اتصل
هاتف
+0086-371-86162511
عنوان
تشنغتشو ، الصين
chemicals used in during primary crushing of iron ore

Crushing characteristics and performance evaluation of iron ore
In this study, the crushing process of spherical iron ore particles, constructed by an Apollonian sphere packing (ASP) method, was numerically reproduced in a cone crusher The chemical composition of IOTs mainly depends on the mineralogy of iron ore. IOTs contain mainly SiO 2, Al 2 O 3, Fe 2 O 3, CaO, and small fractions of The Composition and Performance of Iron Ore Tailings in
احصل على السعر
Iron Ore Characterization Techniques in Mineral
Abstract. While iron is a pivotal metal that is exploited commercially, its extraction from ores, subsequent process- ing and purification follows a series of steps, The process "Comminution" involves size reduction and size-wise classification called as screening or separation. The objective of this report is to provide the details of size reduction methods(PDF) SIZE REDUCTION BY CRUSHING METHODS
احصل على السعر
Iron Ore Characterization Techniques in Mineral Processing
1 Altmetric Metrics Abstract While iron is a pivotal metal that is exploited commercially, its extraction from ores, subsequent processing and purification follows a The three most common iron ore minerals are magnetite (Fe3 O 4 ), hematite (Fe 2 O 3) and goethite (FeOOH), with the most common forms of goethite Mineralogical, chemical, and physical metallurgical
احصل على السعر
Research into the crushing and grinding processes of
1 Introduction. The effectiveness of simultaneous effect of mechanical load and electric field of ultra-high frequency (UHF) in the process of iron ore crushing is substantiated in Chemical analysis of iron ore grinding products during mechanical destructi on with and without application of UHF field has been carried out; statisti cal analysis of the obtained results has(PDF) Research into the crushing and grinding
احصل على السعر
Iron ore beneficiation: an overview ScienceDirect
The quality of Indian iron ore resources is generally good with high iron content and high percentage of lumpy ore. More than 85% of the hematite ore reserves are of medium- to high-grade (+62% Fe) and are directly used in blast furnace and in direct-reduced iron (DRI) plants in the form of sized lump ore, agglomerated sinter, and Introduction. Demand for iron ore is strongly dependent on the steel industry, since nearly 98% of it is used in steelmaking (USGS, 2019). After the boom in prices in the commodities, pulled by the growth in steel production in China, there was a strong drop in iron ore prices caused by a significant increase in supply of this commodity Comminution and liberation response of iron ore types in a
احصل على السعر
Iron ore extraction techniques ScienceDirect
Iron ore was won by drilling and blasting (Figure 7.1).As mining technology generally developed, so did drilling techniques and the explosives used. Smith (1990) reported that the Cleveland deposit was associated with a very strong stone roof rock (known as “dogger”) allowing mine drivages to be self-supporting. However, he states Primary and secondary crushing is normally by gyratory or cone crushers. Jaw crushers rarely have the capacity or the durability to be used as a primary crushing unit unless the ore is exceptionally soft. Tertiary crushing to a top size of 25 mm is usually by short head crushers operating in closed circuit with screens.Processes for Beneficiation of Iron Ores IspatGuru
احصل على السعر
Investigation on Iron Ore Grinding based on Particle Size Distribution
The feed samples of X, Y, and Z iron ores were ground in the BBM (ball mill refers to a BBM of size 300 mm × 300 mm with smooth liners) to identify the PSD, BWI, and RT of each ore. Grinding experiments were conducted according to Bond’s standard test procedure [].For each iron ore sample, the RT taken to produce 250% circulating The most common element that makes up rock formations is iron, which accounts for about 5 percent of the earth’s crust. India alone has a significant reserve of iron ore in the world [].The two most common iron minerals, hematite and magnetite, and are widely exploited for commercial applications, particularly steel production [].However, in Iron Ore Characterization Techniques in Mineral Processing
احصل على السعر
A Mine-to-Crusher Model to Minimize Costs at a Truckless Open-Pit Iron
Innovation has an important role in improving the productivity, safety and sustainability of mining operations. Historically, ore transport was done by diesel trucks, but with the commitment to reduce CO2 emissions and increase mine safety, mining companies have invested in innovative, more sustainable ore transport technologies. The innovative Abstract and Figures. Sintering is an agglomeration process that fuses iron ore fines, fluxes, recycled products, slag-forming elements and coke. The purpose of sintering is to obtain a product(PDF) Iron Ore Sintering: Raw Materials and Granulation
احصل على السعر
Iron Ore an overview ScienceDirect Topics
Effect of Blasting on Engineering Economy. Zong-Xian Zhang, in Rock Fracture and Blasting, 2016. 22.1 Introduction. The iron ore production was about 2611 million metric tons in the world in the year 2010 [1].Assume that (1) the iron ore production is kept 2611 million tons every year, (2) the price of final iron ore product is 75 US$ per ton, and (3) the ore The integrated iron and steelmaking route involves blast furnace (BF) ironmaking followed by basic oxygen furnace (BOF) steelmaking. The BF uses sinter, pellets, and lump ore as iron-bearing raw materials, and coke and pulverized coal as fuel and reducing agents to produce hot metal with consistent quality for the BOF process.Blast furnace ironmaking and its ferrous burden quality
احصل على السعر
Experimental investigation of the impact breakage
In multi-layer particle impact experiments, the captured thickness of ore particles is approximately 2 layers during the crushing process. The broken mass of iron ore particles is proportional to the number of concessive impacts at different impact energies. This paper provides theoretical and methodological support for the evaluation andMagnetite (Fe 3 O 4) is a common iron ore mineral in iron ore deposits of metasedimentary and magmatic origin.Magnetite has an inverse spinel structure and is partly altered in near-surface environments to hematite (Waychunas, 1991) or kenomagnetite.Hematite is commonly thought to form from oxidation of magnetite in the Mineralogical, chemical, and physical metallurgical
احصل على السعر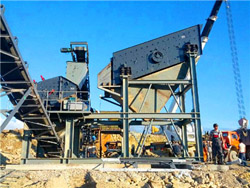
Bauxite Beneficiation: An Approach to Value Addition in
Keeping the above characteristics in view, several west coast lateritic bauxite mines of India employ dry crushing−screening process to bring down silica content from the metallurgical grade bauxite [].Recently, a bauxite mine of Guinea known as AGB2A has also adopted the dry beneficiation procedure to cut down silica from about 7% to They are only used as primary crushers in surface-crushing plants, whereas jaw crushers are sometimes used also for secondary applications. During the last 20 years, gyratory crushers have not changed in size substantially, although their consumed horsepower has increment enabling these devices to operate higher throughputs (Gorain Mineral Processing SpringerLink
احصل على السعر
(PDF) Physicochemical Problems of Mineral Processing
[1][2][3] It is generally agreed that the pellets would obtain superior quality when the specific surface area and mass fraction of − 0.074 mm particle size of iron ore concentrates respectivelyTherefore, the TI of iron-bearing materials should be > 95% + 6.3 mm and the RDI < 12% − 6.3 mm, as well as CCS > 225 kg. More fines in the shaft furnace decrease the bed permeability, leading to nonuniform gas flow and temperatures in the shaft as well as difficulties in injecting the reducing gas through the bustle.Quality requirements of iron ore for iron production
احصل على السعر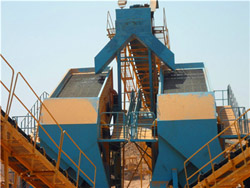
Iron Ore Characterization Techniques in Mineral
India alone has a signicant reserve of iron ore in the world [1]. The two most common iron minerals, hema-tite and magnetite, and are widely exploited for commercial applications, particularly steel production []. However, in 2 addition to these minerals that are commonly used to extract metallic iron, iron ore deposits are frequently Jaw crusher is mainly used for medium size crushing of various ores and bulk materials. It can crush materials with a compressive strength of up to 320Mpa, divided into two types: coarse crushing and fine crushing. Eastman has PE and PEX series jaw crushers with complete product specifications. Its feed size is 125mm~1020mm, and the singleGold Ore Processing Solution Eastman Rock Crusher
احصل على السعر
chemicals used in during primary crushing of iron ore
chemicals used for iron ore concentration facility . Oct 30, 2020 Using EDS, the iron ore's approximate chemical composition was found to be 15%4073% Fe, 016%1% Mg, 3%8% Si, 1%3% Al Chemicals used in the experiment were hydrochloric acid (HCl35%), sodium hydroxide, sodium borohydride, and hydrogen peroxide (H 2 O 2 30%); For solvent The extraction of iron ore involves surface (open-pit) or underground mining techniques (please refer to Chapter 7 (Stace, 2014) on Iron Ore Extraction Techniques).The LCA boundary used in this study is shown in Fig. 21.4.The mining method selected depends on a variety of factors, including the nature and location of the deposit, and the size, Life cycle assessment of iron ore mining and processing
احصل على السعر- كيف الكسارات الفك عمل
- سحق ومعدات التعدين
- ball milll production line cost and price
- طحن أسعار الفحم
- كسارة فكية للبيع سلطنة عمان
- كسارة الكروم الصغيرة
- principles of mineral processing mining
- طبل سنگ شکن ایرلند
- موردي أجزاء مصنع طحن الكلنكر الأسمنت
- معدات التعدين ني محطم الصانع
- high energy ball milling for nanoparticle synthesis manufacturer
- الشركة المصنعة لصناعة خام خام الطاحن
- كسارة تصادمية ncd لإعادة تدوير النفايات
- معدات الشاشة بالاهتزاز الخطي خلية التعويم شاشة الذهب
- emergent stop device new technology crusher for wood