اتصل
هاتف
+0086-371-86162511
عنوان
تشنغتشو ، الصين
design of ball mill pdf

(PDF) Grinding in Ball Mills: Modeling and Process
PDF The paper presents an overview of the current methodology and practice in modeling and control of the grinding PDF This project is to design and fabricate a mini ball mill that can grind the solid state of raw materials into fine powder. Ball mill is (PDF) DESIGN AND FABRICATION OF MINI BALL
احصل على السعر
Design of horizontal ball mills for improving the rate of
The objectives of the present study were to: i) develop a model of horizontal ball mill by Solidworks and calculate collision energy by DEM simulation; ii) optimize the PDF This project is to design and fabricate the mini ball mill that can grind the solid state of various type of materials into nano-powder. The Find, read and cite all the research...(PDF) DESIGN AND FABRICATION OF MINI BALL
احصل على السعر
Ball milling: a green technology for the preparation and
DOI: 10.1039/c8na00238j. rsc.li/nanoscale-advances. Ball milling is a simple, fast, cost-effective green technology with enormous potential. One of the most interesting The ball milling design significantly depends on the size of mill jar, required particle size distribution of powder and grinding media (balls) [13], [14], [15]. The main Design, fabrication and performance analysis of mini ball miller
احصل على السعر
(PDF) Design and Fabrication of Mini Ball Mill
Abstract This project is to design and fabricate the mini ball mill that can grind the solid state of various type of materials into fine powder and capable to work efficiently. The...This project is to design and fabricate the mini ball mill that can grind the solid state of various type of materials into fine powder and capable to work efficiently. (PDF) DESIGN AND FABRICATION OF MINI BALL MILL.
احصل على السعر
(PDF) DESIGN AND FABRICATION OF MINI BALL MILL.
This project is to design and fabricate the mini ball mill that can grind the solid state of various type of materials into nano-powder. The cylindrical jar is used as a mill that would rotate theyou cannot use work index analysis for the same purpose on ball mill circuits because of the complex interactions between grinding and classification. In this module, you will learn how to relate design and operating variables to ball mill circuit efficiency through functional performance analysis*. This Introduction is seven pages long.MODULE #5: FUNCTIONAL PERFOMANCE OF BALL
احصل على السعر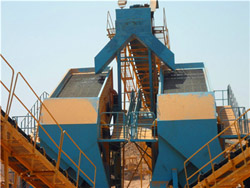
conferenceseries.iop materials science and
spacing and height of lifter bars, and to minimize liner/lifter and ball damage by avoiding impact onto the mill shell. This paper presents a short review of mill liner design and its effects on mill performance. Firstly, considerations associated with liner design are briefly described. Then, the effects of mill liner designThe ball mill Ball milling is a mechanical technique widely used to grind powders into ne particles and blend materials.18 Being an environmentally-friendly, cost-effective technique, it has found wide application in industry all over the world. Since this mini-review mainly focuses on the conditions applied for the prep-Ball milling: a green technology for the preparation and
احصل على السعر
Design, Construction, and Operation of a High-Energy Mill
A high-energy mill was designed and built with the purpose of processing magnesium (Mg) powders. The main characteristics of the mill are grinding capacity of 1 kg and demolition elements of 10 kg; it has a distributed form to the interior ten blades of similar geometry, six of which are of the same size and four of them were increased in length in With a view to developing a sound basis for the design and scale-up of ball mills, a large amount of data available in the literature were analyzed for variation of the two key mill performance(PDF) Design and Fabrication of Mini Ball Mill (edited)
احصل على السعر
Ball Mill Design/Power Calculation 911 Metallurgist
The basic parameters used in ball mill design (power calculations), rod mill or any tumbling mill sizing are; material to be ground, characteristics, Bond Work Index, bulk density, specific density, desired mill tonnage capacity DTPH, operating % solids or pulp density, feed size as F80 and maximum ‘chunk size’, product size as P80 and maximum The design of a ball mill can vary significantly depending on the size, the equipment used to load the starting material (feeders), and the system for discharging the output product. The size of a mill is usually characterized by the ratio “length to diameter” and this ratio most frequently varies from 0.5 to 3.5. TheGrinding in Ball Mills: Modeling and Process Control
احصل على السعر
Modelling the performance of industrial ball mills using
The ball mill modelling scheme using an ore- specific breakage distribution function in a multi-segment ball mill model has provided an adequate representation of industrial ball mill performance. Fur- ther work to extend this technique to ball mills less than 3.2 m in diameter and to mills operating at different process conditions is in progress.Figure 5. High–low wave ball mill liner Materials The selection of the material of construction is a function of the application, abrasivity of ore, size of mill, corrosion environment, size of balls, mill speed, etc. liner design and material of construction are integral and cannot be chosen in isolation.The Selection and Design of Mill Liners MillTraj
احصل على السعر
Design of horizontal ball mills for improving the rate of
Mechanochemical ball milling can degrade high concentrations of persistent organic pollutants (POPs) in contaminated soil and even pure chemicals easily and efficiently. There are many relevant laboratory studies that discuss the selection of reagents and mechanism of pollutant degradation. However, there are few related studies on large BALL MILL Specification Number A Process Data Sheet xxxx-xxx-xxx Sheet No : 1 of 2 Area: xxx Client : Operating Centre: Jakarta No. 1 Working 1 Service: ROM Ball Mill Item No: 1 of: Standby 0 xxxx-ML-001 2 (PDF) Ball Mill Datasheet mo kh Academia.edu
احصل على السعر
Tubular Rod Mills ScienceDirect
Figure 8.2 shows a flow sheet where the rod mill is in open circuit and the ball mill is in closed circuit with a classifier. This is a normal set-up as the primary function of a rod mill is to provide a uniform sized feed to the ball mill. Figure 8.3 shows that the rod mill product is classified and a more uniform feed size is, therefore, discharged to the ball mill The design results show that the minimum shaft power required to drive the ball mill is 0.2025 horsepower, the length of the mill at a fixed mill diameter of 210 mm is 373 mm, and the required(PDF) Design, Construction and Performance Analysis of a 5
احصل على السعر
EFFECTS OF GRINDING MEDIA SHAPES ON BALL MILL
Considering that worn balls in an industrial mill charge constitute about 15 to 40 percent and that the highest difference in breakage rate observed being nine percent for purely one shape charge; it is very doubtful whether it is worthwhile in attempting to develop techniques for removing worn balls from the mill.Since for the ball mill design we are using 80% passing, the required value of C2 for the ball mill will be equal to1.20. C3 is the correction factor for mill diameter and is given as; 𝐶𝐶3 = 2.44 𝐷𝐷 0.2 (3) However, it is important to note that C3 =0.914 vessel used in producing the ball mill was got from aDesign, Construction and Performance Analysis of a 5
احصل على السعر
Effect of ball size distribution on milling rate Request PDF
As balls are an integral element of the ball mill design, the impact of ball size d B on a T and μ T has been extensively studied (Austin et al., 1976a;Katubilwa and Moys, 2009).Design Method of Ball Mill by Discrete Element Method collected. The diameter of the gibbsite powder was measured using a Master Sizer 2000 (Sysmex Corpora-tion). Details of the experimental conditions are given in Table 2. Results and Discussion 1. Effects of Fins on Ball Motion in the Mill To predict ball mill grinding behavior using the dis-Design Method of Ball Mill by Discrete Element Method
احصل على السعر
Failure analysis of a ball mill located in a cement’s
In addition, a fatigue design curve for carbon and low alloy steels (metal temperatures not exceeding 370 °C) is shown in Fig. 4 for a load ratio, R, of −1. The diagram was obtained from Total Materia [4] and The French code RCC-M [5].It was further considered that, due to the ball mill’s corrosive environment, no fatigue limit applies View PDF; Download full issue; Search ScienceDirect. Powder Technology. Volume 380, March 2021, Pages 246-255. Design of horizontal ball mills for improving the rate of mechanochemical degradation of DDTs. Author links open overlay panel Xin Gao a b, Jing Song a b, The ball mill used in this study was a PM400 planetary mill Design of horizontal ball mills for improving the rate of
احصل على السعر- تكلفة كساره محجر
- stone crusher plant design sand making stone quarry
- صغيرة تايوان المحمولة آلة مطحنة مصنعين
- بيع معدات غسيل الرمل
- إجراء إنشاء مصنع كسارة الحجر في ولاية مهاراشترا
- mhada lottery for mill workers 2012 in india
- مطحنة عموم لفة الذهب مطحنة عموم الرطب بكفاءة عالية لمطحنة عداء حافة
- تثمين مطحنة ليمبول خام الذهب
- سلسلة طحن السوبر في الصين
- small rock ore crushers for sale
- التحذير من التكسير
- كسارة إنتاجية
- مطاحن الفحم الكرة عملية الرسم البياني
- china verified suppliers cement ball mills
- للبيع نيوزيلندي الحجر الجيري