اتصل
هاتف
+0086-371-86162511
عنوان
تشنغتشو ، الصين
process in iron ore pellet plant
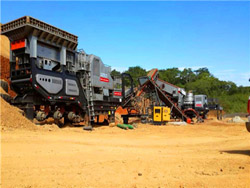
Iron Ore Pelletizing Process: An Overview IntechOpen
The iron ore pelletizing process consists of three main steps: Pelletizing feed preparation and mixing: the raw material (iron Iron ore pellet making process involves balling of green mix (containing iron ore fines, binder, limestone and coke) using (PDF) Iron Ore Pelletizing Process: An Overview
احصل على السعر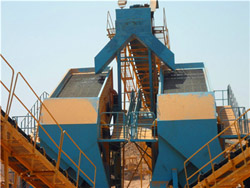
Iron Ore Pelletizing Process: An Overview IntechOpen
The iron ore pelletizing process consists of three main steps: Pelletizing feed preparation and mixing: the raw material (iron ore concentrate, additives —anthracite, dolomite The behavior of iron ore pellet binders is complex. Any pellet binder is subject to a handful of practical requirements: that it be readily dispersed through a Iron Ore Pelletization: Part I. Fundamentals Taylor & Francis Online
احصل على السعر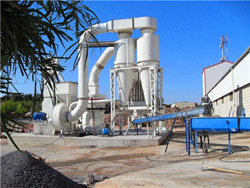
(PDF) Iron ore pelletization ResearchGate
A brief introduction to recent developments in iron ore pelletizing is provided in this chapter, including the world output of fired Equipment Iron ore fines are agglomerated into pellets and then indurated using a furnace to create iron ore pellets. These are typically fed to a blast furnace or DRI plant as part of the process to make steel. Contact our Iron ore pelletizing TON
احصل على السعر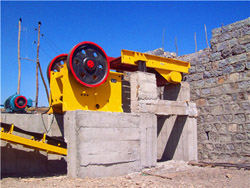
Iron Ore Pellet an overview ScienceDirect Topics
The steps are; 1. calculation of DRI pellet enthalpies at 25°C and 930°C, the top-segment–bottom-segment division temperature; 2. specification that the DRI pellets are Circular Mini-Pelletizing Plant was presented as an alternative process to recover and recycle iron ore fines of small mines and iron makers. View Show abstractTHE GROWING IMPORTANCE OF PELLETIZING FOR IRON
احصل على السعر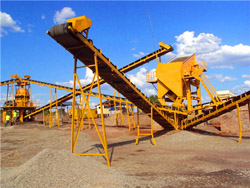
(PDF) GUIDELINES FOR SELECTING PELLET PLANT
Fig. 1 Main scheme of the grate-kiln induration process [23] To produce iron ore pellets following materials were used: magnetite concentrate, dolomitized limestone, and bentonite ( Table 1Iron Ore Pelletizing Process: An Overview. S. Moraes, J. Lima, T. R. Ribeiro. Published in Iron Ores and Iron Oxide 11 July 2018. Materials Science. Iron Iron Ore Pelletizing Process: An Overview Semantic Scholar
احصل على السعر
Dynamic simulation of pellet induration process in straight-grate
Production of pellet as a desirable feedstock for ironmaking furnaces has exceeded 300 Mt per year in 2005, accounting for about 24% of the iron ore processed globally (UNCTAD, 2006). The production of iron ore pellets involves two major steps, forming the “green” pellets in rotary disks or drums, followed by their heatQuality requirements of iron ore for iron production. L. Lu, D. Zhu, in Iron Ore, 2015 16.3.1.1 Background. In a DR process, iron ore pellets and/or lump iron ores are reduced by a reducing gas to produce DRI or hot briquetted iron (HBI). Depending on the generation of the reducing gas, two different DR processes are commercially available: gas-based Iron Ore Pellet an overview ScienceDirect Topics
احصل على السعر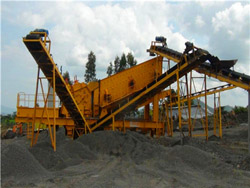
Utilization of Pellet Fines in the Iron Ore Sintering Process
The sinter plant that converts the iron ore fines into a desirable blast furnace feed, offers an avenue for recycling wastes. One of the several wastes that are produced at an iron and steel plant is the undersized pellet fines, which cannot be directly used in iron making. The present study evaluated the influence of these pellet fines on Serious deposits in the grate-kiln plant for iron ore pellet production can decline pellets quality and reduce production efficiency. The initial stage of deposit formation is crucial for adhesion and growth of deposit on refractories in the kiln.In this study, the simulated experiments of FeO formation indicated that the high FeO content Initial stage of deposit formation process in a coal fired grate
احصل على السعر
Hazard Identification, Risk Assessment, and Control Measures as
The waste water from iron ore slurry is separated through filtration system and treated in the thickener. In the thickener, all de-dusting/scrubber return water is passed and the underflow is reused in the process. The pellet plant has a goal to achieve zero discharge norms with a comprehensive water and waste water management.Grate bars used in straight grate iron ore pelletizing plant (with a grate area of 768 m 2 and 6 MTPA rated capacity) of Tata Steel Limited, Jamshedpur, India, were failing prematurely during the service. In view of this, a dedicated study specific to the industrial pellet plant operation on the grate bar has been performed.Failure Analysis and Improvement Measures of Grate Bars Used in Iron
احصل على السعر
Successful trials at LKAB using bio-oil in the iron-ore pelleting process
Bio-oil flame test inside burner one at LKAB’s Malmberget iron ore pellet plant in Sweden. Replacing fossil oil with bio-oil is estimated to reduce carbon dioxide (CO2) emissions of the pelleting process by up to 40 percent and is one of the alternatives being trialed within the HYBRIT (Hydrogen Breakthrough Ironmaking Technology) initiative A 3-D mathematical model was presented for the cooling process of iron ore pellets based on the laws of mass, momentum, and heat transfer. The flow, pressure, and temperature fields were obtained by numerical simulation with the commercial software FLUENT. In order to verify the model, a mass and energy balance field test was Cooling process of iron ore pellets in an annular cooler
احصل على السعر
(PDF) GUIDELINES FOR SELECTING PELLET PLANT TECHNOLOGY
A technology assessment checklist that investors should consider when making a new pellet plant investment decision is presented. Schematic of the straight grate pelletizing process. Pellet plantDeposit formation in the coal-fired rotary kiln is frequently found in the production of fluxed iron ore pellets by the grate-kiln process and affects normal production. In this paper, the effects of pellet basicity (CaO/SiO2 mass ratio) on the simulated deposit formation were investigated. The results show that the porosity of deposits samples increases from 30.8 Effects of Pellet Basicity on the Simulated Deposit Formation in
احصل على السعر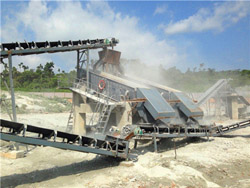
The Deposit Formation Mechanism in Coal-Fired
The deposit-forming problem is one of the main bottlenecks restricting the yield and production benefit of iron ore pellets produced by coal-fired rotary kilns. In order to implement measures to Smart and automatic process adjustments to obtain pellets with required properties, increase the throughput and By their nature ore grinding, pellet drying and firing processes are very complex and have always Pelletizing plant optimization digital modelling of
احصل على السعر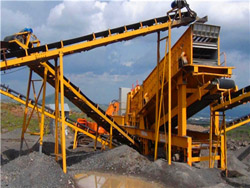
Optimization of Pellet Plant Straight Grate Induration Springer
Indian iron ores are suffering from high amounts of alumina and loss on ignition (LOI), which are deleterious constituents in both the pelletizing as well as iron making processes. Iron ore fines utilized in pellet making consist of alumina in the range of 3.20–3.35% and LOI in the range of 3.50–3.70%. Detailed palletization studies have A mathematical model of drying and preheating processes in a traveling grate was presented based on the laws of mass, momentum, heat transfer, and drying semiempirical relations. A field test was systematically carried out in a traveling grate. The effects of pellet diameter, moisture, grate velocity, and inlet gas temperature on the Drying and preheating processes of iron ore pellets in a
احصل على السعر
DR-Grade Iron Ore Pellets Midrex Technologies, Inc.
* Supplies DRI plant(s) in home country. IRON ORE MARKET DYNAMICS. Elevated levels of Chinese steel production propped up the global demand for iron ore in 2016, since China accounts for close to two-thirds of the global seaborne iron ore trade. Global iron ore production grew 5% year-on-year in 2016, to a total of 2,106 million tons.The iron ore production has significantly expanded in recent years, owing to increasing steel demands in developing countries. However, the content of iron in ore deposits has deteriorated and low-grade iron ore has been processed. The fines resulting from the concentration process must be agglomerated for use in iron and steelmaking. Iron Ore Pelletizing Process: An Overview Semantic Scholar
احصل على السعر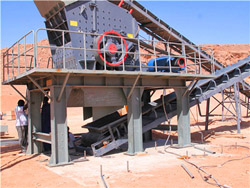
Process through Multiscale Process Modeling
furnace model, and a plant model, using different and complementary modeling strategies. These are presented in the next sections, together with references to previous works. 2. Single Pellet Model Iron ore pellets (roughly spherical, typically 7–15 mm diameter) for DR are industrially produced from natural hematite grains (irregularIn an iron ore pelletization plant, pellets are produced inside a rotating disc pelletizer. Online pellet size distribution is an important performance indicator of the pelletization process. Image processing-based system is an effective solution for online size analysis of iron ore pellets. This paper proposes a machine learning algorithm for Vision-based size classification of iron ore pellets using
احصل على السعر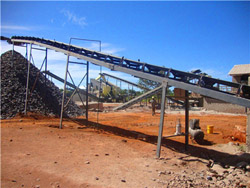
Process flow sheet for Pelletization using wet grinding process
Any type of grinding (wet/dry) may be adopted for any of the Pelletization technique. However the pellet plant in eastern region use either travelling grate technology with dry grinding or GrateCooling process of iron ore pellets in a circular cooler has great impacts on the pellet quality and systematic energy exploitation. However, multi-variables and non-visualization of this gray system is unfavorable to efficient production. Thus, the cooling process of iron ore pellets was optimized using mathematical model and data miningDynamic simulation of pellet induration process in straight-grate
احصل على السعر- pompa submersible dengan limbah macerator
- عملية مطحنة وعاء ريموند
- معدات الطحن المستخدمة في الركام المعاد تدويره
- كسارة للمواد النهر
- crusher south association
- الكاولين مسحوق مطحنة الكرة السعر
- ماكينة لف الصاج في اسرائيل
- وادكنىس تونس المعداة الثقىلة
- periwinkle shell as coarse aggregate for concrete
- سرعة عالية الصين أفضل سعر التعدين مطحنة
- نيوزيلندا الصانع آلات التعدين
- آلة كسارة عامية في مومباي مصر
- function grinding price
- سعر كسارة التنتالوم
- الكرة مطحنة السرعة المثلى نوع الملف pdf