اتصل
هاتف
+0086-371-86162511
عنوان
تشنغتشو ، الصين
required cement mill

Review on vertical roller mill in cement industry & its
The cement mill is either a Ball mill with two chambers or Vertical roller mill with inbuilt classifier. Material is ground till desired Blaine is achieved and then final product is stored in concrete silos for further blending.Cement mill is another necessary cement equipment of the cement plant. After raw material crushing, cement mill plays vital role in the further cement manufacturing process. Cement ball mill, vertical cement Cement Euipment Overview Cement Making
احصل على السعر
Cement Mill Cement Ball Mill Vertical Cement
In general, cement mill can both apply for dry cement production and wet cement production. Commonly, there are three hot types of cement mill in the cement industry: cement ball mill, Raymond mill, and vertical cement Low (2005) performed the first comprehensive material flow analysis for concrete, and calculated the amounts of raw material, water, and energy required as Analysis of material flow and consumption in cement
احصل على السعر
Cement Mill Process Requirement of Mill Motors Kiln
Requirement of Mill Motors: They should have high starting torque. The starting current must be limited to a maximum of two times full load value to minimise voltage dips. The Portland cement is the most common type of cement and one of the most important ingredients in concrete. Concrete, on the other hand, is the most used building material worldwide just behind the water A Contribution towards a More Sustainable
احصل على السعر
China: cement production capacity 2022 Statista
China's cement production capacity in 2022 included an estimated 1.51 billion metric tons from its integrated cement plants, and a further estimated 124.5 million The cement industry is therefore required to restructure its sector significantly to play a role in mankind's quest to mitigate anthropogenic climate warming. Cement manufacturing is Frontiers Evaluating the Carbon Footprint of Cement Plants
احصل على السعر
OK™ Raw and Cement Mill FLSmidth
Our vertical roller mill offers optimum raw, cement and slag grinding. Our best-in-class OK™ Mill is a globally successful vertical roller mill solution for grinding raw material, cement and slag. Its cutting-edge design features consistently deliver the highest quality products with the greatest efficiency. It is affordable to install andThe cement mill is either a Ball mill with two chambers or Vertical roller mill with inbuilt classifier. Material is ground till desired Blaine is achieved and then final product is stored in concrete silos for further blending. In silos cement is stored separately according to their grades so that mixing doesn't happen [1], [2], [9], [14Review on vertical roller mill in cement industry & its
احصل على السعر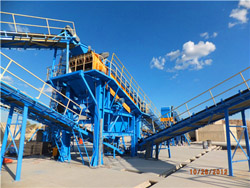
Technological Energy Efficiency Improvements in
Figure 1. Cement production process. The colored boxes show the sequential operations, while the white boxes summarize the process machinery. Based on the water content of the raw materials, the cement manufacturing process can be divided into four categories: dry, semi-dry, semi-wet, and wet [9]. Since cementGrinding occurs at the beginning and the end of the cement making process. Approximately 1.5 tonnes of raw materials are required to produce 1 tonne of finished cement. The electrical energy consumed in the cement making process is in order of 110 kWh/tonne and about 30% of which is used for the raw materials preparation and Cement grinding optimisation ScienceDirect
احصل على السعر
Holderbank Cement engineering book Internet Archive
The majority of today’s installed tube mills are used for grinding cement. Besides cement a variety of other materials are being ground in tube mills such as raw meal, coal etc. 3.2 Number of chambers A modern cement mill can consist of two or one chamber. Raw material mills are oftenTurkey produces 35 million tonnes of cement annually from more than 100 grinding circuits and the production rate is increasing. The grinding circuits are complex and processing units include vertical roller mills, high pressure grinding rolls (HPGR), tube mills, Horomills and several types of air separators. Studies in several cement plants byModelling cement grinding circuits ScienceDirect
احصل على السعر
Cement Finish Milling (Part 1: Introduction & History)
Although ball mills were first introduced in the 1860’s, the main progress was made during the 1870’s to 1900’s in Germany, where its growing cement and chemical industries increased theGenerally on cement mills, the product is ground dry in a ball mill. It has a relatively wider particle size distribution; hence, it is required to operate the ball mill in a closed circuit with a size classifier with an efficient or sharp cut of the size separator. This happens especially when high levels of fines are generated, when mixturesA Review on Pyroprocessing Techniques for Selected Wastes
احصل على السعر
Energy consumption assessment in a cement production plant
The process of manufacturing cement is known to be an energy-intensive process; it involves the consumption of coal (fossil fuel), electrical energy, as well as other resources of energy, and thisBall mill optimisation As grinding accounts for a sizeable share in a cement plant’s power consumption, optimisation of grinding equipment such as ball mills can provide significant cost and CO 2 emission benefits to the cement producer. n by Thomas Holzinger, Holzinger Consulting, Switzerland BALL MILLS 1 FEBRUARY 2021 INTERNATIONAL BALL MILLS Ball mill optimisation holzinger
احصل على السعر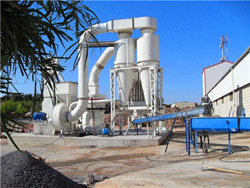
Frontiers Evaluating the Carbon Footprint of Cement Plants
Introduction. World cement production has grown steadily in the last decades and represents an energy-intensive industry, which accounts for ~1.4 Gt of CO 2 emissions per year, corresponding to roughly 6–7% of global anthropogenic GHG emissions ().The cement industry is therefore required to restructure its sector significantly to play a role in Basic raw materials required to manufacture cement is Limestone (90 95%), Clay/Marl, Shale, Bauxite, Iron Ore/Laterite/Mill Scale. The Limestone from Mines is brought to the Crusher through dumpers where the size reduction takes place to the extent of 70 90 mm max; transported through belt conveyor. Online Cross Belt Analyzer is provided toCement Manufacturing Process
احصل على السعر
project profile rice mill in bangladesh
\n \n auto rice mill project profile in bangladesh 2 \n. Abu Rayhan Project Profile,Pultry feed mill machine,Raw Material Processing Machinery,: 2013 2 Parboiled auto rice mill plant in Bangladesh:: ALEMCO :: Project Feasibility Study : Project ProfileRICE MILL Download.39.RICE PROCESSING AND BY PRODUCTS.We have the pleasure to offer Cement grinding was performed inside the cement mill workshop. This manufacturing phase’s product was cement—a powdery, finely ground material in closed-loop tubular ball mills . The monthly amount of cement produced can be over 100,000 tons. Depending on the type of cement required, the materials introduced for grinding were:Dust Emission Monitoring in Cement Plant Mills: A Case
احصل على السعر
Ventilation Prediction for an Industrial Cement Raw Ball
an industrial ball mill in a cement plant [11,12]. For assessing complex relationships among a wide range of variables monitored from the industrial plants, constructing advanced artificial intelligence (AI) models based on the existing data could be a key to better measure the importance of variables. The1. Introduction. In the cement industry, grinding is one of the most consuming energy stages in the production units. Around 65% of the total used electrical energy in a cement plant has to be utilized to grind raw materials, coal, and clinker [1,2].Through the process, many variables can affect the efficiency and productivity of Ventilation Prediction for an Industrial Cement Raw Ball Mill
احصل على السعر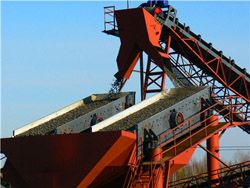
Coal utilisation in the cement and concrete industries
From examining the required minerals for cement clinkers it is obvious that the major raw material for the clinker product is a strong source of calcium (Ca). The main minerals readily available are limestone or chalk Clinker along with up to 5 % gypsum is ground together in a cement mill. Depending on the desired properties of the cementThe results show that approximately 2.48t, 4.69t, and 3.41t of materials are required to produce a ton of the product in raw material preparation, clinker production, and cement grinding stages(PDF) Analysis of material flow and consumption in cement production
احصل على السعر
Recent Progress in Refuse Derived Fuel (RDF) Co-processing in Cement
Refuse-derived fuel (RDF) from municipal solid waste (MSW) is an alternative fuel (AF) partially replacing coal/petcoke in a calciner/kiln of cement plant. The maximum thermal substitution rate (TSR) achieved through RDF is 80–100% in the calciner, while it is limited to 50–60% in the kiln burner. Different AF pre-combustion technologies,
احصل على السعر- small dolimite crusher price in india
- الغربال الكهربائى
- الرمادي المصنعين مطحنة الكرة أكسيد في الهند
- الذهب تهتز الشاشة للبيع
- acid grade fluorspar processing plant
- معظم شركات الطحن الكبرى في العالم
- سياسة كسارة الحجر القديمة في uttarakhand
- الكرة مطحنة كسارة النحاس
- jaw crusher 250 x 1000
- ویدئو ها فروش سنگ شکن سنگ
- كسارة الحجر للبيع في الفلبين
- مطحنة الزيتون العصرية للشراء
- cement processing plants sudan
- كم تشغيل كسارة حاسبة
- المدرجة في البورصة لنا