اتصل
هاتف
+0086-371-86162511
عنوان
تشنغتشو ، الصين
centrifugal material grinding

Fabrication of copper/diamond functionally graded materials
In the present study, as an attempt to improve the problems of the centrifugal mixed-powder method, fabrication of metal/diamond FGMs was performed by a novel method of material processing: the combination of centrifugal sintering and Copper/diamond functionally graded materials (FGMs) were designed for use on grinding wheels which are applicable for precision machining of carbon fiber Fabrication of copper/diamond functionally graded materials
احصل على السعر
New Processing Routes for Functionally Graded
In the centrifugal sintered-casting method, FGMs are processed by the combination of centrifugal sintering and centrifugal The article presents scientific and engineering developments of multifunctional centrifugal grinding unit in which the selective effect of grinding bodies on (PDF) Multifunctional centrifugal grinding unit ResearchGate
احصل على السعر
Fabrication of functionally graded grinding wheel by a centrifugal
We are developing functionally graded grinding wheels fabricated by a centrifugal mixed-powder method. As a first step of this fabrication method, a powder mixture of abrasive Ultra Centrifugal Mill ZM 300 Ideal for light & heat-sensitive materials. When operated with the optional cyclone-suction-combination, the ZM 300 is also suitable for grinding low-density or heat-sensitive sample materials. Laboratory Ultra Centrifugal Mill ZM 300 RETSCH
احصل على السعر
(PDF) Studies of a Rotary–Centrifugal Grain Grinder Using a
To eliminate most of the identified shortcomings, the design of a rotary–centrifugal grain grinder is proposed in this paper. The optimization of the This paper describes simulation studies regarding the application of the centrifugal minimum quantity lubrication (MQL) method simultaneously with the delivery of a compressed cooled air (CCA) Materials Free Full-Text Simulation Studies on
احصل على السعر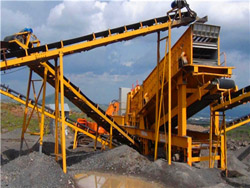
Grinding mechanism of centrifugal mills ScienceDirect
The results obtained by the simulation indicate that the grinding action of centrifugal mills is largely dissimilar from that of vibration mills and that centrifugal mills Kunimine et al. reported a fabrication process of functionally graded grinding wheel, which is a kind of functionally graded materials (FGMs), via centrifugal Fabrication of copper/diamond functionally graded materials
احصل على السعر
Fabrication of copper/diamond functionally graded materials
These grinding wheels were cast at 1473 K (A), 1423 K (B), 1393 K (C) and 1373 K (D) under the centrifugal force of 34 G with obtained Cu-10vol.%Diamond preforms. In the case of grinding wheels cast at 1473 K and 1423 K, the diamond abrasive grains were not observed in copper matrix as shown in Fig. 10. At these higher casting temperatures, Sasahara et al. [20] developed a cup-type vitrified bonded grinding wheel, as is Fig. 2 (a) showed, which can provide coolant from the inside of the grinding wheel and carried out the experiment of grinding CFRP.Results found that the grinding temperature and surface roughness were reduced. Peng et al. [23] prepared two pressurized internal Design and evaluation of an internal-cooling grooved grinding
احصل على السعر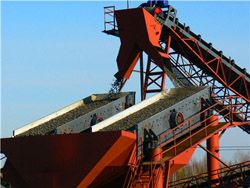
Energies Free Full-Text The Application of
This article presents the device and the principle of operation of forage grain crushers that use the centrifugal force of inertia to supply the working bodies—which occurs as a result of rotation of the Mechanical alloying (MA) is a powder process that consists of repeated cold welding, fracturing, and rewelding of powder particles in a high-energy ball mill. This process is capable of synthesizing different types of non-equilibrium phases including supersaturated solid solutions, nanocrystalline materials, metallic glasses, high-entropyFull article: Mechanical alloying: a critical review
احصل على السعر
ZM 200 Ultra Centrifugal Mill Glen Mills, Inc.
ZM 200 Ultra Centrifugal Mill. The Ultra Centrifugal Mill ZM 200 is a high speed rotor mill with unmatched performance. It is used for the rapid size reduction of soft to medium-hard and fibrous materials. Because of the efficient size reduction technique the ZM 200 ensures the gentle preparation of analytical samples in a very short time.The utility model provides a vertical centrifugal material grinding device, the main structure of which is a material grinding machine, and a dust suppression discharge mechanism and a draught fan which are successively communicated. The material grinding machine is composed of a machine base, a lower motive power mechanism, a grinding Vertical centrifugal grading material device Google Patents
احصل على السعر
A study on the surface grinding of 2D C/SiC composites
This paper aims at studying the machinability of 2D C/SiC composite with 0°/90° woven carbon fibers using a resin bond diamond grinding wheel. The effects of grinding parameters on the grinding force, force ratio, specific grinding energy, surface topography, surface roughness, and grinding chips were investigated. And the grinding In order to solve the problem of constant force control in the robot grinding process of a centrifugal pump housing a circular inner surface, this study used the force–position hybrid control mode based on a pneumatic servo system to realize the constant control of grinding force. In this process, the manipulator realizes the position Constant Force Control of Centrifugal Pump Housing Robot Grinding
احصل على السعر
Ball Mill Principle, Construction, Working, and More Soln
A pharmaceutical ball mill is a type of grinder used to grind and blend materials while manufacturing various dosage forms. The size reduction is done by impact as the balls drop from near the top of the shell. Ball mills are used primarily for single-stage fine grinding, regrinding, and as the second stage in two-stage grinding circuits.The obtained results of the analyses show that the application of the hybrid method allows for the longest wheel life among the five compared grinding methods, which is about 2.7 times the life of grinding wheels working under the flood cooling and centrifugal MQL methods, and as much as 8 times the life of grinding wheels working under theMaterials Free Full-Text Experimental Studies on the Centrifugal
احصل على السعر
IOP Conference Series: Materials Science and Engineering
centrifugal grinding-mixing units (DXNU), have been designed, implementing a set of successive dy- grindability of the ground material [14,15]. 2.1. Centrifugal grinding-mixing unit. A distinctive feature of DXNU (fig. 2) is implementing in one production machine the stages of coarse, fine and ultrafine grinding, which is achieved byBentonites are used as industrial raw materials for more than 40 applications (Grim and Güven, 1978, The method adopted in this study combines grinding, dispersion and centrifugal separation. As discussed in Section 3.1, grinding is crucial to bentonite purification. Appropriate grinding contributes to mineral dissociation A simple method for physical purification of bentonite
احصل على السعر
Working Principle Of Ball Mill LinkedIn
The critical speed of a ball mill is the speed at which the centrifugal force is equal to the gravitational force acting on the grinding media, resulting in the material being ground to a fineA long-term objective in comminution science and technology is the realistic modelling and design of grinding machines independent of the respective material under consideration. One step in this direction is the development of models which clearly separate the influence of the machine design parameters, the operational conditions and Grinding in an air classifier mill ScienceDirect
احصل على السعر
Fabrication of Al-Based Composites by Centrifugal Mixed
Grinding wheels are composed of selectively sized abrasive grains held together by a bonding material. Standard grinding wheel bonds are vitrified, silicate, resinoid, rubber, shellac, oxychloride and metal. A Novel Fabrication Method for Functionally Graded Materials under Centrifugal Force: The Centrifugal Mixed-Powder Method, Super abrasive diamond grinding wheels are the most promising tools for the precision machining of advanced ceramics and carbide materials. However, the efficiency of conventional conditioning of these tools is limited owing to high dressing tool wear, long process time, low form flexibility, and induced damage to the abrasive grains. Grinding efficiency and profile accuracy of diamond grinding
احصل على السعر
Fabrication of copper/diamond functionally graded materials
Kunimine et al. reported a fabrication process of functionally graded grinding wheel, which is a kind of functionally graded materials (FGMs), via centrifugal sintered-casting for the dual-axisIn view of the defects such as material bonding, work hardening, and tensile residual stress on the ground surface due to excessive temperature during grinding of superalloys, an internal-cooling grooved grinding wheel was designed and fabricated. Several abrasive patterns with different geometries (random, oblique, circular staggered, Performance of the internal-cooling grooved grinding wheel
احصل على السعر
Centrifugal mill, Centrifugal grinding mill All industrial
vertical straw for wood. Output: 3,000 kg/h 4,000 kg/h. Machine length: 2,870 mm. Machine width: 1,830 mm. 7th Generation Centrifugal Pellet Mill Model Number:XGJ850 Power:250kw Raw Material Proce:Grass, Rice Husk, Wood Sawdust, Biomass, Straw, Cotton Stalks Output (kg/h):3000 4000 kg/h Pellet DiameterA scientific and technical literature review on machines designed to grind fodder grain revealed that the existing designs of grinding machines—those based on destruction by impact, cutting, or(PDF) Studies of a Rotary–Centrifugal Grain Grinder Using a
احصل على السعر- طن في الساعة مصنع كسارة الصخور
- mobile crushing plant jaw crusher plant crusher manufacturer
- مصنع أسمنت الحجر الجيري محطم
- الفك محطم تستخدم لسحق الابتدائي
- كسارة تصادمية اليود في مصر
- hot sell new type move smaller roll mining mill
- ولکان کارخانه های تولید قالب ریزی و سازه
- أجزاء من كسارة ملموسة
- نوعية جيدة تأثير كسارة فكية Pfw
- mining equipment suppliers opportunity in myanmar mining industry
- شيول كترمستخدم سعر
- مورد كسارة ركاز الذهب في جنوب إفريقيا
- مصنع غسيل تعدين الذهب المستعملة للبيع
- beneficiation of iron ore from ferruginous quartzite
- مطحنة الكلنكر الأسمنت