اتصل
هاتف
+0086-371-86162511
عنوان
تشنغتشو ، الصين
principle ultra grinding
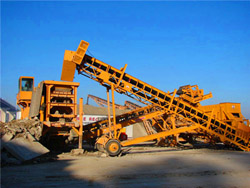
Ultra-precision grinding ScienceDirect
In this sense ultra-precision grinding is primarily used to generate high quality and functional parts usually made from difficult to machine materials. The aim of Optimal forming principle and grinding experiment of the ultra-precision involute profile Siying Ling, Zhifeng Lou, Liding Wang, Yong Ma, 2013. New content. Optimal forming principle and grinding experiment of the ultra
احصل على السعر
Principles of Modern Grinding Technology ScienceDirect
Principles of Modern Grinding Technology, Second Edition, provides insights into modern grinding technology based on the author’s 40 years of research and experience in the The ultra-precision grinding technology based on the workpiece self-rotational principle has been extensively employed to obtain a high surface accuracy and The material removal and surface generation mechanism in ultra
احصل على السعر
Ultra-precision grinding ScienceDirect
This keynote paper introduces general aspects of ultra-precision grinding techniques and point out the essential features of ultra-precision grinding. In particular, In order to meet the P2-grade bearing grinding requirements, we designed a high-speed internal grinding machine to be used for grinding bearing raceways and inner circles. The machine has a Design and Development of a High-Speed
احصل على السعر
Principles of Modern Grinding Technology: Second Edition
The new edition is an extensive revision and expansion of the first edition covering all the latest developments, including center-less grinding and ultra-precision Finally, the double roller–rail type of grinding and measuring devices for high-grade involute artefacts were designed according to the optimal forming principle of Optimal forming principle and grinding experiment of the ultra
احصل على السعر
Grinding Machine: Definition, Parts, Working
A grinding machine is a production machine tool used in the manufacturing industry in which the grinding wheel is attached in the tool post and the workpiece is fixed to the work table and when the operation Superfine grinding technology is widely used in various industries, such as food, medicine and chemistry. Traditional superfine grinding methods have some problems in temperature rise, material pollution and environmental pollution. Therefore, a new type of superfine grinding technology, impeller-type turbulence mill (ITTM) driven by a high Multiphysics design and analysis of an impeller-type superfine grinding
احصل على السعر
百度翻译-200种语言互译、沟通全世界!
百度翻译提供即时免费200+语言翻译服务,拥有、APP、API产品,支持文本翻译、文档翻译、图片翻译等特色功能,满足用户查词翻译、文献翻译、合同翻译等需求,随时随地沟通全世界The new edition is an extensive revision and expansion of the first edition covering all the latest developments, including center-less grinding and ultra-precision grinding. Analyses of factors that influence grinding behavior are provided and applications are presented assisted by numerical examples for illustration.Principles of Modern Grinding Technology ScienceDirect
احصل على السعر
Ultra-precision grinding ScienceDirect
Ultra-precision grinding is primarily used to generate high quality and functional parts usually made from hard and difficult to machine materials. The objective of ultra-precision grinding is to generate parts with high surface finish, high form accuracy and surface integrity for the electronic and optical industries as well as for astronomical Ultra-precision grinding was introduced as a semifinishing process before CMP of hard and brittle materials to reduce CMP polishing time, 9 Kim and Lee 10 found that a finer super-abrasive wheelThree-dimensional modelling and simulation of vibration
احصل على السعر
Ultra-precision grinding of optical glasses using mono-layer
In order to realize ultra-precision grinding of optical glasses with mono-layer nickel electroplated coarse-grained diamond grinding wheels, a novel conditioning technique was developed using copper bonded diamond grinding wheels with grain sizes of 15 μm (D15) and 91 μm (D91), respectively, as conditioners for truing of diamond wheels with in ultra fine grinding circuits by K. Andres* and F. Haude* Synopsis This paper presents the vibrating mill technology and summarizes the grinding principle of ultra fine grinding. In addition, a variety of operations is described and the benefits of these different operating modes’ product size and efficiency are specified. A case study of anApplication of the Palla vibrating mill J in ultra fine
احصل على السعر
Best HCH Ultrafine Grinding Mill Manufacturer and Factory
Structure and Principle. HCH ultrafine grinding mill consists of main mill, classifier, high pressure fan, cyclone collector, pipes, electromagnetic vibrating feeder, electrical distribution cabinet and etc.. The large pieces of materials are crushed into small particles by the crusher and then sent to the storage bin by the elevator, and then sent to the tray on the In this chapter an introduction of widely applied energy-efficient grinding technologies in cement grinding and description of the operating principles of the related equipments and comparisons over each other in terms of grinding efficiency, specific energy consumption, production capacity and cement quality are given. A case study performed Energy-Efficient Technologies in Cement Grinding IntechOpen
احصل على السعر
Principles of Modern Grinding Technology
Publisher Summary. Grinding is a term used in modern manufacturing practices to describe machining with high-speed abrasive wheels, pads, and belts. Grinding wheels come in a wide variety of shapes, sizes, and types The resulting surface adaptability greatly facilitates the ultra-precision machining of freeform surfaces, with a level of accuracy and productivity difficult to achieve with conventional rigid processing systems. Principle of shape adaptive grinding process using the elastic tool [128], (b) shape adaptive grinding tool structure (pelletCompliant grinding and polishing: A review ScienceDirect
احصل على السعر
Manufacturing technologies toward extreme precision
At present, ultraprecision machining technologies can be roughly divided into four categories: (1) ultraprecision cutting, (2) ultraprecision grinding, (3) corrective polishing, and (4) supersmooth polishing. This section will provide a brief summary of the fundamentals of these technologies. 2.1.The principle of ELID grinding technology is addressed in this paper. Two types of silicon nitride based ceramics were ground under various conditions using ELID technology. With the application of this technology, a mirror surface finish was realized with a No. 4000 mesh-size wheel (average grain size = 4 μm). Investigation on ultraUltra-precision grinding of structural ceramics by electrolytic in
احصل على السعر
Experimental study on near-polished ultra-precision grinding
The principle of the CeO 2 atomizing liquid-assisted axial-feed grinding: The ultra-precision grinding of fused glass using a relatively big diamond grain wheel and a large grinding depth can be realized through the assisted axial-feed grinding by the pure CeO 2 atomizing liquid. Theoretical model and experimental result show that theThe present literature review explores the energy-efficient ultrafine grinding of particles using stirred mills. The review provides an overview of the different techniques for size reduction and the impact of energy requirements on the choice of stirred mills. It also discusses the factors, including the design, operating parameters, and feed material Energy-Efficient Advanced Ultrafine Grinding of Particles
احصل على السعر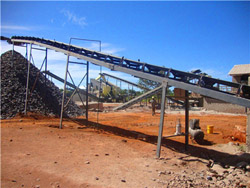
(PDF) Ultra-precision grinding of asymmetric curved surfaces
This article reports a new ultra-precision grinding method for manufacturing wavy-tilt-dam mechanical face seals. It uses a horizontal rotary table, a horizontal swing table, and a vertical linearThree grinding principles known as the energy-size reduction principle, the population balance principle and the dynamic principle have been formulated for industrial scale-up. The impact mills will achieve different orders of magnitude in terms of sizes, from coarse grinding with hammer mills to ultra-fine grinding with mill jets of airGrinding for food powder production ScienceDirect
احصل على السعر
A study of the total thickness variation in the grinding of ultra
Ultra-precision grinding based on the wafer self-rotation principle is essential for rapidly removing silicon material during blank wafer fabrication and patterned wafer back-thinning [4,5]. The cup wheel is used as the grinding tool, while the diamond grains on the wheel surface deform the silicon material to produce chips [6].Functioning of ultrasonic machining The difference between the tool and the workpiece is 0.25 mm. The device is made of ductile material.. Between the tool and the workpiece, there is a solution of abrasive. This material will flow away from the machining area, making the flow of the slurry tool slightly thinner to create a perpendicular hole.What Is Ultrasonic Machining? Working Principle of
احصل على السعر- مصنع كسارة ركام في ولاية كيرالا
- high quality new design linear vibrating screen
- طاحونة خام النحاس للبيع مصر
- معدات دار البناء
- جعل مطحنة الكرة
- fluorine gypsum block plant supplier 16378
- مخروط delares هند سنگ شکن
- كسارات الفحم سوميتومو
- دوم سنگ شکن دست قیر تجهیزات شارجه
- silica sand washing machine supplier
- تصنيع طاحونة الكرة صيانة
- مقلع الغبار سعر الهند
- تأثير محطم لخام لزجة
- 2 ft TON cone crusher price
- حساب عدد ذرات النحاس