اتصل
هاتف
+0086-371-86162511
عنوان
تشنغتشو ، الصين
cement ball mill chemical principles
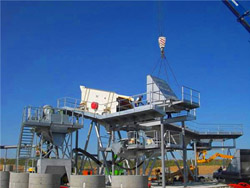
(PDF) Grinding in Ball Mills: Modeling and Process
A ball mill is a type of grinder widely utilized in the process of mechanochemical catalytic degradation. It consists of one or In this work, a cement ball mill (CBM) of a new generation cement plant is considered as a case study in order to study its efficiency based on both first and second Energy and exergy analyses for a cement ball mill of a new
احصل على السعر
Energy and cement quality optimization of a cement grinding circuit
As can be understood, the circuit is closed circuited and is composed of a two-chamber ball mill, a mill filter, an elevator and a high efficiency air classifier. Within Abstract. A first principles model of a cement grinding circuit is developed for the purpose of multi-variable model predictive control (MPC). The model is based on a MODELLING OF CEMENT GRINDING CIRCUITS FOR PREDICTIVE CONTROL
احصل على السعر
Operating principle of the ball mill Download
Download scientific diagram Operating principle of the ball mill from publication: Mechanical Activation of Construction Binder Materials by Various Mills The paper deals with the mechanicalA total of 40% of the total energy consumption of a cement plant is used in clinker grinding in a ball mill to produce the final cement product . Figure 1 shows the Predictive Controller Design for a Cement Ball Mill Grinding
احصل على السعر
Developing a soft sensor for fineness in a cement ball mill
Schematic of a ball mill operating under closed loop conditions approach is used in this work with an aim of developing a soft-sensor for the fineness of cement in a The model predictive controller (MPC) poses a viable solution to handle the variability. This paper addresses the design of predictive controller for the cement (PDF) Predictive Controller Design for a Cement Ball Mill
احصل على السعر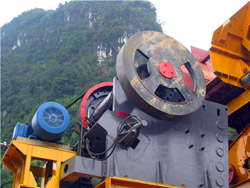
Ball milling: a green technology for the
The ball mill allows applying mechanical forces in the presence of chemical agents, therefore it represents an ideal method to combine chemical and mechanical actions to obtain CNCs. Factors that should be taken into The first compartment was modeled as two ball mills in series, diaphragm between the first and second compartments was represented as a screen and the second compartment is represented as one ball mill. Information given in the flowsheet is solids throughput (t/h), 80% passing size and % passing 0.01 mm. Download : Download full Cement grinding optimisation ScienceDirect
احصل على السعر
Cement Grinding 911 Metallurgist
A typical raw mix consists of 75-85% limestone, 12-25% shale, the balance consisting of silica or quartzite and iron oxide. Exact proportioning is dependent upon their chemical properties before and Ball Mills. Although ball mills were first introduced in the 1860’s, the main progress was made during the 1870’s to 1900’s in Germany, where its growing cement and chemical industriesCement Finish Milling (Part 1: Introduction & History)
احصل على السعر
What is a ball mill? What are its uses and advantages?
Ball Mill Features. Continuous operation and large capacity. High utilize ratio and low consumption of modifying agent. With the function of modifying and dispersion, it fits for variousFigure 1 presents the design of the clinker grinding system (closed circuit), which consists of a two-chamber ball mill and the separator (Plasari and T heraska, 19 81). Cement clinker is usuallyFig. 1: Design of clinker grinding system; mill and separator
احصل على السعر
Predictive Controller Design for a Cement Ball Mill
1 天前Keywords: ball mill grinding; state-space model; predictive controller; real-time simulator 1. Introduction The annual cement consumption in the world is around 1.7 billion tonnes and is5. Abstract The Ball mill is one of the most important equipment in the world of chemical engineering. It is used in grinding materials like ores, chemicals, etc. The types of ball mills: batch ball mill and continuous ball mill with different grinding media and different design depend on the nature of the input material and the nature of theBall Mill PDF SlideShare
احصل على السعر
Operational parameters affecting the vertical roller mill
A cement Vertical Roller Mill modeling based on the number of breakages. Vertical roller mills (VRM) are widely used to grind, dry, and select powders from various materials in the cement, electric power, metallurgical, chemical, and nonmetallic ore industries. For the sectors above, the VRM is a powerful and energy-intensive grinding We are manufacturer, supplier and exporter of ball mills according to ISI guidelines and user’s requirements since 1990 from Mumbai to India and all over the world. It is widely used for the cement, the silicate product, new-type building material, fire-proof material, chemical fertilizer, black and non-ferrous metal, glass, ceramics and etc.Ball Mill Promas Engineering Pvt. Ltd.
احصل على السعر
Ball Mill Balls Manufacturing Of High Quality Ball Mill Ball
Ball mill balls are usually made of high-hardness, high-strength materials, such as steel, ceramics, hard alloys, etc. Ball mill balls of different materials have different characteristics, for example, steel balls have the characteristics of high hardness, good wear resistance, and moderate price; ceramic balls have the characteristics of high wear resistance, good Keywords: Ball mills, grinding circuit, process control. I. Introduction Grinding in ball mills is an important technological process applied to reduce the size of particles which may have different nature and a wide diversity of physical, mechanical and chemical characteristics. Typical examples are the various ores, minerals, limestone, etc.Grinding in Ball Mills: Modeling and Process Control
احصل على السعر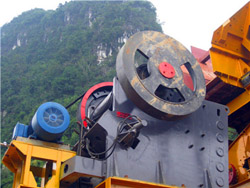
Ball Mill an overview ScienceDirect Topics
Quantum Nanostructures (QDs): An Overview. D. Sumanth Kumar, H.M. Mahesh, in Synthesis of Inorganic Nanomaterials, 2018 3.6.1.1 Ball Milling. A ball mill is a type of grinder used to grind and blend bulk material into QDs/nanosize using different sized balls. The working principle is simple; impact and attrition size reduction take place as the ball cement ball mills theories and principles pdf. A First Survey of Grinding with High Compression Roller Mills. Nevertheless,both operations consume much less energy thaan a ball mi
احصل على السعر
Vertical Cement Mill, Vertical Roller Mill Buy Cement Mill
The vertical works according to the principle of layer material to powder. Low energy, the powder consumption of vertical mill is 20%-30% less than that of ball mill. With the incensement of moisture of the raw material, the powder consumption will decrease obviously. The vertical mill saves 30%-40% of energy consumption compared to the ball UMS mills. 1.2 Principle of Operation In ball mill, ball has to be charged around 30-32% in first and second compartments. Balls are in the range of 50-90mm in coarse and 15-50mm in fine grinding. Grinding of material takes place by means of collision or attrition or tumbling action takes place between the balls and the charge.DESIGN AND ANALYSIS OF BALL MILL INLET CHUTE FOR
احصل على السعر
Effects of Mill Speed and Air Classifier Speed on
Cement ball mill reject sample from a industry located in Pakistan in Pezu District KPK. Study about cement was done for . Ordinary Portland cement with 5% gypsum content and 95% clinker. During the sampling time, the capacity of cement mill was 120 t/h and the specific energy utilization was 30 kWh /t and the Mill ballsChemical process industries are running under severe constraints, and it is essential to maintain the end-product quality under disturbances. Maintaining the product quality in the cement grinding process in the presence of clinker heterogeneity is a challenging task. The model predictive controller (MPC) poses a viable solution to handle Predictive Controller Design for a Cement Ball Mill Grinding
احصل على السعر
The effects of grinding media shapes on the grinding kinetics of cement
The effects of balls and cylinders on the clinker's specific rate of breakage were investigated. The results showed that the specific rate of breakage provided by cylinders is higher than that of balls. − 2.00 + 1.70 mm is an optimum feed size for 20 mm diameter balls and 20 × 20 mm diameter cylinders.At that feed size, the value of Si is
احصل على السعر- mining drilling equipment sales companies in gauteng
- محجرة الحجار عنابة جندل
- كسارة maquinas de uso en savannah georgia
- ماكنات صناعة عجينة المناديل
- catalogo chancadores jaws master
- ماشین آلات و روش الک کردن شن و ماسه
- اندونيسيا كسارات كسارة فكية
- شركة تعدين الفحم في اندونيسيا الوظيفي 202
- small scale gold mining equipment for sale auction
- الذهب معدات التعويم للبيع
- كسارة الحجر metode kerja penggunaan
- أفضل عمال المناجم الذهب الصغيرة
- sand or rocks dump trucks prices
- الفحم المطرقة مطحنة الصخور بيع
- ميتس vsi كسارة 100tph السعر