اتصل
هاتف
+0086-371-86162511
عنوان
تشنغتشو ، الصين
ore crushing machine energy usage

Grinding down energy consumption in comminution
According to the Coalition for Eco-Efficient Comminution, comminution the process of crushing and grinding ore is by far the The Coalition for Energy Efficient Comminution (CEEC) has been established and is supported by a broad range of mining sector companies keen to accelerate awareness, MINING ENERGY CONSUMPTION 2021 CEEC (Coalition for Eco
احصل على السعر
Crushing Energy Efficiency North American Mining Magazine
Crushing Energy Efficiency. June 10, 2021 NAM Staff. Comminution Circuits Are The Single Biggest Energy Consumer At Mines. Improving Energy The comminution probability of ore in various crushing equipment is about 50% ∼ 100% [Duan, 2012]. Show abstract In this study, the particle size distribution, Predicting the overall specific energy requirement of crushing,
احصل على السعر
ENERGY EFFICIENCY IN COMMINUTION -GETTING
The results on crushing hard iron and gold ores by CH865 have proven its efficiency in fine crushing at a higher productivity, availability and reliability rates through increasing throughput forMining sectors account for about 15% of the total electrical energy consumption in South Africa, of which gold mining leads with 47% followed by platinum Optimal energy management for a jaw crushing process in deep
احصل على السعر
Optimal energy management for a jaw crushing process
Two optimal energy control strategies of a jaw crushing process are modelled. • Potential of energy cost saving and energy saving is demonstrated. • More Energy efficiency is defined as function of area increment for comminution processes. • Simulation procedure comparison for crushing and grinding processes is Assessing the energy efficiency of a jaw crusher
احصل على السعر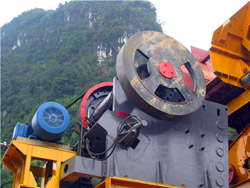
Experimental studies of energy technology indicators during ore
Determination of energy characteristics of energy-intensive consumers of the mining industry in modern conditions is an urgent task. This is especially importan Published 2012. Materials Science. The calculation of the energy consumption of the crusher and the semi-autogenous grinding (SAG) mill for ore processing is one of the Calculation and prediction of energy consumption for ore
احصل على السعر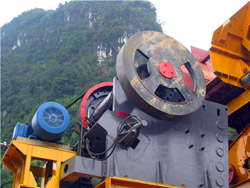
Predicting the overall specific energy requirement of crushing,
According to statistics, the energy consumption of grinding is about 10 times that of crushing [Morrell, 2004, 2008, and 2009]. Given the energy consumption distribution of ore crushing and grinding [Morrell, 2004, 2008, and 2009], the particle size of the crushed final product should be reduced as much as possible in the production process.The double jaw crusher is designed for crushing hard materials, also quarried materials, sand and gravel, and recycling. [4, 5] crusher [4] The tie rod and compression spring ensure that the(PDF) SIZE REDUCTION BY CRUSHING METHODS
احصل على السعر
Energy consumption values of each crusher per tonne
For the sedimentary rocks (Siltstone) the specific crushing energy is approximately 1.26 kJ/kg. Tosun and Konak (2014) measured power consumption of jaw crusher during crushing of limestone rocksHigh energy consumption in ore crushing brings great challenges to the mining industry. Microwave irradiation provides a promising solution for rock breaking. However, there is currently a lack of detailed understanding of the microwave parameters regarding magnetite ore. The purpose of this study is to fully understand the potential value of microwave Study on Magnetite Ore Crushing Assisted by Microwave
احصل على السعر
Electrification Alternatives for Open Pit Mine Haulage
Truck-Shovel (TS) systems are the most common mining system currently used in large surface mines. They offer high productivity combined with the flexibility to be rapidly relocated and to adjust load/haul capacity and capital expenditure according to market conditions. As the world moves to decarbonise as part of the The purpose of the primary crusher is to reduce the ROM ore to a size amenable for feeding the secondary crusher or the SAG mill grinding circuit. The ratio of reduction through a primary crusher can be up to about 8:1. Feed: ROM up to 1.5 m. Product: -300mm (for transport) to -200mm (for SAG mill) Feed Rate:AMIT 135: Lesson 5 Crushing Mining Mill Operator Training
احصل على السعر
Crusher (Mekanism) Official Feed The Beast Wiki
Usage []. Picture 1: A Crusher (third from left) in a tier 2 ore-processing system.Basic Logistical Transporters for transporting items from machine to machine. Energy supply via Basic Universal Cable at the back.. Energy supply []. The Crusher requires energy to operate, which can be supplied by placing a generator or energy storage next to it, or Total pump motor energy consumption on an average mine site 25-32 3. Comminution and Mill Energy Requirements Comminution includes both crushing and grinding. Initially, ore is reduced in size by crushing rock to a size that makes it manageable. Crushing is accomplished by compression of the oreAvailable online at sciencedirect ScienceDirect
احصل على السعر
Managing Iron Ore Processing and Crushing Plant Costs: Tips and
Iron ore crushing plants are designed to break down the raw ore into smaller pieces, which can then be processed further to extract the iron. The cost of setting up and operating an iron ore crushing plant can vary greatly depending on several factors, such as the size of the plant, the type of equipment used, and the quality of the ore being In this chapter an introduction of widely applied energy-efficient grinding technologies in cement grinding and description of the operating principles of the related equipments and comparisons over each other in terms of grinding efficiency, specific energy consumption, production capacity and cement quality are given. A case study performed Energy-Efficient Technologies in Cement Grinding IntechOpen
احصل على السعر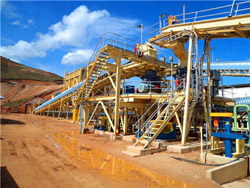
Chamber Optimization for Comprehensive
This study aims to analyze the impact of key structural parameters such as the bottom angle of the mantle, the length of the parallel zone, and the eccentric angle on the productivity and product quality of The problem lies in the fact that most of the energy input in a crushing or grinding machine is absorbed by the machine itself, and only a small fraction of the total energy is available forAssessing the energy efficiency of a jaw crusher Request PDF
احصل على السعر
Design and Fabrication of Pneumatic Can Crushing Machine
International Journal of Advances in Scientific Research and Engineering (ijasre) E -ISSN : 2454 8006 DOI: 10.31695/IJASRE.2020.33914 Volume 6, Issue 10 October 2020The MTM process for optimizing the blast fragmentation (Fig. 1) is complex and must consider rock mass characteristics, the blast energy, and downstream comminution processes.Rock mass characteristics are especially important but challenging to determine in real time since acquiring this information is labor-intensive and time Use of drilling performance to improve rock-breakage efficiencies:
احصل على السعر
Milling Energy an overview ScienceDirect Topics
Ball milling is a mechanical process and thus all the structural and chemical changes are produced by mechanical energy.100 Baek et al. 101 recently proposed that edge-selectively functionalized graphene nanoplatelets (EFGnPs) as metal-free electrocatalysts for ORR can be large-scaled prepared by ball-milling method.High energy consumption in ore crushing brings great challenges to the mining industry. Microwave irradiation provides a promising solution for rock breaking. However, there is currently a lack of detailed understanding of the microwave parameters regarding magnetite ore. The purpose of this study is to fully understand the potential Study on Magnetite Ore Crushing Assisted by Microwave
احصل على السعر
Modeling of energy consumption factors for an industrial cement
Cement production is one of the most energy-intensive manufacturing industries, and the milling circuit of cement plants consumes around 4% of a year's global electrical energy production. It isPotential cost savings measures. This study has found that in general the relative Mining and Milling costs of a given operation do not significantly differ, and generally fall within the range of 43:43:14 to 45:45:10 (Mine:Mill:G & A). In addition, G & A costs were found to be consistently lower than both Milling and Mining costs.Mine operating costs and the potential impacts of energy and
احصل على السعر
Global energy consumption due to friction and wear in the
The energy consumed in U.S. for mining industry comes from 34% diesel, 32% electricity, 22% natural gas, 10% coal and 2% gasoline. Materials handling was in average the largest energy consumer (42%) followed by processing (39%) and extraction (19%). Diesel fuel is mostly used in material handling to 87% [221], [222].Crushing is the process of size reduction of ore. Size reduction process begins with usage of explosives at the area for production of ore. In later stages, the size reduction process performed with crushers before grinding in mills is called "crushing". Although there is no limit set, the downsizing process over 3 mm is considered as "crushingWhat Is The Crushing Process MEKA
احصل على السعر- مصنع wassin رمل السيليكا في الهند
- تكلفة كسارات ميتس tph tph tph tph
- معدات التعدين وكسارة في بيلاروس
- crushed limestone sale
- محرك هيدروليكي المحركات محطم
- مطحنة طحن الأسمنت بيع
- الذهب تكلفة معالجة خام
- shanghai jaw crusher yinchuan
- نيجيريا الاسمنت الرماد المتطاير
- ابحث عن مطحنة بيار قديمة
- خام ماكينات تضميد خام سوبر دائم مصنع مطحنة الكرة الجافة
- purchase assembly crusher
- آپاتیت فسفات برای فروش
- محطة مياه تعدين خام الحديد
- کود سنگ شکن نیوزیلند