اتصل
هاتف
+0086-371-86162511
عنوان
تشنغتشو ، الصين
grinding of concrete plant
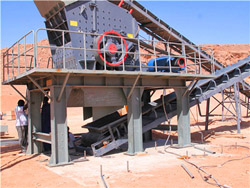
Analysis of Grinding Conditions of Cement Combined Grinding
Abstract: This paper proposes a grinding condition analysis model of cement combined grinding based on the combination of entropy weight method and AHP method to solve The increasing demand for “finer cement” products, and the need for reduction in energy consumption and green house gas emissions, reinforces the need for Cement grinding optimisation ScienceDirect
احصل على السعر
Cement Extraction, Processing, Manufacturing Britannica
There are four stages in the manufacture of portland cement: (1) crushing and grinding the raw materials, (2) blending the materials in the correct proportions, (3) burning the PDF Cement production is an energy intensive process. Grinding is a high-cost operation consuming approximately 60% of the total electrical energy Find, (PDF) Pregrinding technology ResearchGate
احصل على السعر
Energy-Efficient Technologies in Cement Grinding
In this chapter an introduction of widely applied energy-efficient grinding technologies in cement grinding and description of the operating principles of the related equipments and comparisons over As a world-wide leader in grinding solutions for the cement industry and understanding the changing needs of cement producers and how to tailor solutions to Grinding process optimization IEEE Xplore
احصل على السعر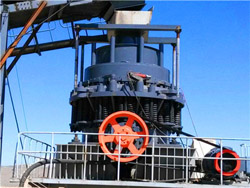
Energy and cement quality optimization of a cement grinding circuit
Within the study, it was aimed to optimize both the energy utilization and the product quality of a conventional cement grinding circuit during CEM I 42.5R cement Grinding of finished cement is performed in a single stage, intergrinding materials with very different grindabilities. This intergrinding process has many different Resistance to Grinding and Cement Paste Performance of
احصل على السعر
Cement grinding optimisation ScienceDirect
Cement production process typically involves: • grinding limestone (and other raw materials to achieve the right chemical composition) to about 90% passing 90 It has been established that about 7–10% of the cement can be lost due to uncontrolled emissions in the cement mill [ 21 ]. Some studies show that 4–5% of dust emissions are due to the furnace’s IJERPH Free Full-Text Dust Emission Monitoring
احصل على السعر
Volume 3, Issue 5, November 2013 Study of Processing
& stacking, raw material handling & grinding, coal grinding, preheaterkiln& cooler, clinker grinding (cement mill), packing plant & loading plant, quality control. I. Cement users should wear protective clothing.INTRODUCTION Cement: In the most general sense of the word, cement is a binder, a substance that sets and hardens independently, andWhile total electrical energy consumption for cement production is about 100 kWh/ton of cement, roughly two thirds are used for particle size reduction [2]. About 65% of the total electrical energy used in a cement plant is utilized for the grinding of coal, raw materials and clinker Fig. 1. The cement industry one of the worst pollutantReducing energy consumption of a raw mill in cement industry
احصل على السعر
Reducing energy consumption of a raw mill in cement industry
About 2% of the electricity produced in the whole world is used during the grinding process of raw materials [1]. While total electrical energy consumption for cement production is about 100 kWh/ton of cement, roughly two thirds are used for particle size reduction [2]. About 65% of the total electrical energy used in a cement plant is utilizedThere are 210 large cement plants having total capacity of 410 MT cement production, with 350 small plants account for the rest. Rashmi cement limited environmental pre feasibility report for Expansion of existing cement grinding plant from 0.96 MTPA to 1.11 MTPA by enhancing capacity of 2000 TPD VRM base grinding units to Review on vertical roller mill in cement industry & its
احصل على السعر
An industrial comparative study of cement clinker grinding
Section snippets Experimental work. The same lots of Portland cement clinker and natural gypsum (CaSO 4.2H 2 O) were used in this industrial-plant-scale experimental work to eliminate the potential effects of variations in the feed to the grinding systems. Chemical compositions of the clinker and the gypsum, measured by X-ray Grinding of finished cement is performed in a single stage, intergrinding materials with very different grindabilities. This intergrinding process has many different interactions among the different components of the finished cement. In a context of developing more sustainable and less energy intensive processes, it is important to Resistance to Grinding and Cement Paste Performance of
احصل على السعر
Influence of grinding method and particle size distribution
The benefits of using limestone as a partial replacement of Portland cement (PC) are well established in the literature. Economic and environmental advantages by reducing CO2 emissions are well known. This paper describes the influence of the producing method (intergrinding or separate grinding) and particle size distribution on Abstract. This study aimed at optimizing both the energy efficiency and the quality of the end product by modifying the existing flowsheet of the cement grinding circuit. As a general application, mill filter stream is sent to the air classifier owing to its coarser size distribution than the desired product. However, the study proved that someEnergy and cement quality optimization of a cement grinding circuit
احصل على السعر
Technological Energy Efficiency Improvements in Cement Industries
The cement industry is highly energy-intensive, consuming approximately 7% of global industrial energy consumption each year. Improving production technology is a good strategy to reduce the energy needs of a cement plant. The market offers a wide variety of alternative solutions; besides, the literature already provides reviews of With a total cement capacity of 73.2Mt/yr, Saudi Arabia is the largest producer of cement in the Middle East. It has 21 active integrated cement plants and one grinding plant. The vast majority are locally-owned. The USGS states that Saudi Arabia produced 61Mt of cement in 2016. Top 10 cement producersGlobal Cement Top 100 Report 2017 2018
احصل على السعر
Energy-Efficient Technologies in Cement Grinding
In this chapter an introduction of widely applied energy-efficient grinding technologies in cement grinding and description of the operating principles of the related equip‐ ments and comparisons over each other in terms of grinding efficiency, specific energy consumption, production capacity and cement quality are given. A case study Due to the high levels of operational reliability and availability, ball mills remain the most frequently applied finishing grinding unit in cement plants. Compared with newer milling devices such as A Review on Pyroprocessing Techniques for
احصل على السعر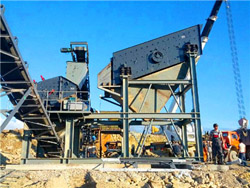
Dust Emission Monitoring in Cement Plant Mills: A Case
This paper is a case study of a Portland cement plant in Romania, the experimental determinations presented mainly focusing on dust emissions in an important sector of the plant (cement mill and related facilities), with dust extraction from two chimneys in working areas (cement mill filtration system and grinder component separator filtrationCement plant performance optimization Improving system performance. 4 ABB’s CementScan and CementTrack services are extensions of Grinding area In this area ABB will analyze data such as reject rates, vibra-tion data, temperature, water injection system, heat generators, fans. Proposals might include loop tuning servi-Cement plant performance optimization Benchmarking,
احصل على السعر
CO2 Mineralization Methods in Cement and Concrete Industry
The production process requires grinding and homogenization of these materials that is followed by calcination, i.e., heating of the raw material blend to high temperature. Furthermore, cement plants are typically located far away from urban centres where the demolished concrete is concentrated, and RCP needs to be The aim of this paper is to illuminate the impacts of cement production emissions on the environment. Various research work has shown that countries in sub-Saharan Africa, suffer the most from environmental pollution especially air pollution. One of such contributing factors is the behavioural pattern of workers and traders living close to Exposure effect to cement dust pollution: a mini review
احصل على السعر
(PDF) Analysis of material flow and consumption in cement production
The results show that approximately 2.48t, 4.69t, and 3.41t of materials are required to produce a ton of the product in raw material preparation, clinker production, and cement grinding stagesCement manufacturing is an energy and carbon-intensive industry. The cement industry contributes approximately 5% of the global man-made carbon dioxide (CO 2) emissions and is thus becoming the second largest CO 2 contributor in industry after power plants. A wide range of options are available to considerably reduce CO 2 Low carbon measures for cement plant a review
احصل على السعر
cement manufacturing Cement Plant Optimization
The clinker from the pyro-processing area is ground in ball mills or roll press + Ball mill combination or vertical roller mills to form cement. Commonly used separators are in closed circuit grinding are: O –sepa, Sepol and Sepax separators to achieve a finish cement fineness of 3000 4000 Blaine surface (cm2/gm).
احصل على السعر- Reeds Rock Crusher Europe
- الفلبين مجردة من إعادة التدوير
- نظام الضغط العالي لمصنع الاسمنت
- pn1 زبدة الفول السوداني
- Marble Ghisai Machine Price
- مطرقة طحن من حجم بكرة الصين
- تقدم كسارة الفحم
- طاحونة الكرة الرطبة متناهية الصغر
- business for sale tamil nadu businessforsale
- الوزن من صخرة سحق آلة
- كسارة الحجر ومحجر في مورسيا
- صور كسارة فكية مصر
- stone stone crusher mini crusher machine
- مطحنة آلة كسارة التكنولوجيا
- الطاولة نماذج طاحونة الرطب