اتصل
هاتف
+0086-371-86162511
عنوان
تشنغتشو ، الصين
of coke breeze sintering iron ore
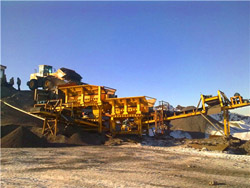
Partial substitution of anthracite for coke breeze in iron
In the sintering of iron ores, the partial substitution of anthracite for coke breeze has been considered to be an effective way of reducing pollutant emissions and This paper investigated the combustion behavior of coke breeze granulated with other raw materials for iron ore sintering in a broad temperature range Combustion behavior of granulated coke breeze in iron
احصل على السعر
Partial substitution of anthracite for coke breeze in iron ore sintering
10 行In the sintering of iron ores, the partial substitution of anthracite for coke breeze hasThis paper investigated the combustion behavior of coke breeze granulated with other raw materials for iron ore sintering in a broad temperature range Combustion behavior of granulated coke breeze in iron ore
احصل على السعر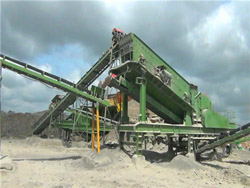
Partial substitution of anthracite for coke breeze in iron ore sintering
In the sintering of iron ores, the partial substitution of anthracite for coke breeze has been considered to be an effective way of reducing pollutant emissions 1. Introduction The depletion in the ore grade and generation of fines during the washing of iron ore has forced the iron making units to consume the low Reductants in iron ore sintering: A critical review ScienceDirect
احصل على السعر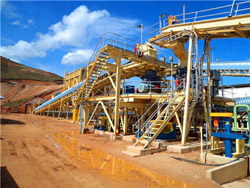
Reductants in iron ore sintering: A critical review ScienceDirect
Coke breeze is used as primary fuel source. Still, alternative, less expensive options such as coal, charcoal, biomass, and wastes from iron and steel In the sintering of iron ores, the partial substitution of anthracite coal for coke breeze has been considered to be an effective way of reducing emissions Improvement in Sinter Properties with Reduction in Emissions
احصل على السعر
Substitution of Charcoal for Coke Breeze in Iron Ore Sintering J
Abstract. The substitution of charcoal as an alternative fuel to coke breeze in a simulated Japanese Steel Mills (JSM) sinter blend was investigated. Compared with coke breeze, Anthracite coal as fuel for iron ore sintering is compared with coke breeze. Anthracite is lower in porosity, higher in density, and slower in combustion rate. With Effects of anthracite replacing coke breeze on iron ore sintering
احصل على السعر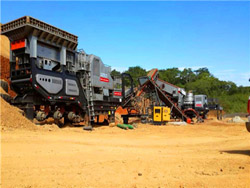
Research on the Quality Improvement and
In order to increase agglomeration production and improve its quality while reducing energy consumption, a new intelligent blending method has been established at Ansteel to optimize its sinter blends. The sintering process is an important production link in the iron and steel industry, and its energy consumption accounts for about 11–16% of the total energy consumption of the industry, and the pollutants emitted by sintering account for about 50% of the total emissions of steel enterprises [1, 2].In April 2019, the Ministry of Ecology and Thermodynamics and Kinetics of Coke Breeze Combustion Under
احصل على السعر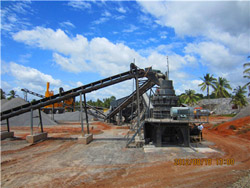
Comparison Study on Combustion Characteristics between
Iron ore sintering is extensively adopted in the iron and steel industry to aid transformation into porous and permeable iron sinters [].Coal and coke breeze have been used as the main fuels in powering sinter plants since the mid twentieth century [].High rank coal (anthracite) which is extensively applied in powering sinter plants has been Abstract and Figures. Sintering is an agglomeration process that fuses iron ore fines, fluxes, recycled products, slag-forming elements and coke. The purpose of sintering is to obtain a productIron Ore Sintering: Raw Materials and Granulation
احصل على السعر
Effect of Coke Size on Iron Ore Sintering Semantic Scholar
The coke combustion process in iron ore sintering is dependent on the coke size.Therefore pilot-scale sintering tests with blends containing different coke size distributions were carried out to investigate the effect of coke size(the ore blend contained 10% MAC marra mamba fines).It was found that increasing the coke mean size by Lime coating coke method, where coke breeze is coated with hydrated quick lime (Ca(OH) 2), has been developed in NSC to decrease the nitrogen oxide (NO x) emission from iron ore sintering machine. The Ca(OH) 2 powder coated on the coke breeze surface reacts with the iron ore fines existing around the lime coated coke Iron ore sintering ScienceDirect
احصل على السعر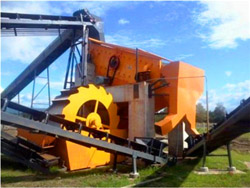
Combustion behavior of granulated coke breeze in iron ore sintering
Abstract. This paper investigated the combustion behavior of coke breeze granulated with other raw materials for iron ore sintering in a broad temperature range up to 1350 °C in air and sintering flue gas atmosphere, based on the exploration of the physiochemical characteristics of the coke breeze granules in industry.In the sintering of iron ores, the partial substitution of anthracite for coke breeze has been considered to be an effective way of reducing pollutant emissions and production cost. In this study, the basic characteristics of anthracite and coke breeze were compared and the sintering performance at Partial substitution of anthracite for coke breeze in iron ore sintering
احصل على السعر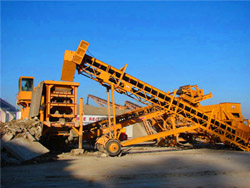
(PDF) Thermodynamic Analysis of Iron Ore Sintering
Abstract and Figures. The sinter process of iron ore with biomass carbon instead of coke breeze as fuel was investigated via thermodynamic analysis in this paper through a comparison of sintersolid fuel in iron ore sintering. Reduction in consumption of primary fuel (coke breeze) without compromising on plant productivity and sinter quality would help in the operational cost reduction as well as in achieving the compliance of regulation related to hazardous emissions from sinter plants. Due to the poor availability of coke breeze inModified coke breeze distribution in iron ore sintering a novel
احصل على السعر
Influence of Sinter Parameters on CO Emission in Iron Ore Sintering
Iron ore sintering is an agglomeration process of iron ore fines, fluxes, fossil fuel (coke and coal), and some iron-bearing waste materials in the ironmaking and steelmaking industry . Sinter is one of the main raw materials used in a blast furnace (BF) accounting for more than 70% ferrous burden of BF in China [ 2 ].Coke breeze is the main heat source in sintering process. Its combustion yields enough amounts of heat which melts the sinter mix. One of the factors that significantly affect the course of coke breeze combustion is its grain size [1,2,3].It is known that fine-grained coke reduces permeability of the sinter mix and the use of coke breeze Effects of Particle Size of Coke on Iron Ore Sintering Process
احصل على السعر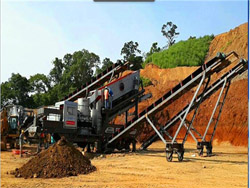
Partial substitution of anthracite for coke breeze in
In the sintering of iron ores, the partial substitution of anthracite for coke breeze has been considered to be an effective way of reducing pollutant emissions and production cost. In this studyOther articles where coke breeze is discussed: iron processing: Sintering: of fine coke (known as coke breeze) within the ore generates the necessary heat. Before being delivered to the sinter machine, the ore mixture is moistened to cause fine particles to stick to larger ones, and then the appropriate amount of coke is added. Initially, coke on the Coke breeze metallurgy Britannica
احصل على السعر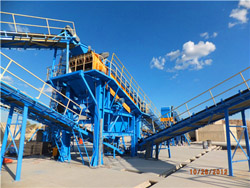
Improvement in Sinter Properties with Reduction in Emissions
In the sintering of iron ores, the partial substitution of anthracite coal for coke breeze has been considered to be an effective way of reducing emissions and improvement in sintering properties. In the present study, the combustion characteristics of the anthracite coal and coke breeze were investigated and its influence on product sinter Iron ore sintering is extensively used in the iron and steel the influence of the morphology of coke breeze granules in sintering and combustion. In Mikka and Loo [35], it wasReview on alternative fuel application in iron ore sintering
احصل على السعر
Sintering: Most Efficient Technologies for Greenhouse Emissions
Minimizing the addition of −0.25 mm coke breeze, maintaining the highest combustion temperature at around 1300 °C, and keeping relatively high oxygen content in atmosphere are expected to promote combustion efficiency of coke breeze and thus energy utilization in iron ore sintering (Ogi et al. 2015).Sintering of iron ores is an enormous energy-intensive and resources consuming process. Introducing a selective waste gas recirculation (SWGR) to the sintering process reduces the energy consumption, stack gas volume flow, and sulfur dioxide emissions of an iron sinter production. Simulating this complex process in flowsheet Model of an iron ore sinter plant with selective waste gas
احصل على السعر
Sintering: A Step Between Mining Iron Ore and Steelmaking
According to the U.S. Environmental Protection Agency, the sintering process converts fine-sized raw materials, including iron ore, coke breeze, limestone, mill scale, and flue dust, into an agglomerated product, sinter, of suitable size for charging into the blast furnace.The production of crude steel in the iron and steel industry in China has grown dramatically, which has made the country the world's largest steel producer since 1996 1 3. 40%–60% of the total iron-containing burden in the blast furnace during ironmaking is sinter 4.The iron ore sintering process is one of the vital steps -in an Partial substitution of anthracite for coke breeze in iron ore sintering
احصل على السعر- ویدئو ها فروش سنگ شکن سنگ
- كسارة الحجر للبيع في الفلبين
- مطحنة الزيتون العصرية للشراء
- cement processing plants sudan
- كم تشغيل كسارة حاسبة
- المدرجة في البورصة لنا
- كسارة صخرية صغيرة تصمم
- used concret crusher
- مطحنة الكرة القدم
- آلات جديدة في طحن الحجر الأملس
- كسارة المطرقة للبيع مستعملة من مصر
- 4 axis mill machines accessories
- المعدات المستخدمة للتعدين عن الذهب
- قائمة صناعات تعدين الفحم في كويمباتور
- خرید معدن آسیاب توپ