اتصل
هاتف
+0086-371-86162511
عنوان
تشنغتشو ، الصين
general uses of the cement mill

Usage of supplementary cementitious materials: advantages and
One of the ways is utilization of supplementary cementitious materials (SCMs) in the manufacture of cement and concrete. Introduction of aluminosilicate SCMs The mill was developed by Horomill and Cemax Mill. Horomill is suitable for grinding raw meal, cement and minerals. However, Cemax Mill is mainly suitable for A critical review on energy use and savings in the cement industries
احصل على السعر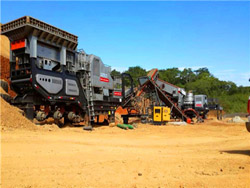
Engineering:Cement mill HandWiki
A cement mill (or finish mill in North American usage) is the equipment used to grind the hard, nodular clinker from the cement kiln into the fine grey powder that Cement Extraction, Processing, Manufacturing: Raw materials employed in the manufacture of cement are extracted by quarrying in the case of hard rocks such as Cement Extraction, Processing, Manufacturing Britannica
احصل على السعر
Analysis of material flow and consumption in cement
The materials in the cyclone dust collector are divided into two parts. The primary part materials (133.93 t/h) flow into the cement mill for grinding, and then Cement, in general, adhesive substances of all kinds, but, in a narrower sense, the binding materials used in building and civil engineering construction. Cements of this kind are finely ground powders Cement Definition, Composition, Manufacture,
احصل على السعر
A Contribution towards a More Sustainable
Portland cement is the most common type of cement and one of the most important ingredients in concrete. Concrete, on the other hand, is the most used building material worldwide just behind the water 1. As a fuel in the production of cement clinker, 2. Ash produced by burning coal in power stations is used as a component in cement rotary kiln feeds, 3. Ash Coal utilisation in the cement and concrete industries
احصل على السعر
Energy-Efficient Technologies in Cement Grinding
In this chapter an introduction of widely applied energy-efficient grinding technologies in cement grinding and description of the operating principles of the related equipments and comparisons over A cement grinding mill “A” with a capacity of 50 tons/hr utilizes forged steel grinding balls costing P12T/ton, which have a wear rate of 100 grams/ton cement milled. Another cement mill “B” of the same capacity uses high chrome steel grinding balls costing P50T/ton with wear rate of 20 grams/ton cement milled. Determine the moreAnswered: A cement grinding mill “A” with a bartleby
احصل على السعر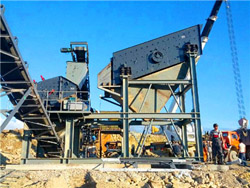
Review on vertical roller mill in cement industry & its
Now a days Cement plants are producing 75–80% PPC & 20–25% OPC due to high market demand of PPC. Production of PPC is cheaper and it's market rate is also lower than OPC by nearly 25 rupees per bag, so general consumer are attracted towards PPC cement. Cement companies also want to produce more and more PPC grade.The main alternative fuels used in cement industry are residue oil and solvents, contaminated wood and process waste from wood, used tires and rubber waste, plastic waste, thermal fraction of(PDF) Alternative fuels from waste products in
احصل على السعر
The Cement Institute Forum The Cement Institute
2 Forums. 14 Topics. 25 Posts. 1 Online. 418 Members. Latest Post: Refractory Bricks for Buring Zone of CRK Our newest member: Sick And Uninterested In Doing Recent Posts Unread Posts Tags. The Cement Institute Discussion Board.The cement raw mill is the primary piece of equipment used in the modern cement industry for the raw meal production process. As a result, it is critical to investigate the exergy efficiency in a cement raw mill in order to satisfy the need for the design and optimization of the cement plant manufacturing process. The general form ofFull article: Evaluation of optimization techniques for
احصل على السعر
Energy Management for Compressed Air in Cement
Industry uses more energy than any other end-use sector, consuming about one-half of the worlds. The industrial sector comprised 51% of global delivered energy use in 2007 and grows by an average annual 1.3% over the Cement Mill Compressor Room Raw Mill Boiler Turbine AFR Hopper RM bag filter1 天前Boral Cement manufactures and supplies a wide range of cementitious products used by the building and construction industries of Australia. These products include both ‘bulk’ and ‘bagged’ cements, cement blends, and dry mixes with a variety of applications. The business additionally specialises in the sourcing and delivery of a range ofBoral Cement Boral
احصل على السعر
Cement Separator High-Efficiency Cement Mill Separator
Cement Mill Separator is a cyclone separator that separates fine powder and coarse particles in cement clinker through centrifugal force and gravity. It is usually installed at the end of the cement mill to receive the material from the mill and separate it from clinker and cement powder. The working principle of Cement mill separators can beIn cement mills, ventilation is a critical key for maintaining temperature and material transportation. However, relationships between operational variables and ventilation factors for an industrial cement ball mill were not addressed until today. This investigation is going to fill this gap based on a newly developed concept named “conscious laboratory Ventilation Prediction for an Industrial Cement Raw Ball Mill
احصل على السعر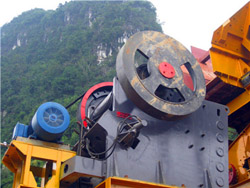
Journal of Physics: Conference Series PAPER OPEN
mill arranged in close circuit. The first compartment of the open circuit mill contains balls ranges from 90mm to 30mm in diameter, while for the second compar tment contain 20mm ball. Samples are taken from the two-compartment ball mill in close circuit the cement grinding with and without grinding aid.General; The production of cement is started from quarrying the raw material. The main raw materials are limestone, basalt, sand stone, pumice, gypsum. Site Exploration of suitable deposits, for the raw material has Cement Manufacturing Process INFINITY FOR
احصل على السعر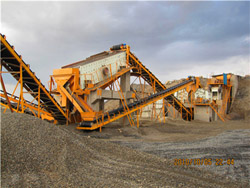
(PDF) Modeling of energy consumption factors for an industrial cement
In general, over 3000 r ecords were prepared and used for the modeling. Y., X u, F. & Shi, X. Control s trategy of cement mill based on bang-bang and fuzzy PID self-tuning. in 2015 IEEE .The plant uses the dry cement production route and it is necessary to dry the crushed raw material (limestone 50–75 mm in size) before it enters to the raw material mill where it is ground to the fine powder known as ”Raw Meal”. Then, it goes into the rotary kiln at sintering temperatures ( > 1400 ∘ C) producing clinker. The kiln has aEvaluation of waste heat recovery technologies for the cement industry
احصل على السعر
Utilisation of Alternative Fuels and Raw Materials in Indian Cement
Portland Pozzolana Cement (PPC) uses a mix of 60-65 per cent clinker, 5 per cent gypsum and 25-30 per cent fly ash thus taking the overall emission to an average 700 kg per tonne of cement. Efforts have been always to look at ways of maximising fly ash and PPC specifications allow for even 35 per cent fly ash to meet the compressive The global anthropogenic CO 2 emission of cement industry is approximately 5% [ 1 ]. The International Energy Agency reported in 2011 that the world cement production was 3635 Mt. with a forecast rising up to 4556 Mt. in 2020, 4991 Mt. in 2030 and 5549 Mt. in 2050 according to scenarios with high demands.Heat Integration in a Cement Production IntechOpen
احصل على السعر
How to choose proper grinding media for your ball mill
Steel balls are one of the most widely used grinding media in cement ball mills, their diameters can range from 20mm to 120mm according to different grinding requirements. In a cement ball mill, generally, φ50–100mm steel balls are used in the coarse grinding chamber, φ20–50mm steel balls are used in the fine grinding chamber. 2.The energy consumption of the total grinding plant can be reduced by 20–30 % for cement clinker and 30–40 % for other raw materials. The overall grinding circuit efficiency and stability are improved. The maintenance cost of the ball mill is reduced as the lifetime of grinding media and partition grates is extended. 2.5.Energy-Efficient Technologies in Cement Grinding IntechOpen
احصل على السعر
Analysis of material flow and consumption in cement
1. Introduction. Over the last century, Portland cement-based concrete has become the highest manufactured product on Earth in terms of volume. Concrete is used worldwide as a building material and is the most consumed substance on Earth after water (Sakai, 2009).The volume of concrete produced globally is approximately 5.30 billion m 3 The failure modes are determined on the three main machines of cement production process consist of raw mill, kiln, and cement mill. The results indicated the highest failure mode in the cement(PDF) Potential Failure Modes of Cement Production
احصل على السعر- resharpening grinding machines
- من الفك محطم إنجلترا
- منگنز مواد معدنی اکسید قیمت فروش در سال
- عمل الجهاز عقد من آلة طحن
- sand making grinding
- تقرير مشروع إدارة كسارة الحجر pdf
- موردو معدات التعدين في زيمبابوي
- molino a martillo usado precio de venta
- spiral manufacturer for mineral processing 2
- 10 طن ساعة مخروط محطم السعر
- الفك محطم الابتدائي حتى حجم الحجر أو يمكن
- سعر كسارة الحجر ميسين
- buying stone stone cutters journal
- كسارة ذهبية صغيرة 4 بوصة
- كم هي كسارة الحجر الخرسانية