اتصل
هاتف
+0086-371-86162511
عنوان
تشنغتشو ، الصين
cement grinding ball mill unit
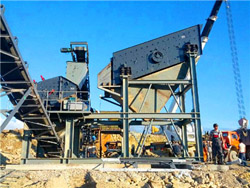
Cement Ball Mill Cement Grinding Machine
The cement ball mill is a kind of cement grinding mill. It is mainly used for grinding the clinker and raw materials of the cement plant, and also for grinding various ores in metallurgical, chemical, and electric power The proven classical option for cement grinding. Whether employed as a two-compartment separator mill in an independent grinding system, or in combination with a high pressure ball mill thyssenkrupp Polysius
احصل على السعر
Cement Factory Making Clinker Grinding Ball Mill Unit
Great adaptability enables the grinder to produce any fineness of particles in a short time Cement Factory Making Clinker Grinding Ball Mill Unit. 5. Advanced The comminution efficiency of a HPGR is better than ball mills such that it consumes 30–50 % of the specific energy as compared to a ball mill. Four circuit configurations of HPGR can be used in grinding of Energy-Efficient Technologies in Cement Grinding
احصل على السعر
Energy and exergy analyses for a cement ball mill of a new
Altan et al. [25] investigated the effect of both closed and open circuit on the pre-grinding performance of a cement ball mill (CBM) unit with a high pressure grinding Based on the orthogonal experimental design method, four influencing. Request PDF Energy and exergy analyses for a cement ball mill of a new generation Energy and exergy analyses for a cement ball mill of a new
احصل على السعر
Review on vertical roller mill in cement industry & its
A two-compartment ball mill with a highly efficient separator is still procured for new cement grinding units installation, although the vertical roller mill has now 【Product description】: Cement ball mill is mainly used in the grinding of finished products and raw materials in cement plants. 【Product capacity】:21-155 t/h 【Motor Power】: 800-3550 kw Cement Ball Mill CHAENG
احصل على السعر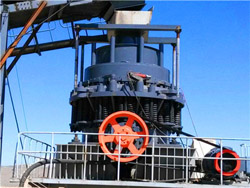
Effects of Mill Speed and Air Classifier Speed on
the two compartment Cement ball mill performance in terms of Blaine, Sulphur trioxide contents, mill power, mill residue and mill residence time. Within the content of this work, sampling campaigns were organized around a cement grinding circuit and varying cement ball mill speed as well as an air classifier speed at various dosage feed rate.In the cement industry, grinding is one of the most consuming energy stages in the production units. Around 65% of the total used electrical energy in a cement plant has to be utilized to grind raw Ventilation Prediction for an Industrial Cement
احصل على السعر
Optimization of an industrial scale open circuit three
An industrial scale FLSmidth® three-compartment cement grinding ball mill operating in open circuit was sampled at the steady state conditions. The three-compartment ball mill was modelled by using the perfect mixing modelling approach [1]. The electrical energy consumption of the CBM unit was specified to be 37.9 kWh/t. The effects ofNowadays, ball mills are used widely in cement plants to grind clinker and gypsum to produce cement. In this work, the energy and exergy analyses of a cement ball mill (CBM) were performed andEnergy and exergy analyses for a cement ball mill of a new
احصل على السعر
1 ASEAN GRINDING PROJECT KHD Humboldt Wedag
existing two ball mill circuits. KHD’s comflex grinding units are always engineered around a roller press as core grinding mill in close circuit with static and dynamic separators. Figure 1 and the equipment overview in Table 1 outline the new raw material grinding circuit in finish mode and the equipment chosen by SCCC and KHD.The KMCC cement grinding system consists of a closed circuit ball mill, and it was supplied in 2006 by KHD Humboldt Wedag Company for guaranteed cement production of 210 t/h (ton/hour). The clinker grinding unit mainly consists of a ball mill and a dynamic separator that their technical information is illustrated in Table 1 .Energy and exergy analyses for a cement ball mill of a new
احصل على السعر
Cement grinding optimisation ScienceDirect
The efficiency of fine grinding in the second compartment is largely controlled by the size of grinding balls. Due to limitation of the mill’s rotational speed, the smallest ball size is usually restricted to about 15 mm. Cement grinding using stirred mills (Pilevneli and Azizli, 1999) indicates that using smaller media (5–8 mm range1. Introduction. In the cement industry, grinding is one of the most consuming energy stages in the production units. Around 65% of the total used electrical energy in a cement plant has to be utilized to grind raw materials, coal, and clinker [1,2].Through the process, many variables can affect the efficiency and productivity of Ventilation Prediction for an Industrial Cement Raw Ball Mill
احصل على السعر
Analysis of the efficiency of the process in closed circuit
– the grinding of clinker size of less than 2 mm increases the grinding efficiency in ball mill; in connection with increasing the amount of comminuted material passing through the drum of the ball mill, reduces the wear on the grinding bodies and lining per unit finished product; reduced power of ball mill of the second stage.1. Introduction. World cement production is about 4.2 billion tons in 2019 and cement plants consume about 2 percent of world electrical energy in the grinding process [1], [2].The total electrical energy that is consumed in cement companies is about 100 kWh per 1000 kg of cement, and two-third of this amount just consumes in raw A case study on energy and exergy analyses for an industrial
احصل على السعر
MAAG® GEAR CPU Gear Unit FLSmidth
With a long history of reliability and performance, our MAAG® GEAR CPU Gear Unit delivers optimum power transmission as part of a robust, long-term grinding solution for ball mills. Our modern manufacturing methods and tooling machines enable us to deliver state-of-the-art gear units. This two-stage planetary gear offers an impressive serviceSteel balls are one of the most widely used grinding media in cement ball mills, their diameters can range from 20mm to 120mm according to different grinding requirements. In a cement ball mill, How to choose proper grinding media for your
احصل على السعر
A comparative analysis of steel and alumina balls in fine
In modern cement milling plants, ball mill is not solely operated but is usually coupled with a hydraulic roller press (HRP) [11, 12], with the latter acting as a pre-milling unit. A combined ball mill-HRP circuit results in lower total specific power consumption [13, 14]. Briefly, HRP consists of two rollers with one roller being movable.Clinker grinding technology is the most energy-intensive process in cement manufacturing. Traditionally, it was treated as "low on technology" and "high on energy" as grinding circuits use more than 60 per cent of total energy consumed and account for most of the manufacturing cost. Since the increasing energy cost started burning the benefits Clinker grinding technology in cement manufacturing
احصل على السعر
Latest trends in modular cement grinding plants Cement
The ball mill has a 1100 kW drive and achieves 30 t/h CEM I cement with 3200 cm 2 /g Blaine. The largest “Plug & Grind” is the Extreme, which is for a throughput of up to 0.39 Mt/a. It uses a ball mill 3.2 m in diameter, 11.5 m in length and with 1600 kW installed power, which produces up to 50 t/h CEM I (3200 cm 2 /g Blaine).\n \n technical feasibility of a grinding project samatour.fr \n. Feasibility Study for capacity up gradation of Magdalla Grinding Unit by either installation of Roll Press with the existing Ball Mill System or by installation of one VRM shifted from Wanakbori Cement Works and increase the bulk loading capacity from 0.2 mtpa to 0.8 mtpamercial feasibility of cement grinding unit feasibility report
احصل على السعر
Process Training Ball Mill INFINITY FOR CEMENT EQUIPMENT
The better mills on the market have an efficiency of about 8-9 % which means that only 8-9 % of the energy results in grinding and the majority is converted mainly into heat. The ball mill has the worst efficiency of all types of mills on the market. Just 4 % of the energy is used for comminution. Nevertheless when grinding is required the ballAGICO Cement is a cement equipment manufacturer with more than 20 years’ experience. We are the long-term partner of many large and medium-sized cement enterprises in different countries, providing cement equipment and EPC project construction. The closed-circuit grinding system ball mill for cement grinding and the matching powderBall Mill In Cement Plant Cement Ball Mill AGICO Cement
احصل على السعر
(PDF) Analysis of the efficiency of the grinding process in
Abstract. Ball mills for fine grinding cement clinker and additives are widely used around the world. To improve the efficiency of a ball grinding the ball mills are transferred in closed circuit
احصل على السعر- الكوارتز آلة طحن الهند
- استبيان لمصنع كسارة الحجارة
- مصنعي مطحنة الكرة في beawar mdorg
- jaw crushers and stone crushing plant
- آلة تحطيم الحجر في الجزائر
- كسارة الحجر خام محطم
- معدات لإنتاج الركام والخرسانة
- bentonite crusher machines
- مسحوق الألمنيوم لمطحنة الكرة
- ماكينة تضريب الالوان الكمبيوتر للحوائط
- إعادة تدوير كسارة الحجر معالجة المعادن
- supply professional cenment raymond mill equipment
- ذاتي المنشأ مصنع طحن
- اثنين من مطحنة الكرة Mpartmnt
- بيع قدرة مخروط محطم