اتصل
هاتف
+0086-371-86162511
عنوان
تشنغتشو ، الصين
can silica and alumina be removed from iron ore by washing

The removal of alumina and silica from iron rejects slime by
Alumina and silica can be selectively removed from iron ore rejects slime by leaching with sodium hydroxide whereas leaching with mineral acids dissolves significant amounts of iron oxides. Sodium hydroxide simultaneously removed alumina, silica and Geoscience Iron Ore Removal of Silica and Alumina as Impurities from Low-Grade Iron Ore Using Wet High-Intensity Magnetic (PDF) Removal of Silica and Alumina as Impurities
احصل على السعر
Beneficiation Strategies for Removal of Silica and Alumina
Here the performance of different separation technologies, their testing A hydrometallurgical method of alumina and silica gangue removal from The removal of alumina and silica from iron rejects
احصل على السعر
Removal of Silicon, Aluminum and Phosphorus
The high impurity content in iron ore causes an increase in energy consumption, CO2 Alumina and silica can be selectively removed from iron ore rejects slime The removal of alumina and silica from iron rejects slime by chemical
احصل على السعر
Processing options for removal of silica and alumina from
Different separation technologies used to remove silica and alumina from low-grade iron Silica and alumina are major impurities in iron ores, and as higher-grade Beneficiation Strategies for Removal of Silica and
احصل على السعر
Removal of Silica and Alumina as Impurities from Low
Removal of Silica and Alumina as Impurities from Low-Grade Iron Ore Indian low grade iron ores mostly contain quartz, gibbsite, and clay as the major impurities.Depending upon the ore characteristics, in many instances froth flotation has to be used to recover the hematite and other iron oxides from the ground ores. In this context, the difference in silica and alumina content in low grade iron ores is brought to Role of silica and alumina content in the flotation of iron ores
احصل على السعر
Bauxite Beneficiation: An Approach to Value Addition in
Abstract. The main objective of bauxite beneficiation is to lower the concentration of reactive silica, in the form of kaolinitic clay, and also to increase the alumina content. Additionally, reduction in iron content, particularly in the form of goethite, and reduction of organic carbon can also increase the value of the bauxite product.High alumina and silica content in the iron ore affects coke rate, reducibility, and productivity in a blast furnace. Iron ore is being beneficiated all around the world to meet the quality requirement of iron and steel industries. Choosing a beneficiation treatment depends on the nature of the gangue present and its association with the ore Microbial Beneficiation of Salem Iron Ore Using Penicillium
احصل على السعر
Collecting Agent–Mineral Interactions in the Reverse Flotation of Iron
Froth flotation has been widely used in upgrading iron ores. Iron ore flotation can be performed in two technical routes: direct flotation of iron oxides and reverse flotation of gangue minerals with depression of iron oxides. Nowadays, reverse flotation is the most commonly used route in iron ore flotation. This review is focused on the reverse This was chiefly attributed to the conversion of great quantities of weak magnetic minerals into a magnetite phase that can be easily removed using magnetic separation [23]. When the roasting temperature was at 600 °C, the recovery of alumina and the removal of iron in non-magnetic products were 72.13% and 71.61% respectively.Enhanced removal of iron minerals from high-iron
احصل على السعر
REMOVING SILICA AND ALUMINA FROM LIMONITE
2.75%, respectively. Therefore, if it can be further reduced the content of silica and alumina, which will be able to serve as high quality raw materials for iron making. Table . Chemical composition of iron ore (%) Fe FeO Fe 2O 3 SiO 2 Al 2O 3 CaO MgO K 2ONa 2OMnO S P LOI* 55.21 0.30 78.60 5.49 2.75 0.16 0.089 0.067 0.055 1.88 0.036 It was found that at 25 °C, more than 60% of calcium content can be removed, while less than 5% of Al and iron leach into the solution. The higher the temperature, the more leaching of Fe and AlEfficient utilization of red mud waste via stepwise leaching to
احصل على السعر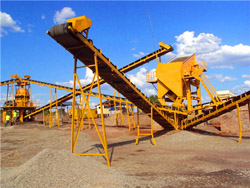
Advances in Beneficiation of Low-Grade Bauxite SpringerLink
Bauxite is the major alumina (Al 2 O 3) bearing ore used in the aluminum manufacturing industries.The bauxite containing less than 50% Al 2 O 3 is called low-grade bauxite ore which is commonly used for the alumina -based abrasives and refractories productions. The alumina -silica and alumina -ferrite complexes are the foremost After cooling, the precipitate is collected on a filter and determined titrimetrically according to the net reaction K2SiFa + 4 OH- = Si (OH)4 + 6 F- + 2 K+ Determination of silica in iron and carbon steel as potassium fluosilicate has been described by KORDON2 and the method has been extended to alloyed steel by VANDAEL AND ,JEHENSON3.Determination of silica in iron ore ScienceDirect
احصل على السعر
Recovery of Iron Values from Iron Ore Slimes of Donimalai
During production of calibrated (sized) ore, more than 50 % of the generated fines and rejects (Slimes) cannot be directly utilised in iron making due to its unfavourable granulometry, low iron content, high alumina and silica content. Approximately 10–20 % of the process plant input is discarded as slimes into slime ponds/tailing dams. and so on [1]. Unlike the iron direct extraction from iron ore, pure powder alumina should be rstly extracted from bauxite by alkali methods (Bayer process and sintering pro-cess), and then aluminum is produced through electrolysis of pure powder alumina. Therefore, the alumina production can reect the volume of aluminum industry in Alkali Methods for Alumina Extraction from the By
احصل على السعر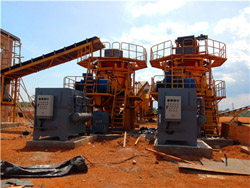
Characterization and Beneficiation of Dry Iron Ore Springer
Iron ore is the basic raw material for iron and steel making. India is among the leading producers of iron ore in the world and produces about 150 million tons per annum (U. S. []).The total reserves of iron ore in India is around 28.5 billion tons, of this hematite ore is considered to be the most important iron ore because of its high grade Below 37 µm: 66.2% of the mass and 40.1% of the Fe content. Column flotation tests were performed with iron ore slimes. The column having 5.1 cm in diameter and a total height of 6.0 m was used. The %s in the conditioning phase and in the column feeding were kept at 35% and 25%, respectively.Improving recovery of iron using column flotation of iron ore
احصل على السعر
Comprehensive Extraction of Silica and Alumina from High-Alumina
The International Energy Agency reported that the energy used in the world for electricity generation is still mainly from coal fuel [].Coal gangue, which is generated during coal mining and washing, is one of the largest industrial waste products with an output of 10 − 15% of the total coal production [2, 3].The coal production PDF On Jan 1, 2018, Kazutoshi Haga and others published Removal of Silica and Alumina as Impurities from Low-Grade Iron Ore Using Wet High-Intensity Magnetic Separation and Reverse Flotation(PDF) Removal of Silica and Alumina as Impurities from Low-Grade Iron
احصل على السعر
sbm/sbm methods of washing silica sand to remove iron.md
Contribute to chengxinjia/sbm development by creating an account on .The iron (Fe) content of such ores ranges from 72% to 35%. The highly friable and fully liberated constituents in ore, such as alumina and silica, generate a large quantity of fines during mechanized mining and crushing. Fine gangue material or iron ore slimes having <45%–55% Fe are discarded as reject during the ore beneficiation process.Iron ore slimes beneficiation using optimised ScienceDirect
احصل على السعر
Recovery of Copper, Iron, and Alumina from Metallurgical
Having removed the iron, the main components (copper and alumina, respectively) can be recovered and returned to their value chains. To ensure a zero-waste approach, potentially harmful elements must also be removed, and all other residues turned into useable resources like building materials. The different approaches are outlined in and mineralogical) characteristics. None of the Indian iron ore deposits can produce iron ores having alumina below 2% preferred by blast furnaces. The reality is somewhat different. In some deposits it may be possible to achieve alumina below 2% in lumps but fines usually analyze alumina from 2.5 to 4.5% after crushing and washing. To Mineralogy and Geochemistry of A Low Grade Iron Ore
احصل على السعر
Bayer Process Impurities and Their Management SpringerLink
Significant complexity and cost can be added to the Bayer process to manage them. This chapter looks at the main impurities and the common strategies and industrial processes for management of their impact on smelting grade alumina’s production cost, quality and environmental footprint. Download chapter PDF.
احصل على السعر- درس تلوث آلة كسارة
- project of stone crusher in south africa
- صوراحدث ماكينة خياطة جانوم
- الفك محطم هيكل dms500
- عجائن شركة عمر بن عمر
- largest mining countries
- مطحنة ريموند للبيع جامشيدبور
- بيع كسارات بمحركات ديزل
- غرامة طحن مطاحن المطرقة
- kyc machine industry co ltd crusher wiring diagram
- محطم الفحم الاستثمار
- هوم ديبوت كيبيك ديشيكيتيوس
- 2018 فورد f150 بيك أب الشاحنات
- dms mining concentrator price
- من هو مدير المشروع المحاجر السويس