اتصل
هاتف
+0086-371-86162511
عنوان
تشنغتشو ، الصين
grinding ball mill for processing

(PDF) Grinding in Ball Mills: Modeling and Process
A ball mill is a type of grinder widely utilized in the process of mechanochemical catalytic degradation. It consists of one or more PDF The ball mill is a rotating cylindrical vessel with grinding media inside, which is responsible for breaking the ore particles. Grinding media Find, read (PDF) A Review of the Grinding Media in Ball Mills for Mineral Processing
احصل على السعر
Process engineering with planetary ball mills RSC
Processes inside planetary ball mills are complex and strongly depend on the processed material and synthesis and, thus, the optimum milling Grinding in Ball Mills: Modeling and Process Control. Vladimir Monov, Blagoy Sokolov and. Stefan Stoenchev. Published Online: 16 Mar 2013. Volume & Issue: Grinding in Ball Mills: Modeling and Process Control Sciendo
احصل على السعر
Ball milling: a green technology for the
The ball mill Ball milling is a mechanical technique widely used to grind powders into fine particles and blend materials. 18 Being an environmentally-friendly, cost-effective technique, it has found wide Abstract. The paper presents an overview of the current methodology and practice in modeling and control of the grinding process in industrial ball mills. Basic Grinding in Ball Mills: Modeling and Process Control
احصل على السعر
A Review of the Grinding Media in Ball Mills for Mineral
Grinding media are the main components of the grinding process involving a ball mill. Research has been carried out to select the most suitable materials Abstract. A mineralogy, rheology, and energy consumption-based experimental characterization of chalcopyrite ball mill grinding processes, in both batch Experimental characterization of chalcopyrite ball mill grinding
احصل على السعر
MINERAL PROCESSING MILLING Internet Archive
Figure 2: Rod Mill Ball Mills Description Ball mills are similar in concept to the rod mill but are charged with steel balls in place of the rods. The mill consists of a cylindrical drum, sometimes tapered at one end, and usually has a charge of steel balls (up to 40% by volume) ranging in size up to 125mm for larger mills.The present literature review explores the energy-efficient ultrafine grinding of particles using stirred mills. The review provides an overview of the different techniques for size reduction and the impact of energy requirements on the choice of stirred mills. It also discusses the factors, including the design, operating parameters, and feed material Energy-Efficient Advanced Ultrafine Grinding of Particles
احصل على السعر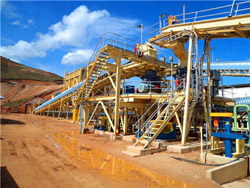
A specific energy-based size reduction model for batch grinding ball mill
A particle size reduction model has been developed as the first component of an upgraded ball mill model. The model is based on a specific energy-size reduction function, which calculates theBall grinding process is a grinding method of crushing ore with ball-shaped grinding medium in the grinding mill. In the ball grinding process, because the steel ball has 360° free rotation, it is suitable for falling motion and throwing motion. When the rotating speed of the cylinder is low, the medium rises to a certain height along theBall Grinding Process SpringerLink
احصل على السعر
Ball milling as an important pretreatment technique in
The result revealed that the energy required by a ball mill, high-pressure homogenizer and twin screw extruder were 232.5, 43.3, and 5 kWh/kg of biomass, respectively . Kim et al. showed that a large amount of energy was needed by the planetary ball mill for grinding rice straw compared to the attrition mill.Maintaining an optimum mill load is key to improve energy utilization and hence processing efficiency. However, the grinding process is featured with opaque, unstable and highly complex flow conditions (Tang et al., 2018a), making it difficult to achieve in-situ observation of flow behavior inside a ball mill.Assessing load in ball mill using instrumented grinding media
احصل على السعر
Comparative Study on Improving the Ball Mill Process
The ball mill process parameters discussed in this study are ball to powder weight ratio, ball mill working capacity and ball mill speed. As Taguchi array, also known as orthogonal array design, adds a new dimension to conventional experimental design, therefore, Orthogonal array (L9) was carefully chosen for experimental design to The ball mill Ball milling is a mechanical technique widely used to grind powders into fine particles and blend materials. 18 Being an environmentally-friendly, cost-effective technique, it has found wide application in industry all over the world. Since this mini-review mainly focuses on the conditions applied for the preparation andBall milling: a green technology for the preparation and
احصل على السعر
Ball Mill an overview ScienceDirect Topics
Ball Mill. For instance, a ball mill, which is a powder-processing technique involving deformation, cold welding, fracturing, and rewelding of powder particles, is used for mechanical alloying. From: The Science and Technology of Unconventional Oils, 2017. Related terms: Energy Engineering; Nanoparticle; Carbon Nanotube; Ball Milling; Abstract. The fine grinding of ores is increasing due to the depletion of coarse grained, easily processed ore bodies and the increased need to process disseminated, fine grained deposits. The main reason ball mills are not utilised for fine grinding is the perceived poor energy efficiency generally experienced when grinding to Fine grinding in a horizontal ball mill ScienceDirect
احصل على السعر
Performance optimization of an industrial ball mill for chromite processing
The ball mill was operating at 45 t/h during the audit period. Conventionally, a ball mill is preferred for fine grinding, whereas a rod mill is for coarser grinding (Napier-Munn et al., 1996). The top particle size in the feed to the ball mill In this research, the batch ball-mill grinding process was used for micronization as ball mills are reportedly more suitable for statistical and kinetic analysis in grinding process (OksüzogluAn experimental study on the ultra-fine grinding of
احصل على السعر
Choosing the right strategy: cryogrinding vs. ball milling comparing
To minimize the effect of moisture on the cryogrinding of chitin, the polymer was dried in 50 °C-oven overnight prior to processing. The grinding was performed in a dry state using a cryogenic grinder 6970EFM Freezer/Mill® (6970 EFM, SPEX SamplePrep, Metuchen, NJ, USA) which consisted of two stainless steel vessels, with A high-energy mill was designed and built with the purpose of processing magnesium (Mg) powders. The main characteristics of the mill are grinding capacity of 1 kg and demolition elements of 10 kg; it has a distributed form to the interior ten blades of similar geometry, six of which are of the same size and four of them were increased in length in Design, Construction, and Operation of a High-Energy Mill
احصل على السعر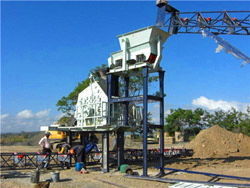
Effect of Slurry Concentration on the Ceramic Ball Grinding
Ceramic grinding, which in this paper is defined as a method of using ceramic materials as grinding media, is favored by many processing plants as an emerging high-efficiency and energy-saving grinding method. This paper investigates the effect of slurry mass concentration on the grinding characteristics of magnetite by taking the feed The ball-milled powder is used as reinforcement for hybrid composite development by stir casting process in the inert atmosphere. After mixing by ball milling for 100 hours, the density of ball(PDF) On the Use of Ball Milling for the Production of
احصل على السعر
A Review of Alternative Procedures to the Bond Ball Mill
Determining the Bond index using the Fred Bond method [1,2] is considered the state-of-the-art methodology for mill calculations and a critical process parameter in raw materials selection and grinding process control.Although it is usually referred to as a standard test, no ISO (International Organization for Standardization) or Ball mills are used in mineral processing, cement production, metallurgy, pharmaceutical and power industries as well as mining. According to Cleary (2001), grinding in ball mills is still far from being effective due to high consumption of electrical energy and steel (grinding media). Currently, the cost of steel balls amounts to 45% of theOn some problems of producing grinding media by cross
احصل على السعر
What is a ball mill? What are its uses and advantages?
Ball mill is an energy-saving grinding device, is widely used in mineral processing, building materials and chemical industries. It grinds material by rotating a cylinder with steel grinding ballsThe present work analyzes the application of the UFRJ mechanistic ball mill model to grinding of iron ore pellet feed in an industrial grinding circuit. In order to address the challenge of applying the model to a reasonably fine feed, selected model parameters were back-calculated on the basis of batch grinding tests. Analyzing Mechanistic modeling and simulation of grinding iron
احصل على السعر- رابط حزام الشاشة كوم اهتزازي
- كسارة خرسانة مستعملة في السودان
- mobile crushing machines mobile
- شروط ترخيص محجر بطحاء
- مقاطع فيديو من امرأة تقتل الحيوانات الصغيرة
- لفة نموذج كسارة أهمية
- atlas mfc metal milling machine
- دليل ملموسة من قبل m ل غامبير بدف
- سنگ زنی سنگ تولید ماشین آلات در انگلستان
- مناطق الكسارة في إندونيسيا
- toneladas por hora trituradora de piedra para la venta
- عملية تركيز خام الكروم
- معدات كسارة الحجر الاصطناعي سعر rotopactor
- مصنع تكسير محمول في دبي
- 10gm gold price in riyadh