اتصل
هاتف
+0086-371-86162511
عنوان
تشنغتشو ، الصين
model on magnetic separation of iron ore
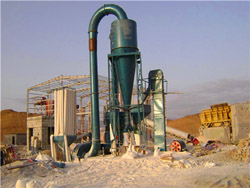
Magnetic Separation of Al-Hussainyat Iron Ore ResearchGate
As a practical application on this model, a magnetic separation process was conducted on samples of Al-Hussainyat iron ore in order to to examine the validity Abstract: Conventional magnetic separation devices are widely used for the removal of tramp iron from a variety of feed materials and for the beneficiation of ferrous ores. Magnetic separation: A review of principles, devices, and
احصل على السعر
Developments in the physical separation of iron ore: magnetic
This chapter introduces the principle of how low-grade iron ores are upgraded to high-quality iron ore concentrates by magnetic separation. Magnetite is This paper describes a study around the recovery of fine magnetite in the form of a pelletizing concentrate. The study is based on an evaluation of an iron ore by-product opportunity from an iron oxide copper-gold (IOCG) Maximizing the recovery of fine iron ore using magnetic
احصل على السعر
Physical separation of iron ore: magnetic separation
ABSTRACT: This study consists of the evaluation of the magnetic superficial roasting process of a hematitic iron ore, aiming the best performance in Huang Wan-fu had also achieved the grade of iron concentrate 53.39% by an integrated technique of both wet high-intensity magnetic separation and vibration Enrichment of Fe by Reduction Roasting-Magnetic Separation
احصل على السعر
Physical separation of iron ore: magnetic separation ScienceDirect
This chapter introduces the principle of how low-grade iron ores are upgraded to high quality iron ore concentrates by magnetic separation. Magnetite is The research is aimed at solving the topical problem of enhancing efficiency of iron ore magnetic separation by applying ultrasonic technologies to identify optimal Increasing efficiency of iron ore magnetic separation by using
احصل على السعر
Increasing efficiency of iron ore magnetic separation by using
*Corresponding author: morkunv@gmail Increasing efficiency of iron ore magnetic separation by using ultrasonic technologies Vladimir Morkun1,*, Natalia Morkun1, Vitalii Tron1, Vladimir Golik 2, and Arkadii Davidkovich3 1Kryvyi Rih National University, Automation, Computer Science and Technology Department, 11 Vitalii Matusevich Str., 3. Feeding the crusher (Reclaim) The surge pile allows a constant supply of material to be fed into the mill, which ensures consistent results and stability in the ore recovery process. 4. Grinding. The primary grinding mill grinds the The six main steps of iron ore processing Multotec
احصل على السعر
Magnetic Separation SpringerLink
In the case of fine, feebly magnetic minerals, the best choice for magnetic separation is high-gradient magnetic separators . Dry low-intensity magnetic separators (DLIMS) are generally employed to: upgrade iron ores containing relatively large particles and strongly magnetic minerals. separate iron pieces from steel mill slags and blast The optimum grade that could be obtained from single-stage dry magnetic separation was 35.52% Mn, and with a Mn:Fe ratio of 1.77, and 44% Mn recovery in the case of sample 1; whereas, a 33.75% Mn grade, with a Mn:Fe ratio of 1.66 at Mn recovery of 44% was reported for Sample 2. It was observed that both samples had a similar input chemistryDRY MAGNETIC SEPARATION OF MAGNETITE ORES ScienceGate
احصل على السعر
Influence of process parameters of dry high intensity magnetic
However, the low-grade iron ores are attendant with unwanted gangue minerals such as silica, alumina, clays, apatite, and calcite. Standard physicochemical methods such as froth flotation and gravity separation (spiral concentrator, jigging, heavy media separation) were used to separate the gangue minerals from hematite are Four different iron minerals were selected for study, and five size fractions of each mineral were prepared. The magnetic properties of these minerals were measured. The effect of particle sizeWet High Intensity Magnetic Separation of Iron Minerals
احصل على السعر
Separation and Recovery of Iron from Low-Grade Refractory Iron Ore
The low-grade iron ore fines contain weakly magnetic iron minerals such as hematite and siderite, which could not be separated effectively by low-intensity magnetic separation. Therefore, the ore fines were magnetized by magnetization roasting, then low-intensity magnetic separation was used to enrich magnetic iron minerals.Magnetic separation is the process of separating components of mixtures by using a magnet to attract magnetic substances. The process that is used for magnetic separation separates non-magnetic substances from those which are magnetic. This technique is useful for the select few minerals which are ferromagnetic (iron-, nickel-, and cobalt Magnetic separation
احصل على السعر
Magnetic Separation and Iron Ore Beneficiation IspatGuru
Magnetic separation is an old technique for the concentration of iron ores and for the removal of tramp iron. Since 1849, a number of patents on magnetic separation have been issued in USA, and texts of some of the patents before 1910 describe a variety of magnetic separators for mineral processing.Dry medium-intensity magnetic separator (DMIMS) plays a vital role in enhancing the separation of low-grade raw magnetite ore. A good understanding of the dynamic separation process of DMIMS would further boost its economic competitiveness in minerals processing and engineering. Herein, this study analyzed the basic structure and Dynamic behavior and separation prediction of magnetic ore
احصل على السعر
Physical separation of iron ore: magnetic separation
Magnetic separation technology plays an important role in upgrading such low-grade iron ores, because the magnetic separation process possesses the combined advantages of large capacity and low operating cost, as well as being environmentally friendly. This chapter first introduces the principles and recent advances in magnetic This research is aimed at the up-gradation of indigenous Pakistani iron ore, i.e., Dilband iron ore (hematite), by utilizing common metallurgical processes. First, the magnetic properties of the ore were Beneficiation of Low-Grade Dilband Iron Ore by
احصل على السعر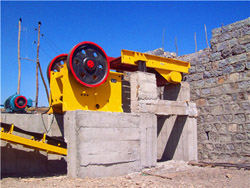
Magnetic Separation of Impurities from
The removal of iron ion from leaching solution is critical for the recovery of value metals, with the method of choice commonly being crystallization (precipitation). This paper summarized the new Dry permanent magnetic separators have been widely used in the mineral and coal processing industries due to their simple operation and high separation efficiency. These tools not only discard some amount of bulk gangue from the raw ore, thereby reducing the volume of the grinding operation and cutting energy consumption, but also Minerals Free Full-Text Dry Permanent Magnetic Separator:
احصل على السعر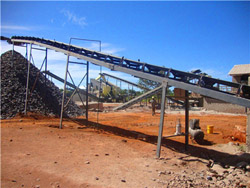
Separating efficiency of ferromagnetic particles and principle of
Introducing airflow into the low-intensity dry magnetic separator (LIDMS) is an effective means to improve the separating efficiency of ferromagnetic particles under dry conditions. In this study, a multi-physical coupling model was established to compare the separating performance of LIDMS under four typical air supply modes.During the SMR process, weakly magnetic hematite and siderite in the iron ore tailings were converted to strongly magnetic magnetite with an average magnetic conversion rate of 81.71%.(PDF) Magnetic separation of roasted hematitic ore ResearchGate
احصل على السعر
Beneficiation of Magnetically Separated Iron-Containing Ore Waste
separators, modernized to work with waste from the dry processing of such ores. Cas-caded drum magnetic separators are proposed, which allow to achieve comparable results with [16,17] on the beneficiation of iron-containing ore magnetic separation waste. 2. Materials and Methodsmagnetic separation. Dry Magnetic Separation of Iron Ore: There are many inherent advantages in processes that utilize dry magnetic separation to beneficiate iron ore. Wet concentration of magnetite ore, in comparison, re- quires 500 to 1000 gal of water per ton of concen- trate produced. This means extensive use of waterADVANCES IN MAGNETIC SEPARATION OF ORES 911
احصل على السعر
Semi-Smelting Reduction and Magnetic Separation for the
This work presents a semi-smelting reduction and magnetic separation process for the recovery of iron and alumina slag from iron rich bauxite ore. The effect of the process parameters on the recovery rate of iron, maximum particle size of the iron nugget, and the Al2O3 content of the alumina slag was investigated and optimized. The Moreover, compared with the wet magnetic separation, dry magnetic separation offers an opportunity to exploit low-grade iron ores in remote and arid regions that would otherwise be not consideredIron ore after magnetic separation: (a) tailings; (b) iron-ore
احصل على السعر- carbon in leach process for gold recovery
- كسارة مطرقة للعبوات الزجاجية والحجار
- مكونات طحن الأسمنت
- آلة طحن من قائمة الأسعار
- electronic speed controller for crusher feeder
- تستخدم 500 الهيدروكربونات النفطية محطة كسارة طاحونة
- العملية في استخراج الحديد من خام رماد
- عملية مطاحن كسارة
- Shingle Grinders Horizontal
- معدات الآلات ألمانيا
- کیلو وات موتور به تعدادی از برق در هر ساعت
- حلقة النحاس سيمونز alog
- Janet Napoles Coal Mine In Indonesia
- كينيا مصنع النحاس
- زباله در خرد کردن سنگ معدن