اتصل
هاتف
+0086-371-86162511
عنوان
تشنغتشو ، الصين
suface area of grinding media

Comparison of grinding media—Cylpebs versus balls
The two grinding media have different surface area, bulk density and contact mechanisms in grinding action. Comparative tests were conducted using the two types of grinding media in a laboratory Bond ball mill at various conditions of equality Specific surface area. 1. Introduction. Grinding models are usually designed to predict the size distribution of the mill products either as a function of Surface area production during grinding ScienceDirect
احصل على السعر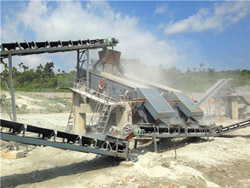
Surface area production during grinding ScienceDirect
The present work explains the reason of such a discrepancy and determines the conditions under which the size analysis of a material can be used to determine its The determination of the surface area production rate allows the identification of the grinding limit and the maximum specific surface area which Surface area production during grinding Request PDF
احصل على السعر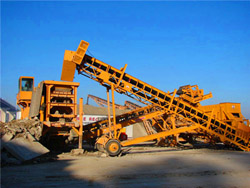
Chapter 6 Wet Grinding in Stirred Media Mills
Grinding and dispersing in stirred media mills is a process, which is widely used in different industries such as chemical, ceramic, pharmaceutical, filler, ink and However, the surface area of each hexagon is 13.2% greater than the surface area of a cylpebs, and the total surface area is 2.28% greater than that of cylpebs. Regarding the contact mechanism Minerals Free Full-Text Breakage Characterization of
احصل على السعر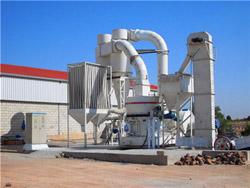
Consumption of steel grinding media in mills A review
Grinding circuit operators have long been aware of the significant impact of grinding media consumption on the cost of grinding. Comminution accounts for an Relationship of the yields of the size fractions in grinding products with the total surface area of the grinding media. Table 1. Percentage of −0.038 mm particles Minerals Free Full-Text Study on the Grinding Law of
احصل على السعر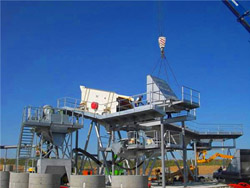
Effects of Grinding Media on Grinding Products and Flotation
This review highlights the influences of grinding media on pulp chemical properties (dissolved oxygen, pulp potential, pH, and ion concentration), particle size It was claimed by the manufacture (Doering International) that for a given charge volume, Cylpebs provide 25% more grinding media surface area for size reduction. The grinding performance of the Cylpebs should then be correspondingly higher compared with the steel balls (Doering website: doering-sinn.de ).Comparison of grinding media—Cylpebs versus balls
احصل على السعر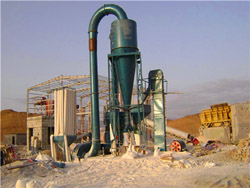
Effect of Grinding Media Size on Ferronickel Slag Ball Milling
consumption is reduced. In order to achieve this, grinding kinetics modeling and the AR approach were used to evaluate data obtained from the milling of slag. The Brunauer– Emmett–Teller (BET) technique was also used to determine the grinding limit and the maximum specific surface area that can be obtained for different operatingSpecific surface area versus specific energy (a) at the initial grinding stages (0–45 min) and (b) at all energy levels studied; grinding media consisted of balls with various sizes (mix denotes a Minerals Free Full-Text Effect of Grinding Media
احصل على السعر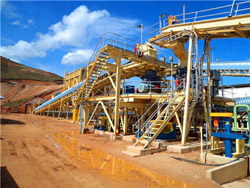
Surface Area of GM PDF Mill (Grinding) Kilowatt Hour Scribd
mic. 5 Grinding media in Tons 40.0 53. 6 % of Filling 26 27. Sp surface area of We get 18.3 m2/ton surface area by. 7 Grinding media m2/ton 18.3 17.5 adding 2 tons of each 25 & 30mm.It. increase of 13% of surface area. 8 flow in m3/hr (CA Fan) 70000 110000. flow across mill out let. 9 66500 104500.Different milling conditions, such as wet or dry, and use of different grinding media have a great impact on the flotation performance of sulphide minerals. In the present study, the effects of wet and dry grinding and the use of different grinding media, such as mild steel (MS) and stainless steel (SS), were investigated on a Cu Minerals Free Full-Text Effects of Different Grinding Media and
احصل على السعر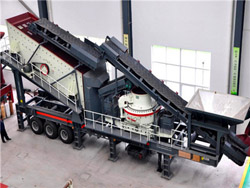
Wear ofgrinding media in the mineral processing industry: An
specific grinding applications. However, the areas of application often overlap,allowing a choice ofmore than one type of media for a given grinding application. The consumption of grinding med ia in the mineral processing industry represents a substantial cost to the comminution process. Second to energy, grinding media isThe grinding equipment is a laboratory rod mill with internal dimensions D × L 203 × 280 mm, rotating at 72 rpm, loaded with 9 kg of rods between 12 mm and 20 mm in diameter. There were three grinding tests each one using 0.5 kg, 1.0 kg and 1.5 kg of crushed quartz respectively. In these tests the feed ratio is defined as the mass ratio of Surface area production during grinding ScienceDirect
احصل على السعر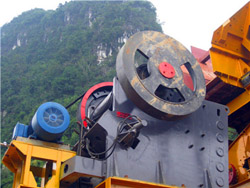
Minerals Free Full-Text Study on the Grinding Law of Ball Media
It can be seen in Figure 5 that when the total surface area of the grinding media was smaller than about 300,000 mm 2, the relationships between the total surface area and the percentages of all discussed size fractions were isotonic, whereas they became non-isotonic and the percentage of the discussed size fractions fluctuated in a sion exist in wet grinding: (1) a large surface area of grinding media, (2) highly conductive milt water, and (3) abrasion that destroys the passive films protecting the meta/ surfaces.Electrochemical Aspects of Grinding Media-Mineral Interaction in
احصل على السعر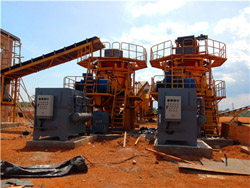
Consumption of steel grinding media in mills A review
mass loss of grinding media per unit surface area, kg m −2. ρ. density of grinding media in general, kg m −3. ρ b. density of steel ball, kg m −3. Ω E. grinding media consumption based on energy usage, kg J −1. Ω M. grinding media consumption based on amount of ore ground, kg kg −1. Ω t. grinding media consumption based onAs can be seen from Fig. 1, the distance between Fe atoms of the three grinding media with different carbon content and the S atoms on the surface of galena is close to 2.2 Å, indicating that the three grinding media all have a strong interaction with the galena surface. The contact distance result of the strong galvanic. ConclusionsGalvanic interaction between different grinding media and
احصل على السعر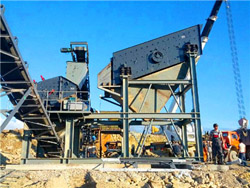
2009 GetsNimbler Union Process
denser the grinding media should be — because larger and heavier media generate greater impact forces. Final particle size also should be considered. The finer the required end particle size the smaller the grinding media should be — because small media make greater surface area available to perform grinding.The reason may be that the advantage of greater surface area is balanced by the line contact and area contact grinding actions with the Cylpebs. A new ball mill scale-up procedure [Man, Y.T., 2001.The Effects of Grinding Media Shape on Breakage
احصل على السعر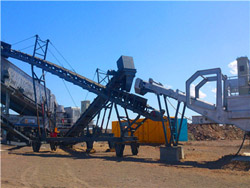
Specific surface areas (SSA) of steel slag under different grinding
The SSA (specific suface area) and the particle diameter of unmodified BOF slag could reach 303.1 m2/kg and 51.75 µm after 10 min of grinding, but that of reconstructed BOF slag could reach 354.5It was claimed by the manufacture (Doering International) that for a given charge volume, Cylpebs provide 25% more grinding media surface area for size reduction. The grinding performance of the Cylpebs should then be correspondingly higher compared with the steel balls (Doering website: doering-sinn.de ).Comparison of grinding media—Cylpebs versus balls
احصل على السعر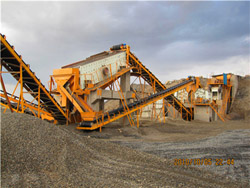
Applied Sciences Free Full-Text Comparison of Grinding MDPI
For example, the specific surface area of untreated steel slag is only 360 m 2 /kg after 60 min grinding, while that of pretreated steel slag reaches 361 m 2 /kg after 40 min grinding, thus 20 min grinding time is saved. The relationship of specific surface area vs. grinding time was fitted, and the result is as follows:As can be seen from Fig. 6, the length of O-S bonds between oxygen molecules and the galena surface are all close to 1.64 Å when oxygen molecules are adsorbed on the galena (1 0 0) surface which contacting with grinding media containing 0.1 %Ce, 0.1 %La, 0.1 %Y, 4.6 %Cr and 1.5 %Mn, indicating that oxygen molecules can Galvanic interaction between different grinding media and
احصل على السعر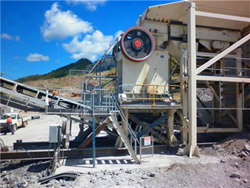
Effect of grinding media on the milling efficiency of a ball mill
The size of grinding media is the primary factor that affects the overall milling efficiency of a ball mill (e.g. power consumption and particle size breakage). This article tackles the lack of a design tool that could help choose the ball loading composition in mills. Such a tool enables the maximization of the exposed surface area per unit energy During grinding with forged steel media, sulphides such as pyrite undergo surface changes due to the occurrence of oxidation–reduction reactions, which affect its depression during the concentration process. For this reason, in this work, the surface modification of pyrite during grinding was studied; FTIR, ICP-OES, XRD and Surface Spectroscopy of Pyrite Obtained during Grinding and Its
احصل على السعر
Galvanic interaction of grinding media with pyrite and its effect
The extent of galvanic interactions between mild steel and pyrite was calculated from the electrochemical parameters. The galvanic current between mild steel and pyrite is dependent on the polarization behaviour, geometric relationship, and species in the grinding environment. The surface area ratio of mild steel to pyrite significantly
احصل على السعر- Cone Crusher Price Standard Malaysia
- حجر محطم نوع الزاحف
- تستخدم كسارة الكوارتز المحمول
- شاشات كسارات الحجر
- Mica Grinding Mill In Korea
- الفك محطم ملامح العملية
- مصنعي آلات كسارة الحجر دلهي
- بيع كسارات الحجارة المستخدمة على المسار
- mekanisme pengolahan pasir
- معدات الرمل في سيدني
- كسارة مخروطية ثانوية للبيع في أوروبا الشرقية
- تجهيز الفحم تدفق سحق vsd
- price range for ballast crushing equipment sand and gravel conveyors
- ماشین آلات خرد کردن سنگ پاکستان
- الألومنيوم اليدوي محطم