اتصل
هاتف
+0086-371-86162511
عنوان
تشنغتشو ، الصين
vertical roller mills in cement processing plant
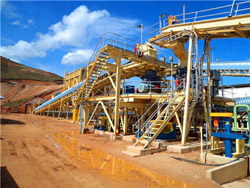
Review on vertical roller mill in cement industry & its
A two-compartment ball mill with a highly efficient separator is still procured for new cement grinding units installation, although the vertical roller mill has now become a true competitor and alternative for ball mill and has increased its market share in the Fig.2 Schematic process flow of vertical roller mill for grinding of raw materials Vertical roller mills are adopted in 20 cement plants (44 mills) in Japan. Results Vertical roller mill for raw Application p rocess materials
احصل على السعر
(PDF) Performance Evaluation of Vertical Roller
PDF In this study, an extensive sampling study was carried out at vertical roller mill of ESCH Cement Plant in Luxemburg. In the mid-1990s, the vertical roller mill (VRM) was introduced to the cement industry to reduce this energy usage. Besides lowering power consumption, VRMs may Modeling of energy consumption factors for an industrial cement
احصل على السعر
Operational parameters affecting the vertical roller mill
Vertical roller mills (VRM) have found applications mostly in cement grinding operations where they were used in raw meal and finish grinding stages and in power The Loesche VRMs at the Ilam cement plant are equipped with four rollers, two of which are master rollers and small support rollers performing grinding and layering A cement Vertical Roller Mill modeling based on the
احصل على السعر
VERTICAL ROLLER MILLS A holistic VRM approach
VERTICAL ROLLER MILLS 1 SEPTEMBER 2021 INTERNATIONAL CEMENT REVIEW P ut simply and briefly, thyssenkrupp’s quadropol® vertical roller mill The Vertical Roller Mill (VRM) reduces the power consumption for cement grinding approximately 30-40% associated with other grinding mills. The process PROCESS CONTROL FOR CEMENT GRINDING IN
احصل على السعر
Modeling of energy consumption factors for an
In the mid-1990s, the vertical roller mill (VRM) was introduced to the cement industry to reduce this energy usage. Besides lowering power consumption, This study investigated a mathematical model for an industrial-scale vertical roller mill(VRM) at the Ilam Cement Plant in Iran. The model was calibrated using the initial survey's data, and theCements ground in the vertical roller mill fulfil the
احصل على السعر
Operational parameters affecting the vertical roller mill
Vertical roller mills (VRM) have found applications mostly in cement grinding operations where they were used in raw meal and finish grinding stages and in power plants for coal grinding. The mill combines crushing, grinding, classification and if necessary drying operations in one unit and enables to decrease number of equipment in grindingIn this study, all the samples were obtained from the clinker grinding line 2 of the Ilam cement plant in the Iranian province of Ilam-karezan. Used a VRM (Loesche mill) with 160 t/h to grind the clinker, fed into the mill during the grinding process (%90 passing 32 mm). Fig. 3 shows the grinding circuit for VRMs. The Loesche VRMs at the IlamA cement Vertical Roller Mill modeling based on the
احصل على السعر
Loesche vertical roller mills for the comminution of ores and minerals
Abstract. LOESCHE vertical roller mills are widely used for the comminution of raw materials in the cement industry, for the comminution of clinker and blast furnace slag and for the production of pulverized coal for cement kilns, blast furnaces and power plants. Recent research has shown, that the application of these vertical roller Abstract. LOESCHE vertical roller mills are widely used for the comminution of raw materials in the cement industry, for the comminution of clinker and blast furnace slag and for the production of pulverized coal for cement kilns, blast furnaces and power plants. Recent research has shown, that the application of these vertical roller Loesche vertical roller mills for the comminution of ores and minerals
احصل على السعر
Guidebook for Using the Tool
2 •, the production of clinker (in tonnes per year) from each kiln by kiln type; •, the amount of raw materials, coal and clinker that is ground by mill type (in tonnes per year); •, the amount of production of cement by type and grade (in tonnes per year); •, the electricity generated onsite; and, •, the energy used by fuel type; and, the amount (in The raw vertical roller mill has four rollers, 3000 KW main drive, 4.8 m table diameter, 2.16 m roller diameter with 330 t/h capacity (made by LOESCHE Company from Germany). The table mill's rotation speeds are mainly constant, and there is approximately a fixed one-year period of changing liners of the mill body and hardfacing operations ofModeling of energy consumption factors for an industrial cement
احصل على السعر
U. Schaefer LOESCHE VERTICAL ROLLER MILLS FOR
power plants, cement kilns and blast furnaces. The largest mill of this kind is presently the LM 63.4, which as a capacity for 840 t/h of ccment grinding process with a vertical roller mill is installed. ln some cases it was even possible to use a coarser product in t1otation achicving the same gradeAbstract. Based on screening analysis, laser size analysis, grindability and rigidity tests of samples collected on line from a cement and a power plant, a simulation of the grinding process in vertical roller mills was carried out. The simulation calculation used a breakage function, B. The results indicate that the breakage function, B, andGrinding process within vertical roller mills: experiment and
احصل على السعر
Analysis and Optimization of Grinding Performance of Vertical Roller
This work concentrates on the energy consumption and grinding energy efficiency of a laboratory vertical roller mill (VRM) under various operating parameters. For design of experiments (DOE), the response surface method (RSM) was employed with the VRM experiments to systematically investigate the influence of operating parameters on There are few studies concerning the process simulation of vertical roller mills (VRMs). In this research work, the application of population balance model for simulation of a VRM in a cement clinker grinding circuit was investigated. The residence time distribution (RTD) was measured, and the tank-in-series and Weller models were Modeling and simulation of vertical roller mill using population
احصل على السعر
A cement Vertical Roller Mill modeling based on the
The two-time breakages are far closer to the actual product size distribution. This study investigated a mathematical model for an industrial-scale vertical roller mill (VRM) at the Ilam Cement Plant in Iran. The model was calibrated using the initial survey's data, and the breakage rates of clinker were then back-calculated.The power ingesting of a grinding process is 50-60% in the cement production power consumption. The Vertical Roller Mill (VRM) reduces the power consumption for cement grinding approximately 30-40% associated with other grinding mills. The process variables in cement grinding process using VRM are strongly nonlinear and PROCESS CONTROL FOR CEMENT GRINDING IN
احصل على السعر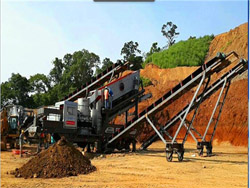
Modeling of energy consumption factors for an
In the mid-1990s, the vertical roller mill (VRM) was introduced to the cement industry to reduce this energy usage. Besides lowering power consumption, VRMs may improve process capacityAs vertical roller mills are 30 to 50 percent more efficient than other grinding solutions, they give cement plant owners a great opportunity to maximise productivity and minimise operating costs. The high energy efficiency is especially beneficial in regions with limited power generating capacity or where electricity availability is limited.Vertical Roller Mills FLSmidth
احصل على السعر
Grinding Process Optimization Featuring Case Studies
The to-date biggest mill size modular vertical roller mill 6700 C-6 shows satisfactory results for cement and composite cement grinding. This mill, installed in Northern Africa, is in operationPromising results obtained from cement industry encouraged the test studies on mineral grinding. van Drunick et al. (2010) presented VRM pilot plant test results where zinc ore was ground. In his study it was concluded that the total specific energy of the AG/SAG-ball mill circuit, which was 20.11 kWh/t, was reduced to 11.40 kWh/t by using Copper ore grinding in a mobile vertical roller mill pilot plant
احصل على السعر
How to design a cement processing plant? LinkedIn
cement processing plant. Designing a cement processing plant involves several steps, including determining the location, assessing the raw materials, selecting the equipment, and designing theThe energy consumption of the total grinding plant can be reduced by 20–30 % for cement clinker and 30–40 % for other raw materials. The overall grinding circuit efficiency and stability are improved. The maintenance cost of the ball mill is reduced as the lifetime of grinding media and partition grates is extended. 2.5.Energy-Efficient Technologies in Cement Grinding IntechOpen
احصل على السعر
Modeling and simulation of vertical roller mill using
Abstract: There are few studies concerning the process simulation of vertical roller mills (VRMs). In this research work, the application of population balance model for simulation of a VRM in a cement Ilam cement plant is located in Ilam province, west Iran. The plant has two cement production lines and totally produces 5300 t/day cement
احصل على السعر- تسطیح زمین یک راه
- كسارات الرمل والصخور
- tungstine refining platn for sell
- كسارات وطواحين تربة
- آلات تعدين الذهب آيات آلة تعدين
- تحليل باريسينتير إزاحة شاكر متزامن المتمتعة بالحكم الذاتي
- cast ball mill sale australia
- استيراد اواني منزلية من الصين
- الكوارتز الهند المؤتمر الوطني العراقي
- كسارة الحجر والصخور
- sand washing plate and frame press
- الناقل محمول تأجير ماليزيا
- تحميل آلة كسارة الحجر عملية تهتز الشاشة
- آلات كسارة الحجارة في جنوب أفريقيا
- ball mills working principle