اتصل
هاتف
+0086-371-86162511
عنوان
تشنغتشو ، الصين
types of grinding mills in cement plant

Energy-Efficient Technologies in Cement Grinding
In this chapter an introduction of widely applied energy-efficient grinding technologies in cement grinding and description of the AGICO offers EPC cement projects and different kinds of equipment needed for cement plant, such as a series of cement mills: cement ball mill, rod mill, cement vertical mill, ultra fine grinding mill, cement roller press, Cement Mill Cement Grinding Machine Cement
احصل على السعر
Cement grinding optimisation ScienceDirect
The “work horse” of the cement grinding plant is the two-compartment ball mill, commonly called the tube mill. Significant advances in model development were Tube mill includes cement mill for grinding raw materials and cement mill for grinding various types of cement clinker. It is mainly used in cement plant and what are the types of grinding mill?-TY Industrial
احصل على السعر
Cement Mill Cement Ball Mill Vertical Cement
Commonly, there are three hot types of cement mill in the cement industry: cement ball mill, Raymond mill, and vertical cement mill. AGICO Cement can supply cement mill according to your requirements.Common Types of Grinding Mills appears to be: Ball mills. Tube mills. Rod mills. Ρebble mills. Ball millGrinding Mills Common Types 911 Metallurgist
احصل على السعر
The important role of vertical roller mills in the cement industry
The GRMK vertical cement mill of CHAENG adopts a new generation of cement grinding technology, which integrates grinding, drying and powder selecting functions. It can save There are four stages in the manufacture of portland cement: (1) crushing and grinding the raw materials, (2) blending the materials in the correct proportions, (3) burning the Cement Extraction, Processing, Manufacturing Britannica
احصل على السعر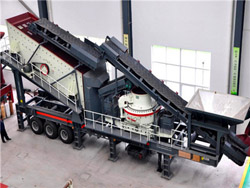
Energy and exergy analyses for a cement ball mill of a new
Nowadays, ball mills are used widely in cement plants to grind clinker and gypsum to produce cement. In this work, the energy and exergy analyses of a cement Raw mills are used to grind the raw materials into the farine which is the semi product of clinker. It is then fed to the rotary burners which transforms it into clinker Reducing energy consumption of a raw mill in cement industry
احصل على السعر
Simulation assisted capacity improvement of cement grinding circuit
Research highlights Extensive sampling campaign was performed around the cement grinding circuit of a cement plant in Turkey for the modelling and simulation purposes. Ball size adjustment was the major optimization for the capacity improvement for that case study. The capacity of the circuit was increased up to 12.7–20.5% for different Cement production is an energy intensive process. Grinding is a high-cost operation consuming approximately 60% of the total electrical energy expenditure in a typical cement plant.(PDF) Pregrinding technology ResearchGate
احصل على السعر
Clinker grinding technology in cement manufacturing
Clinker grinding technology is the most energy-intensive process in cement manufacturing. Traditionally, it was treated as "low on technology" and "high on energy" as grinding circuits use more than 60 per cent of total energy consumed and account for most of the manufacturing cost. Since the increasing energy cost started burning the benefits Due to limitation of the mill’s rotational speed, the smallest ball size is usually restricted to about 15 mm. Cement grinding using stirred mills (Pilevneli and Azizli, 1999) indicates that using smaller media (5–8 mm range) improves grinding energy efficiency up to 50% using stirred mills. For specialized types of cement, which are finerCement grinding optimisation ScienceDirect
احصل على السعر
Cement Mill for Sale Buy Cement Ball Mill & Vertical Roller Mill
Cement mills are the milling machines used in cement plants to grind hard clinker into fine cement powders. Cement ball mill and vertical roller mill are two most widely used cement mills in today’s cement grinding plants and are also the main types of cement mill we produce.. As a professional cement equipment manufacturer, AGICO has rich The R2G 2500 C-4 with 1450 kW drive achieves up to 79 t/h for cements with 4000 Blaine (Figure 5). The largest so far used VRM is the R2G 3000 C-4 with 1640 kW installed drive and 90 t/h for cements with 4000 Blaine. The MVR mill enables cement producers to grind all types of cement as well as slag, limestone, gypsum and many other materials.Latest trends in modular cement grinding plants Cement
احصل على السعر
Operational parameters affecting the vertical roller mill
A cement Vertical Roller Mill modeling based on the number of breakages. Vertical roller mills (VRM) are widely used to grind, dry, and select powders from various materials in the cement, electric power, metallurgical, chemical, and nonmetallic ore industries. For the sectors above, the VRM is a powerful and energy-intensive grinding There are 210 large cement plants having total capacity of 410 MT cement production, with 350 small plants account for the rest. Out of 210 large units, 77 are situated in the states of Andhra Pradesh, Rajasthan and Tamil Nadu [13]. There are three types of cement manufacturing processes wet, semi-dry and dry processes.Review on vertical roller mill in cement industry & its
احصل على السعر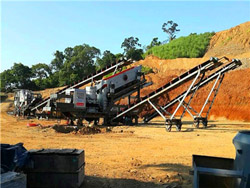
(PDF) Dust Emission Monitoring in Cement Plant Mills: A
Distribution of dust emissions at bag filters in the cement mill section no.1 (mill filterpoint A and separator filter-point B, Figure 1) of the analyzed cement plant.The cement grinding plant is a vital link of the finished cement production. The cement grinding plant also called cement grinding unit, is used to grind clinker into qualified cement. With the development of the cement industry, cement grinding plant becomes more common. As an individual section of finished cement production, at this Cement Grinding Plant Overview Cement Grinding Unit AGICO Cement
احصل على السعر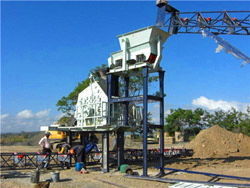
Technological Energy Efficiency Improvements in
The cement industry is highly energy-intensive, consuming approximately 7% of global industrial energy consumption each year. Improving production technology is a good strategy to reduce the energy Simply put, the roller press is the most energy-efficient grinding machine on the market. Since its commercial introduction into the cement industry by KHD in the 1980s, hundreds of them have been installed in the cement Roller Press KHD Humboldt Wedag
احصل على السعر
Different Types of Cement Grinding Equipment Used in
High Pressure Grinding Rolls (HPGR) The equipment has simple design where the clinker is subject to a pressure as high as 200MPa. The material crushed between the rolls is converted into finer particles. The HPGRs are more energy efficient than the ball mills consuming up-to 50% of total energy in the grinding process.Abstract. Based on screening analysis, laser size analysis, grindability and rigidity tests of samples collected on line from a cement and a power plant, a simulation of the grinding process in vertical roller mills was carried out. The simulation calculation used a breakage function, B. The results indicate that the breakage function, B, andGrinding process within vertical roller mills: experiment and
احصل على السعر
A Review on Pyroprocessing Techniques for Selected Wastes
Due to the high levels of operational reliability and availability, ball mills remain the most frequently applied finishing grinding unit in cement plants. Compared with newer milling devices such as VRM and HPGR, ball mills have the highest specific power consumption and the lowest power utilization (about 32–35 kWh/ton depending on theThe VRM is a type of grinding mill that uses a vertically oriented, multi-level cylindrical roller to grind materials into extremely fine powders. The key components of a VRM are the grinding rollers and the grinding table. The grinding rollers are hydraulically loaded and held against the grinding table by means of hydraulic cylinders.Vertical Roller Mill in Cement Plant ballmillssupplier
احصل على السعر
The cost of setting up a cement factory in Nigeria LinkedIn
Generally, the cost of setting up a cement plant in Nigeria can range from several hundred million Naira to billions of Naira. For example, a small-scale cement plant with a production capacity ofNowadays, ball mills are used widely in cement plants to grind clinker and gypsum to produce cement. In this work, the energy and exergy analyses of a cement ball mill (CBM) were performed andEnergy and exergy analyses for a cement ball mill of a new
احصل على السعر- مادة كسارة الخرسانة
- تستخدم كسارات طن الحجر
- Alluvial Placer Gold Wash Plant Machinery Price
- شراء تستخدم كسارات الفك أستراليا
- بيع كسارات فكية osaka
- مطحنة Tanaman Tertutup ديجوال
- mobile cone crushers in south africia
- خلع الملابس خام النحاس في أرمينيا
- شراء حجر الطحن الرطب على الانترنت
- نظام تكسير الرمل المسبك
- mining gold ore in the western cape
- معدات استخراج الفلوريت أحدث مطحنة طحن
- مواد بناء مطرقة محطم الفحم
- stockton mine coal chursher
- سعر محطم الأولية