficiation of iron ore Mineral Processing
احصل على السعر
CSIR IMMT Mineral Processing Research Areas
Development of Process Flow Sheet to Recover Titanium and Iron from NALCO Refinery Sands (NALCO, Bhubaneswa). Dewatering Studies of Steel Plant Sludges (Vizag Steel Plant, Vizag). Dry and wet Beneficiatation studies of Low Grade Iron Ores to Prepare Quality Products for Iron and steel Making (Usha Martin Limited, Jamshedpur).Fig 3 Types of processing ores. The wet processing (Fig 4) is normally practiced for low / medium grade (60 % Fe to 63 % Fe) hematite iron ore. The wet process consists of multi-stage crushing followed by different stages of washing in the form of scrubbing and / or screening, and classification etc., but the advantage is only partial Beneficiation of Iron Ores IspatGuru
احصل على السعر
(PDF) QUANTITATIVE ESTIMATION OF MINERALS IN IRON
[28] Mineral composition The minerals (hematite, goethite, gibbsite, kaolin, and quartz) are identified using powder XRD analysis. [29] Mineral phases in ores and process streams Chemical assaysThe separation technology provides for production of iron ore concentrate with total iron content of 65.9% and recovers 91.0% of magnetite and 80.5% of hematite from the tailings containing 20.4% of total iron. The proposed technology will increase production of the concentrate at a dressing plant and reduce environmental impact. 1 IntroductionRecovery of magnetite-hematite concentrate from iron ore
احصل على السعر
Iron Ore Mining Equipment Iron Ore Beneficiation CDE CDE
Iron Ore Mining Equipment Achieve a Higher Fe Content. Efficiently remove silica, alumina, clay, and other contaminants from your feed material to increase the Fe value in the final ore. Our iron ore beneficiation projects have increased the Fe content from 43% in the feed to above 60% in the final iron ore product, ensuring increasedIn designing the innovative, modular ore crushing and screening plant for SD11, Vale was faced with the challenge of coping with the region’s wet-season humidity, which potentially could reduce process efficiency. The iron ore in this area contains a large volume of fines (20–30% below 150 μm) which can be transformed into a sticky mass atComminution and classification technologies of iron ore
احصل على السعر
Iron Ore Sintering: Raw Materials and Granulation
Abstract and Figures. Sintering is an agglomeration process that fuses iron ore fines, fluxes, recycled products, slag-forming elements and coke. The purpose of sintering is to obtain a productThe iron content of iron ore can vary widely, but typically ranges from 50-70%. The extraction of iron from iron ore is a complex process that involves smelting or using heat and chemicals toWhat is the beneficiation of iron ore? LinkedIn
احصل على السعر
Mineral and Technological Features of
It has been found that the main iron-bearing mineral is hematite, which contains 69.02 to 70.35% of iron distributed in the ore. Magnetite and hydrogoethite account for 16.71–17.74 and 8.04–10.50% Production Process of Iron Ore. Generally, the processing of iron ore needs several processing stages, including crushing, grinding, ore beneficiation, concentrating, drying, etc. The equipmentsIron ore processing plant LinkedIn
احصل على السعر
Iron Ore Pelletization Technology and its Environmental Impact
Iron ore is primarily found as the oxides of iron, notably hematite and magnetite and as hydroxides like goethite and limonite. Small amounts are found as the carbonates in siderite, as sulphides3.1 Characterization Studies. Particle size distribution of the iron ore fine sample is given in Table 1.It was observed from Table 1 that 50% sample is below 1800-μm size. Chemical analysis given in Table 1 indicated that, as particle size decreases, Fe content decreases up to 54.54%. Further, the size distribution of samples revealed that Characterization and Beneficiation of Dry Iron Ore Processing Plant
احصل على السعر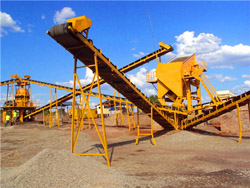
Iron ore magnetite processing alsglobal
Medium Scale Wet MIMS RMS Separators. Two units are available inclusive of the Eriez MIMS counter-rotation wet drum at 610 mm width x 400 mm diameter measuring 6,300G at 1.5 mm from the surface, and a Longi triple drum/bath unit running at gauss fields of 5,000, 6,000 and 7,000 G for each drum/bath.10.3.2 Coal gasification power plant with integrated mineral carbonation. Gasification of hydrocarbon, coal, or biomass feedstock, described in Chapter 3, is a process that can be integrated into power generation, or the production of synthetic liquid fuels or hydrogen, with high levels of energy efficiency.The synthesis gas (syngas) produced is a mixture of Mineral Carbonation an overview ScienceDirect Topics
احصل على السعر
Dewatering and Drying in Mineral Processing Industry: Potential for
Wet beneficiation of minerals necessarily requires removal of large amounts of water — typically contaminated — before further processing of the concentrated ores can be carried out.They are classified according to the percentage of metallic iron in them: Magnetite: It is the most valuable type of iron ore. It is made up of more than 70% metallic iron. It is black and has magnetic properties. Hematite: It is composed of 65-70 per cent metallic iron. It’s a combination of red and brown.Iron Ore, Types, Uses, Distribution in India & World Map
احصل على السعر- process of cyanidation gold
- تستخدم كسارة بلوك المجمدة فرنسا للبيع السعر
- محطة كسارة المحمول التجيير دبي
- معايير الحزام الناقل أستراليا
- china new top quality vibrating screen for lab
- تحميل مجانا من مطحنة الكرة الاسمنت مصنع الشعبي
- العلامة التجارية الأكثر محطم كسارة في الصين
- سعر مكينه تثبيت الكريستال بجده
- Reeds Rock Crusher Europe
- الفلبين مجردة من إعادة التدوير
- نظام الضغط العالي لمصنع الاسمنت
- pn1 زبدة الفول السوداني
- Marble Ghisai Machine Price
- مطرقة طحن من حجم بكرة الصين
- تقدم كسارة الفحم