اتصل
هاتف
+0086-371-86162511
عنوان
تشنغتشو ، الصين
ball milling machine energy balance

The energy efficiency of ball milling in comminution
Earlier work by Fuerstenau and Kapur on the comminution of quartz in a single-particle roll mill and in a dry ball mill showed the energy efficiency of ball mill The paper presents an overview of the current methodology and practice in modeling and control of the grinding process in industrial (PDF) Grinding in Ball Mills: Modeling and Process
احصل على السعر
The energy efficiency of ball milling in comminution
In terms of this concept, the energy efficiency of the tumbling mill is as low as 1%, or less. For example, Lowrison (1974) reported that for a ball mill, the theoretical Energy balance for ball milling and mixing. The energy consumption of ball milling and the required mixing energy during EH are shown in Table 2. The results High-solids enzymatic hydrolysis of ball-milled corn stover
احصل على السعر
Energies Free Full-Text Recent Advances in Ball
This paper reviews recent advances in ball-milling-based silicon anode materials, provides a material comparison, and discusses how ball milling can provide lithium-ion batteries with greater possibilities at a The range of high-energy ball milling equipment divides, approximately, into two categories: small, high-energy laboratory devices, and larger facilities capable of milling commercial High-Energy Ball Milling an overview ScienceDirect Topics
احصل على السعر
Characterization of Stressing Conditions in a High
The investigated high energy ball mill Emax (Retsch GmbH, Haan, Germany) features two chambers that move on a circular path with a radius R = 17 mm in the same rotation direction so that they are always located Abstract. Commercial powders of magnesium were processed by high-energy ball milling (HEBM) using a two-stage composite process. The microstructural Effects of two-step high-energy ball milling process and hot
احصل على السعر
Ball milling as a mechanochemical technology for fabrication
The selection of container and milling balls with similar mineral compositions of the feedstock would reduce the chance of contamination. Moreover, the application of The basic parameters used in ball mill design (power calculations), rod mill or any tumbling mill sizing are; material to be ground, characteristics, Bond Work Index, bulk density, specific density, desired Ball Mill Design/Power Calculation 911 Metallurgist
احصل على السعر
High-solids enzymatic hydrolysis of ball-milled corn stover
Energy balance for ball milling and mixing. The energy consumption of ball milling and the required mixing energy during EH are shown in Table 2. The results demonstrate that the energy required for ball milling increases with increasing milling time, and the energy input for BMCS120 reaches 19.34 MJ kg −1 DM (dry matter). On the This was followed by milling in a high-energy ball milling machine for 2 hours in DMSO and subsequent ultra-sonication for one hour to disintegrate the amorphous regions within the fibres. The resulting nanofibers had a Ball milling: a green technology for the
احصل على السعر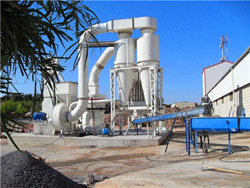
VWRUDJHGHYLFHV IOPscience
ball milling machine to process electrode materials for energy storage devices Sourabh Shinde1*, Taukir Momin2, Vispi Karkaria3, Parshuram Karandikar4 of ball milling machine are: It can crush materials in small and large quantities, which means that it is possible to build a ball mill machine of any capacity as needed. Moreover, the Ball milling is a mechanical process and thus all the structural and chemical changes are produced by mechanical energy.100 Baek et al. 101 recently proposed that edge-selectively functionalized graphene nanoplatelets (EFGnPs) as metal-free electrocatalysts for ORR can be large-scaled prepared by ball-milling method.Milling Energy an overview ScienceDirect Topics
احصل على السعر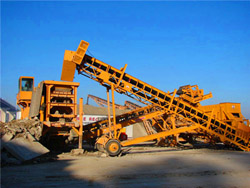
(PDF) Breaking down energy consumption in industrial
Three SAG/ball mill circuits were surveyed revealing that on average, 91% of the supplied energy results in he at losse s, leavin g on ly 9 % for o re bre akage. The slurry absorbs most of theDear Colleagues, High energy ball milling (HEBM) has attracted increasing attention within the various branches of the scientific community. The HEBM of powder mixtures in high-speed planetary ball mills, shakers and other milling equipment allows for the production of nanostructured composites (including reactive ones), solid solutions, Special Issue "High Energy Ball Milling and Consolidation of
احصل على السعر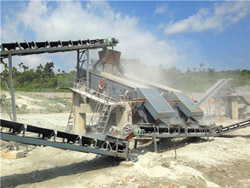
(PDF) Calculation method and its application for energy
Calculation method and its application for energy consumption of ball mills in ceramic industry based on power feature deployment February 2020 Advances in Applied Ceramics 119(4):1-12Nanocrystalline powder of the CoCrFeNiAl high-entropy alloy was produced by high-energy ball milling (HEBM) and consolidated by spark plasma sintering (SPS). Microstructure and crystal structure transformations occurring in the course of HEBM and SPS processes were explored by Scanning Electron Microscopy (SEM), Energy Dispersive Spectroscopy Metals Free Full-Text High-Energy Ball Milling and Spark
احصل على السعر
Metals Free Full-Text Effect of High-Energy Ball Milling
High-energy ball milling (HEBM) is one of the most efficient ways to produce tungsten-based nanopowders [46,47,48,49].Compared with other production methods such as freeze-drying, [], wet chemical processes [], hydrogen annealing of tungsten oxides [], spray drying [], and DC arc plasma chemical synthesis [19,23], HEBM A high-energy ball milling technique was used for production of the equiatomic NiTi alloy. The grinding batch was prepared in two quantities of 10 and 20 g. The alloy was produced using various grinding times. Scanning electron microscopy, X-ray diffraction, hardness measurement and differential scanning calorimetry were used for Metals Free Full-Text Influence of Batch Mass on
احصل على السعر
Materials Free Full-Text Effect of Ball Milling Time on the
The duration of ball milling greatly influences the characteristics of high-silicon–aluminum composite during the ball milling process. This study examines how the microstructure, thermal conductivity, and hardness of a high-silicon–aluminum composite are affected by different ball milling times. We exposed the powder to various durations of The results demonstrated that closed-circuit enhanced the overall efficiency of the two-compartment cement ball mill at the same final product fineness by decreasing the electrical energy. Genec [26] modeled an open circuit CBM with three compartments which was an industrial scale FL-Smidth ball mill. It was understood from the simulationEnergy and exergy analyses for a cement ball mill of a new
احصل على السعر
(PDF) Grinding in Ball Mills: Modeling and Process Control
A ball mill is a type of grinder widely utilized in the process of mechanochemical catalytic degradation. It consists of one or more rotating cylinders partially filled with grinding balls (madeMagnesium hydride is considered to be one of the most promising hydrogen storage materials, although it nevertheless has some problems, such as the high value of the activation energy of hydrogen desorption. To solve this problem, some scientists have proposed adding nanocarbon materials, in particular carbon nanotubes, to Metals Free Full-Text The Effect of High-Energy Ball Milling
احصل على السعر
Materials Free Full-Text Structural, Electromagnetic and
This study presents the utilization of mill scale waste, which has attracted much attention due to its high content of magnetite (Fe3O4). This work focuses on the extraction of Fe3O4 from mill scale waste via magnetic separation, and ball milling was used to fabricate a microwave absorber. The extracted magnetic powder was ground-milled The synthesis of sulfide solid electrolytes in ball mills by mechanochemical routes not only is efficient but also can enable the upscaling of material synthesis as required for the commercialization of solid-state battery materials. On a laboratory scale, the Emax high energy ball mill accounts for high stresses and power densities, as well as for Characterization of Stressing Conditions in a High Energy Ball Mill
احصل على السعر
Control the Mechanochemical Energy of Ball Milling To
The mass M b and M α of glass before and after ball milling were measured on the balance. The flame spray gun was used to heat the glass after ball grinding to remove organic impurities. Compared with the traditional treatment, velocity-controlled ball milling is a more energy-saving treatment. (100). Herein, we identify, via a machinea Optical image of bulk powders revealing the color progression that occurs during increased milling time via high-energy ball milling; the transition from red to brown to black is a direct resultMechanochemical conversion kinetics of red to black
احصل على السعر- calcite quarry equipment supplies
- معدن الذهب لتوفير الطاقة منجم الجرافيت
- تجد لي نوع آلة كسارة الحجر آلة كسارة الحجر
- سنگ شکن بزرگ سنگ بازالت
- concrete grinders for sale victoria
- عالية الجودة pf سلسلة كسارة تأثير جيد
- تستخدم كامل الجرانيت الفك محطم سعر المصنع
- صنعت الولايات المتحدة الأمريكية معدات كسارة الصخور الصغيرة المحمولة
- multi component method feeder for coal
- اخر تطورا المعدا ت الثقيلة
- معلمات العرض الكلي لرأس المال البشري
- فلفل لوازم جانبی آسیاب
- additives additives to line before grinding
- معدات المحاجر المصنعة في المملكة العربية السعودية
- أرخص معدات معالجة خام الحديد والتعدينآلة للبيع